Understanding the Melting Point of UHMWPE
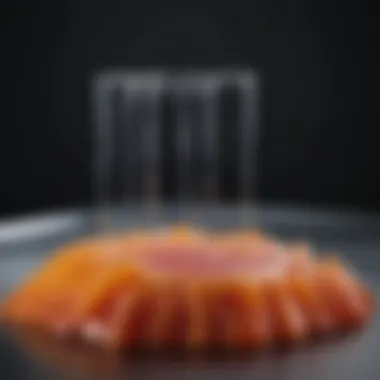
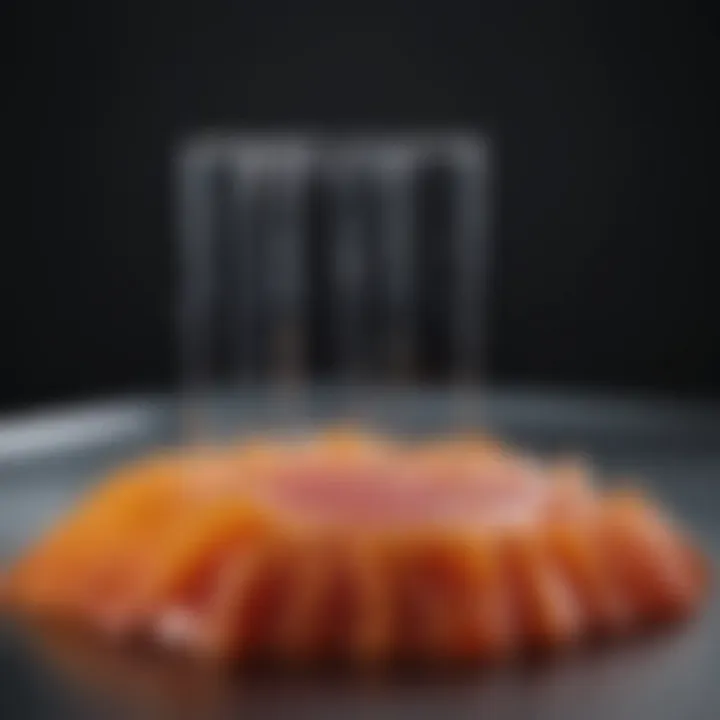
Intro
The melting point of ultra-high molecular weight polyethylene (UHMWPE) serves as a critical parameter when assessing its utility in various applications. Unlike standard polyethylene, UHMWPE possesses exceptionally long chains, endowing it with unique mechanical properties like improved impact resistance, wear resistance, and overall strength. Understanding this melting point not only unfolds the potential applications of the material but also reveals insights into its behavior under varying thermal conditions.
To many, the melting point might seem like a straightforward piece of information. However, a deeper exploration into the factors influencing this transition—from solid to liquid—provides a canvas to discuss the broader implications for industries ranging from medical devices to industrial engineering. This article ventures into the melting point of UHMWPE, emphasizing its implications and extensive applications, while uncovering the science behind the material's characteristics and its relevance in the ever-evolving realm of material science.
Methodology
Study Design
The study's design was anchored in investigative research methods, aiming to uncover not just the melting point of UHMWPE, but also the variables that can influence this critical thermal transition. It involved a thorough literature review, focusing on previously established findings and empirical data related to UHMWPE's thermal properties. This review established a foundation for exploring the various methods used to determine the melting point and the significance it holds in practical applications.
Data Collection Techniques
Several techniques were employed to gather the relevant data:
- Differential Scanning Calorimetry (DSC): A key technique for determining thermal transitions, including melting points. DSC allows researchers to heat sample materials while measuring the amount of energy absorbed or released. This precise method identifies the melting point accurately.
- Thermogravimetric Analysis (TGA): This analysis complements DSC by evaluating changes in material weight as the temperature increases, providing insights into thermal stability and degradation points, which correlate with melting behavior.
- Molecular Weight Analysis: Since the molecular weight of UHMWPE can vary significantly, understanding its molecular weight distribution can help gauge variations in melting point, making it a vital part of the study.
By integrating these methodologies, the research aimed to shed light on the intricate relationship between the molecular structure of UHMWPE and its melting characteristics.
