Revolutionizing Industries with Circuit 3D Printing
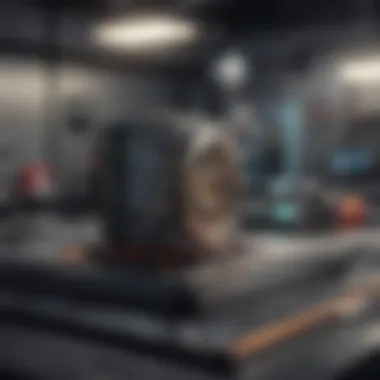
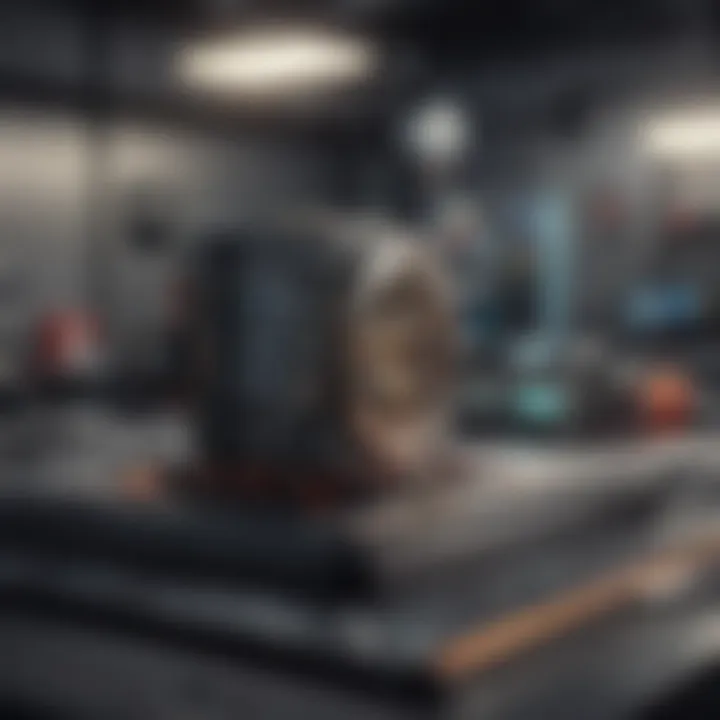
Intro
Circuit 3D printing represents a notable shift in the way electronic circuits are designed and manufactured. Traditionally, circuit fabrication involved complex processes that often resulted in lengthy production times and high costs. However, with advancements in 3D printing technologies, it is now possible to manufacture intricate circuits layer by layer. This innovation is not only economical but also enables greater customization and rapid prototyping.
The evolution of circuit 3D printing can be traced back to its early roots in additive manufacturing. As researchers and engineers explored different materials and techniques, the idea of combining conventional electronic fabrication methods with 3D printing took flight. Key materials, such as conductive inks and thermoplastics, became pivotal in advancing this technology.
Emerging applications include smart devices, healthcare innovations, and consumer electronics, all of which benefit from the flexibility that circuit 3D printing provides. This article will dissect the methodologies, state-of-the-art materials, and potential challenges faced by this innovative technology, making it a vital read for students, researchers, and professionals alike.
Methodology
Study Design
The study conducted to explore circuit 3D printing involved a comprehensive review of existing literature and practical applications. Researchers focused on understanding the implications of various methodologies utilized in the manufacturing process. This approach allowed for a balanced view of both theoretical perspectives and real-world outcomes.
Data Collection Techniques
Data was gathered from multiple sources, including peer-reviewed journals, industry white papers, and patents. Furthermore, interviews with industry experts contributed firsthand insights. Observational studies of current circuit 3D printing practices provided additional context for the findings derived from the literature review.
Discussion
Interpretation of Results
The results indicated that circuit 3D printing is gaining traction across various sectors. Notably, the technology has significantly reduced the time required to develop prototypes. Additionally, flexibility in design has opened doors for innovative applications that were previously unfeasible with traditional methods.
Limitations of the Study
While the findings are promising, several limitations exist. The variability in material properties can affect the performance of printed circuits. Moreover, the technology is still developing, which means ongoing research is necessary to fully understand its potential and limitations.
Future Research Directions
Future inquiries should focus on the enhancement of materials used in circuit printing, particularly in areas like conductivity and durability. Also, exploring the integration of circuit 3D printing with other technologies, like artificial intelligence and machine learning, may yield robust solutions that push the boundaries of what is currently achievable.
Circuit 3D printing is poised at the intersection of innovation and practicality, making its study not just relevant, but crucial in today's fast-evolving technological landscape. Its potential applications in smart devices, biomedical areas, and consumer electronics signify a transformative era in circuit fabrication.
Intro to Circuit 3D Printing
As we delve into the realm of circuit 3D printing, understanding its significance is crucial. This innovative technology fuses the traditional art of electronics manufacturing with modern additive processes. The implications of this fusion extend far beyond mere convenience; it represents a shift in how electronic components are designed, fabricated, and integrated into various applications.