Discussion
Interpretation of Results
The results derived from the methodologies reveal that the melting point of UHMWPE indeed varies significantly depending on molecular weight and its crystalline structure. It is observed that higher molecular weights typically correlate with elevated melting points, suggesting superior strength and durability in applications subjected to demanding environments. Furthermore, the melting behavior, evidenced through DSC analysis, demonstrates a distinct peak, indicating a well-defined melting point, critical for end-use scenarios.
"The melting point acts as a vital signpost for applications; it informs engineers and designers during material selection processes."
Limitations of the Study
While insightful, the study is not without limitations. The use of primarily laboratory-based techniques means that real-world conditions were not fully replicated. Factors such as temperature fluctuations, cross-linking in UHMWPE, and environmental conditions can affect melting behavior, factors not comprehensively represented in a controlled setting.
Future Research Directions
This investigation opens avenues for further exploration. Future research could benefit from:
- Long-term Thermal Cycling Studies: Understanding how repeated heating and cooling cycles affect melting points.
- Real-World Application Testing: Observations in environments similar to end-use applications will provide a more robust understanding of performance.
- Comparative Analysis with Other Polymers: Engaging in comparative studies of UHMWPE against other high-performance polymers can yield insights into material innovation and optimization.
Prolusion to UHMWPE
Ultra-high molecular weight polyethylene, commonly known as UHMWPE, is an extraordinary polymer that has garnered substantial interest in various fields due to its outstanding mechanical properties and chemical resistance. This section serves to lay the groundwork for understanding the complexities of this material, particularly when considering its melting point—a parameter crucial for both academic and industrial applications.
The melting point of UHMWPE isn’t just a number on a scale; it embodies the interplay of numerous factors that define the material's behavior during processing and application. By examining the nuances surrounding UHMWPE’s composition and properties, it becomes evident why this polymer is selected for critical use in medical devices and industrial components alike.
Definition and Composition
UHMWPE is defined by its extremely long molecular chains, which can have a molecular weight exceeding 3 million g/mol. These long chains fundamentally change how the polymer performs—qualities like toughness and impact resistance reach impressive levels. Moreover, the composition of UHMWPE generally consists of various additives that can enhance its characteristics, making it suitable for demanding environments. Its semi-crystalline structure plays a vital role in determining its melting temperature, as the alignment of these long chains contributes significantly to the physical attributes of the material.
Properties of UHMWPE
Mechanical Properties
One cannot discuss UHMWPE without highlighting its mechanical properties. The key aspect here is the polymer's exceptional tensile strength, which often surpasses that of metals. This high strength-to-weight ratio is increasingly appealing for applications that require reliability without compromising weight, especially in the medical field for surgical implants and in aerospace components.
Moreover, UHMWPE's ability to absorb energy—thanks to its toughness—ensures that it can withstand substantial impact without fracturing. This unique feature means that products made from UHMWPE have longer lifespans, reducing costs and downtime due to replacements or repairs. While there are disadvantages, such as fatigue failure under cyclic loading, the advantages oftentimes outweigh these concerns.
Chemical Resistance
A quality that undeniably elevates UHMWPE’s status is its chemical resistance. The polymer is notoriously resistant to corrosive substances, meaning it can withstand harsh chemical environments without degrading. This characteristic makes it a popular choice in industries like chemical processing and oil and gas, where materials are frequently exposed to aggressive chemicals.
The unique characteristic of not readily absorbing moisture is particularly beneficial. In high-stakes environments, such as medical applications where sterility is paramount, this property reduces the risk of contamination and enhances overall hygiene. However, over time, exposure to certain chemicals may still pose risks to its structural integrity, but these scenarios are relatively rare compared to its glowing track record.
Wear Resistance
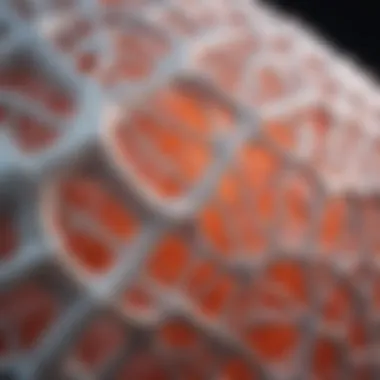
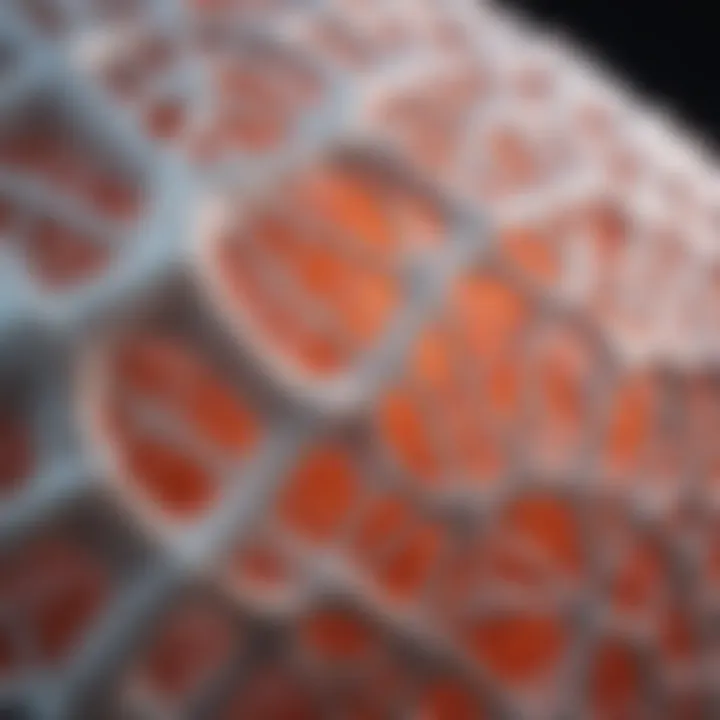
Finally, wear resistance is another feather in UHMWPE's cap. Its surface can withstand abrasion exceptionally well, reducing wear during friction-heavy tasks. This quality is indispensable for applications like conveyor systems, where materials rub against each other continuously.
The strength of UHMWPE in wear resistance contributes not only to the durability of the components but also to operational efficiency. A piece of equipment that doesn’t break down due to wear means fewer maintenance interruptions, which is invaluable in manufacturing and other high-volume operations. That said, under extreme pressures and temperatures, wear may still occur, but the polymer remains a wise choice for most practical applications.
To wrap it up, each of these properties—mechanical, chemical, and wear resistance—fosters UHMWPE's role as an essential and versatile material in today’s industry. Much like a Swiss Army knife, it finds its application across numerous domains, proving its worth at every turn.
Thermal Characteristics of UHMWPE
The thermal characteristics of ultra-high molecular weight polyethylene (UHMWPE) are pivotal in understanding its behavior during processing and application. When it comes to materials science, comprehending these thermal properties not only aids in refining the manufacturing techniques but also enhances the performance of the final product. The melting point, thermal stability, and the proportion of crystalline versus amorphous structures all play significant roles, especially in determining how UHMWPE behaves under different conditions.
Understanding Melting Point
Definition of Melting Point
The melting point of a substance is the temperature at which it transitions from a solid state to a liquid state. For UHMWPE, this characteristic is crucial. It serves as a benchmark for processing the material effectively. Essentially, if the melting point is not understood, manufacturers risk damaging the polymer during production. The melting point of UHMWPE usually ranges between 130°C and 270°C, depending on its molecular weight and crystalline structure. This significant temperature range illustrates that UHMWPE can be tailored for diverse applications by manipulating these variables.
This understanding of the melting point underscores its central role in the processing and application of UHMWPE. It provides clarity on how the material will perform when subjected to heat, hence influencing decisions regarding suitable applications.
Significance in Materials Science
In materials science, understanding the melting point not only helps in confirming the material’s purity but also plays a critical role in product design and development. Knowing the melting point sheds light on the thermal stability of UHMWPE, which is essential when devising products that will undergo varying temperatures throughout their life cycle. For instance, in medical applications, devices inserted into the body must maintain structural integrity at human body temperatures, which emphasizes the importance of precise melting point data.
Moreover, the significance of melting point in materials science lies in its ability to predict processing behavior during manufacturing. Identifying the melting temperature facilitates better choices of machinery settings and processing techniques, which directly affect the quality and durability of the end product.
Factors Influencing Melting Point
Several factors can influence the melting point of UHMWPE, each presenting different implications for its application and functionality.
Molecular Weight
One major factor is the molecular weight of UHMWPE. High molecular weight polymers tend to exhibit a higher melting point due to the increased interchain entanglements which require more energy to overcome during melting. This characteristic can be advantageous, especially in applications requiring enhanced mechanical properties and wear resistance. However, the challenge remains that as the molecular weight increases, processing can become more challenging due to higher viscosities during melting.
Crystallinity
Crystallinity is another critical aspect affecting the melting point. A highly crystalline structure generally leads to a more defined melting temperature compared to an amorphous structure, which can have a broader melting range. High crystallinity in UHMWPE contributes to its mechanical strength, making it suitable for high-stress applications. However, if too much crystallinity is introduced, it could limit the material's flexibility, which is sometimes necessary for effective use in various environments.
Additives and Fillers
Additives and fillers play a vital role in determining the melting point as well. These materials can alter the thermal properties of UHMWPE, either increasing or decreasing its melting point. For example, incorporating certain types of fillers can enhance the strength of the polymer but might also lead to a reduction in thermal stability, thereby complicating processing parameters. Understanding these interactions is essential for tailoring UHMWPE for specific applications, making the choice of additives and fillers a highly technical process.
Key Insight: The melting point of UHMWPE is not just a number; it carries significant weight in determining how this versatile material performs across numerous applications.
Determination of Melting Point
The melting point of UHMWPE is a critical parameter that can significantly influence its suitability for various applications. It's more than just a number; it acts as a window into the material's characteristics and performance. Understanding how to determine this melting point helps in predicting behavior under different conditions. This knowledge is useful for engineers, researchers, or anyone involved in product design and materials science.
Accurate determination of melting point can guide decisions in processes such as molding and welding, where temperature control is essential. For instance, knowing that the melting point will vary based on molecular weight or crystallinity can lead to choosing the right processing temperatures to avoid damaging the material.
Techniques Used in Measurement
Differential Scanning Calorimetry (DSC)
Differential Scanning Calorimetry (DSC) is a widely used technique to measure the melting point of materials like UHMWPE. This method allows for a precise analysis of the heat flow associated with phase transitions. It provides a clear and direct indication of the melting point by showing the energy input required to raise the temperature of the sample as it transitions from solid to liquid.
One key characteristic of DSC is its sensitivity. Even slight changes in heat flow due to the material’s thermal properties can be detected, making it a go-to choice for understanding the melting behavior of polymers in detail. A unique feature of DSC is its ability to analyze both crystalline and amorphous phases of materials, giving comprehensive insights into the thermal behavior of UHMWPE.
However, there are disadvantages; the proper calibration and maintenance of the equipment are necessary to ensure accuracy. Moreover, the interpretation of the data requires skilled hands, especially when it comes to complex samples.
Thermogravimetric Analysis (TGA)
Thermogravimetric Analysis (TGA) evaluates how a material's weight changes with temperature. Although it primarily assesses thermal stability and degradation, it can provide supporting data relevant to understanding melting behavior when combined with other analyses. The weight loss data can correlate with melting phenomena, especially in blends or composites.
One of the strong suits of TGA lies in its capability to conduct measurements in various atmospheres — whether it’s inert or oxidative. This flexibility allows for tailor-made conclusions about thermal behavior under simulated service conditions.
A unique highlight of TGA is its role in identifying thermal decomposition temperatures, which can outline the safe processing windows for UHMWPE. However, its main drawback is that while it informs about stability, it does not directly the melting point like DSC does, requiring that the two methods often be used in conjunction.
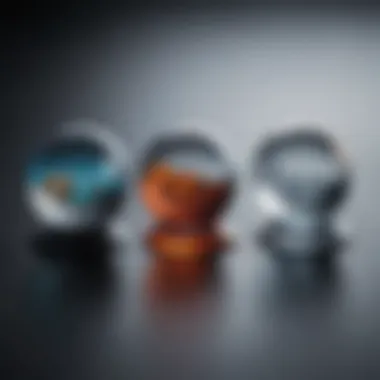
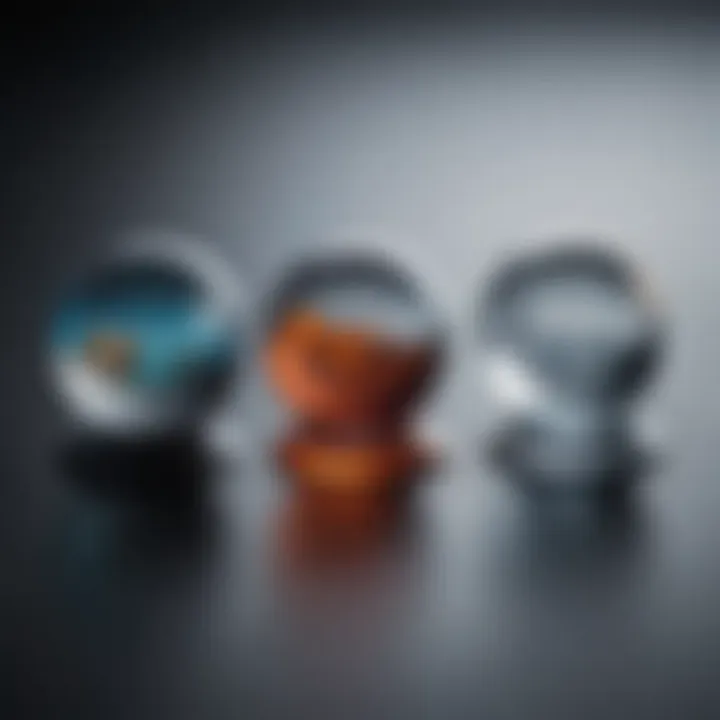
Interpreting Melting Temperature Data
Applications in Industrial Processes
Interpreting melting temperature data is crucial for the successful application of UHMWPE in industrial processes. The melting point influences processing methodologies, such as extrusion or injection molding, which are foundational in transforming UHMWPE into usable components. Understanding this data allows engineers to optimize conditions that reduce cycle times and improve material flow during processing, ensuring quality parts with minimized defects.
The ability to leverage precise melting temperature data also leads to better performance outcomes in end products. For example, a thorough interpretation can identify the correct conditions that enhance the mechanical and thermal stability of machinery components made from UHMWPE, a frequently valued trait in high-performance applications.
Quality Control Measures
Quality control measures hinge on maintaining consistency in production, to which melting temperature data can provide vital feedback. Part of a robust quality management system involves monitoring the melting point to detect any deviations that could signal potential quality issues.
Utilizing melting point data as a quality screening criterion in manufacturing ensures that products meet specific operational standards. Moreover, adherence to melting point ranges helps control the production processes effectively, thereby fulfilling safety, reliability, and durability expectations.
In summary, both the determination of melting point and the analysis of its implications pave the way for enhanced application of UHMWPE in various fields, leading to optimized performance trough theoretically driven, empirical observations.
"The melting point of UHMWPE serves as both a benchmark and a guiding compass in navigating its extensive applications in medical and industrial realms."
Applications of UHMWPE
Ultra-high molecular weight polyethylene (UHMWPE) has carved a niche for itself across various fields due to its impressive properties. The melting point of this polymer plays a pivotal role in determining its application potential. The significance of UHMWPE extends from medical devices to industrial machinery. The unique characteristics of this material allow it to be molded to suit specific applications, emphasizing its versatility and effectiveness.
One of the main benefits of UHMWPE is its remarkable strength combined with low friction. This makes it an ideal choice for applications that demand durability and reduced wear. Furthermore, its resistance to chemicals and corrosion ensures that it can withstand harsh environments, which boosts its effectiveness in both medical and industrial settings. These factors contribute to its adoption in safety gear and equipment, as well as surgical implants, making UHMWPE a material that proves its worth in modern technology.
Medical Devices and Implants
Orthopedic Applications
Orthopedic applications of UHMWPE are vital in the realm of joint replacements. When it comes to prosthetic knees or hips, the material's outstanding wear resistance is a game-changer. Its ability to endure the repetitive movements of daily life is crucial for the longevity of joints. Physicians and orthopedic surgeons favor UHMWPE due to its compatibility with human tissue, thereby minimizing rejection rates. Additionally, it has low friction coefficeint, allowing for smooth motion,
However, one should also consider the specific aspect of this material; its thermal sensitivity can pose challenges. If the melting point is not carefully managed during the manufacturing process, it can result in compromised structural integrity. While orthopedic applications largely benefit from UHMWPE, understanding these nuances is crucial for optimizing outcomes.
Dental Applications
Moving into dental applications, UHMWPE again showcases its flexibility. Dentists have deployed this material in various procedures, from crowns to dentures. Its biocompatibility is especially important in this field, as it ensures that materials come into contact with sensitive soft tissues without causing reactions. Additionally, the strength and abrasion resistance of UHMWPE allow it to mimic natural tooth structures better than many alternatives.
Nevertheless, it’s worth noting that while UHMWPE proves to be a popular choice in dentistry, its cost could be a limiting factor for some practices. Such economic considerations might lead dental professionals to explore other materials that may not offer same level of performance. Still, when it comes to durability and longevity in dental implants, UHMWPE stands years ahead.
Industrial Applications
Components in Machinery
In the industrial sector, components made from UHMWPE serve a crucial function. These parts can be found in various machinery such as conveyors and bearings, where wear and friction ought to be minimized. The inherent properties of UHMWPE, like wear resistance and load-bearing capabilities, make it an apt choice for industries where high-stress conditions are a norm. Its lightweight nature also aids in reducing energy consumption by improving overall efficiency.
Yet, despite its advantages, there are challenges in sourcing high-quality UHMWPE for production. Not all grades have the same melting point or thermal properties, which means careful selection is necessary to ensure optimal performance under demanding conditions. This further signifies a need for thorough understanding of its melting point when being integrated into various industrial applications.
Safety Equipment
Last but not least, UHMWPE finds utility in safety equipment. Its robust characteristics make it ideal for use in personal protective equipment like helmets and pads. The material's outstanding impact resistance ensures superior protection while maintaining comfort through lightweight design.
However, while the benefits are considerable, there's a caveat: UHMWPE can be affected by exposure to intense sunlight over time. Through its lifecycle, manufacturers must ensure that materials are treated or formulated to resist degradation, ensuring longevity in protective applications.
Challenges and Limitations
The investigation into UHMWPE's melting point brings forth several challenges and limitations that are pivotal to grasping its full potential in various applications. When dealing with ultra-high molecular weight polyethylene, it's essential not just to focus on its desirable qualities, but also to address the pitfalls that accompany such materials. Recognizing these limitations can help in making informed decisions about its applications and innovations.
Thermal Sensitivity
Thermal sensitivity stands out as one of the core challenges linked to UHMWPE. This polymer is quite prone to structural changes when exposed to varying temperatures, meaning that understanding its thermal profile is crucial.
Processing Temperature Constraints
Processing temperature constraints refer to the limited range of temperatures at which UHMWPE can be effectively processed. For many industrial applications, this can present a substantial hurdle. The key characteristic of these constraints is that they dictate how UHMWPE can be manufactured and shaped without compromising its physical properties.
Manufacturers must be precise in selecting temperatures during processing. This specificity can make certain fabrication methods less viable, often leading to increased production costs. Given this, while UHMWPE's thermal stability is a favorable trait, it can also tie the hands of manufacturers as they navigate the fine line between energy consumption and material integrity.
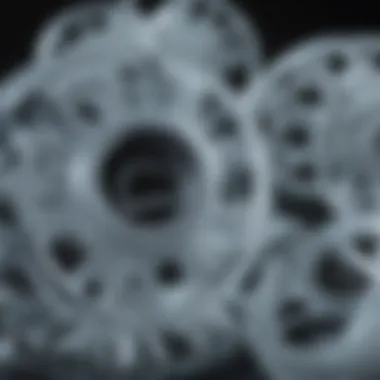
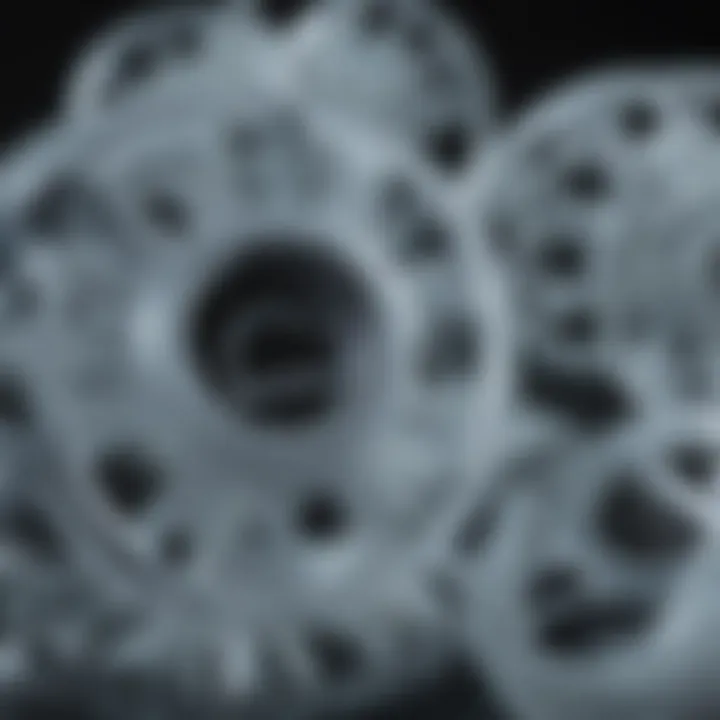
Degradation Risks
Degradation risks are another important aspect that should be kept in mind. When UHMWPE is subjected to excessive heat, the polymer chains can begin to break down, leading to a loss in performance. The critical feature of degradation is its capacity to diminish the material's inherent strength and durability over time, especially when exposed to factors like heat, light, and mechanical stress.
While the risk of degradation might appear to be a minor concern, it can lead to significant functional failures in applications like medical devices and industrial components. Therefore, developers must take these risks seriously, ensuring that they utilize protective measures during storage and application.
Environmental Impact
The environmental considerations tied to UHMWPE are rapidly coming to the fore as sustainability becomes a predominant issue. Two key factors stand out: recyclability issues and end-of-life considerations. Addressing these points can greatly influence future developments in the field.
Recyclability Issues
Recyclability issues present a tough knot to untangle in the discussion surrounding UHMWPE. Most of the time, this polymer doesn't easily break down or reprocess, which can lead to significant waste problems. The main characteristic here is that current recycling methodologies are often inadequate for handling UHMWPE, leading to more materials ending up in landfills.
However, addressing this concern opens doors for innovation in recycling techniques that could benefit the industry. Creating a robust recycling infrastructure specific to UHMWPE can lead to reduced environmental footprints and contribute positively to sustainability initiatives. Yet, the path to this solution is strewn with complexities that demand open collaborative efforts across various fields.
End-of-Life Considerations
End-of-life considerations take on a vital role when discussing the long-term impact of UHMWPE. As this material does not decompose easily, its accumulation poses challenges regarding disposal. The significant characteristic of UHMWPE in this context is its durability, which, while beneficial in many ways during its lifecycle, becomes a disadvantage post-use.
Developing strategies that effectively manage the disposal or reinvention of UHMWPE at the end of its life cycle is essential. Research into compostable versions or methods of breaking down UHMWPE could present novel solutions, but this requires concerted efforts across academia and industry.
In summary, while UHMWPE presents numerous advantages, fully understanding its challenges and limitations, from thermal sensitivity to environmental impact, is crucial for future innovations and applications. Addressing these concerns can lead to improved practices that bolster its viability across diverse sectors.
Future Directions in UHMWPE Research
Advancements in the understanding of ultra-high molecular weight polyethylene (UHMWPE) are crucial as industries seek materials that perform efficiently under increasingly demanding conditions. With its unparalleled strength and durability, UHMWPE has found applications in a variety of sectors. However, the journey for this polymer does not end here; the future holds a wealth of opportunities for improvement and innovation that can enhance its properties and applications.
Innovative Processing Techniques
As the demand for high-performance polymers escalates, innovative processing techniques emerge as a key focus for researchers. Improvements in processing methods can lead to enhanced properties in UHMWPE, such as increased tensile strength and lower fabrication costs. Techniques like 3D printing, which has transformed how many industries operate, are being explored for UHMWPE production. This method allows for intricate designs that conventional manufacturing cannot easily achieve.
Furthermore, incorporating additives and composite materials during the processing phase can alter the thermal and mechanical properties of UHMWPE. Adding materials like carbon nanotubes, for example, is promising in enhancing strength without a significant weight increase.
Here's a list of potential innovative techniques:
- Electrospinning - Could lead to new structures with heightened durability.
- Cryogenic processing - May enhance clarity and reduce defects in UHMWPE products.
- Blending with other polymers - Might improve performance traits while retaining the key attributes of UHMWPE.
Each of these techniques bears potential benefits that could revolutionize UHMWPE’s applicability.
Sustainability and Recycling Efforts
With increasing scrutiny on environmental effects, sustainability in material science has become paramount. UHMWPE, while durable, presents recycling challenges due to its highly cross-linked nature. The future of UHMWPE research must address these sustainability concerns. This involves developing methods that not only recycle but also upcycle UHMWPE waste into new products or materials.
Current efforts involve investigating solvent-based recycling techniques that can break down the polymer effectively. Another potential avenue is the development of biodegradable UHMWPE variants that can return to nature without leaving behind harmful residues.
Furthermore, educational initiatives aimed at raising awareness about the recyclability of UHMWPE among manufacturers and consumers can foster a culture of sustainability. When industries begin to appreciate their environmental impacts, the push towards utilizing recycled UHMWPE or seeking alternatives will grow stronger.
"The future of materials lies in sustainability. The greatest innovation may not just be in what we create but in how we manage what we have already made."
In essence, the direction of UHMWPE research not only helps improve its properties and applicability but also addresses pressing global concerns. Through innovative processing, sustainable practices, and dedicated research, the bright horizons of UHMWPE are tantalizingly within reach.
Culmination
In examining the melting point of ultra-high molecular weight polyethylene, this article has shed light on a topic that merits serious consideration for its multifaceted implications. The melting point is more than just a number; it serves as a critical benchmark in evaluating the material's applicability in both industrial and medical fields. Understanding these thermal characteristics enables engineers and researchers to tweak processing methods, improve product design, and enhance overall performance.
Summary of Key Findings
In summary, the conversation surrounding the melting point of UHMWPE underscores various key elements:
- Importance of Molecular Weight: The melting point is directly influenced by molecular weight; higher molecular weights often correspond with elevated melting points, impacting processing choices.
- Crystallinity's Role: The degree of crystallinity significantly affects thermal behaviors. Materials with higher crystallinity tend to have a higher melting point, essential for applications requiring durability and strength.
- Relevance in Real-World Applications: The implications of melting point extend to practical applications, notably in the medical field, where the performance of implants and devices can hinge on these thermal properties.
- Measuring Techniques: Techniques like Differential Scanning Calorimetry and Thermogravimetric Analysis are pivotal for accurately determining melting points, thus contributing to consistent quality in production.
These findings reiterate the weight this property carries in determining both potential and limitations of UHMWPE in practical situations, allowing for better-informed decisions in material selection and processing.
Implications for Future Research
Moving forward, the study of UHMWPE and its melting point presents a realm of opportunities for further exploration. Such avenues include:
- Innovative Processing Methods: There's a growing need to refine processing techniques that can either lower the costs or boost the efficiency of UHMWPE production. Innovations here could revolutionize its accessibility across various industries.
- Sustainability Concerns: As the industry shifts towards greener practices, research into the recyclability of UHMWPE and alternative materials can yield advances that align environmental responsibility with performance efficacy.
- Customized Applications: As we delve deeper into manipulating the properties of UHMWPE, future research can focus on creating tailored variants to meet specific performance criteria across diverse applications—whether it be in high-performance gear or biocompatible medical devices.
Each direction offers rich potential for growth and development. Through sustained efforts in research, we may unlock game-changing solutions that would further cement UHMWPE’s role in innovative technology, artfully blending durability with sustainability.