Definition and Overview
Circuit 3D printing refers to the integration of electronic circuitry directly into three-dimensional printed structures. By utilizing various additive manufacturing techniques, this technology allows for the creation of complex electronic components that are often lightweight and capable of being produced at rapid scale. Different methods like inkjet and extrusion printing are used to lay down conductive materials alongside plastic or other substrates. This collaboration has led to a rethinking of conventional manufacturing paradigms, enabling designers to realize concepts that previously would have only existed in theoretical discussions.
The core advantage of circuit 3D printing lies in its ability to create custom geometries tailored to specific applications, which is vital for evolving fields like smart electronics and wearable devices. Moreover, it streamlines processes by reducing assembly requirements often seen in traditional electronics production.
Historical Context
The journey of circuit 3D printing began in the 1980s with the advent of 3D printing technologies. Initially focused on rapid prototyping, advancements in materials and processes over the decades paved the way for incorporating electronic elements. By the late 1990s, the concept of printing circuits was emerging, but the methods were limited and not widely adopted due to technical challenges.
As electronic needs surged with the growth of consumer technology, more robust and flexible printing methods were developed. Key developments, such as conductive inks and improved extrusion techniques, have made circuit 3D printing more feasible. Today, organizations are exploring how this technology can make workflows more efficient and responsive to market demands.
In summary, the evolution of circuit 3D printing reflects a trajectory of merging electronic and manufacturing expertise. The current landscape indicates an exciting future where electronics can be seamlessly integrated into everyday objects, leading to innovative applications across various sectors.
Technological Foundations
Technological Foundations is a critical topic in the realm of circuit 3D printing. Understanding these foundations is essential for grasping how advancements in printing technology can lead to innovations in electronic circuit fabrication. This section will discuss the primary techniques employed, the significance of the materials used, and how the integration of electronics is shaping the future of this field.
Additive Manufacturing Techniques
Additive manufacturing techniques are at the core of circuit 3D printing. Unlike traditional subtractive processes, these techniques build objects layer by layer. This allows for greater design flexibility and complexity. The most commonly used additive techniques for circuit 3D printing include stereolithography (SLA), selective laser sintering (SLS), and fused deposition modeling (FDM). Each method has unique advantages:
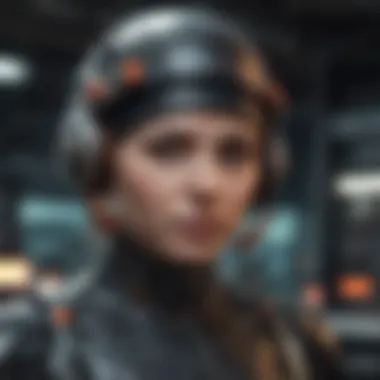
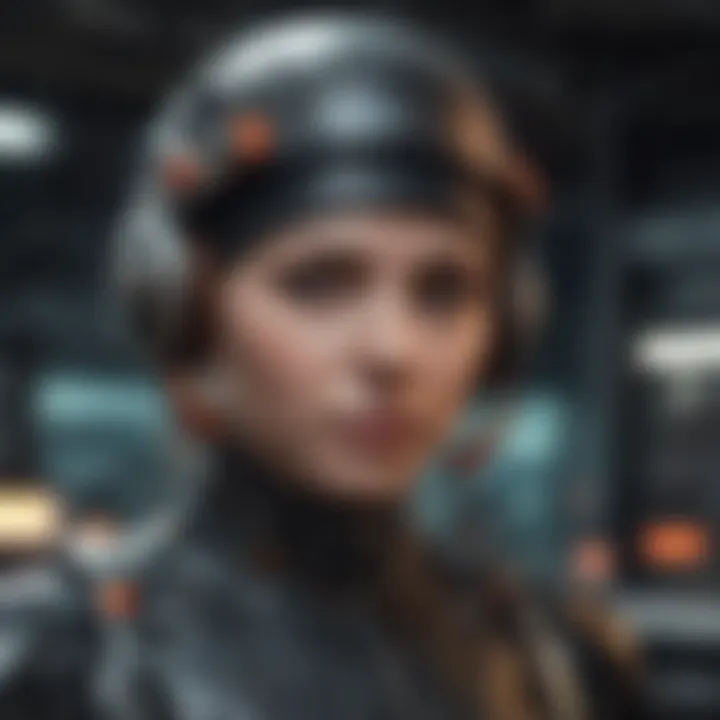
- Stereolithography (SLA): This technique uses a UV light source to polymerize liquid resin. It allows for high-resolution prints but is limited to specific materials.
- Selective Laser Sintering (SLS): In this method, a laser fuses powdered materials together. It can process various materials, including metals and ceramics.
- Fused Deposition Modeling (FDM): FDM works by extruding thermoplastic filaments. This process is user-friendly and has a low cost but may have limitations in producing intricate designs.
These additive techniques contribute to the production of more intricate circuits with potential for miniaturization, which is crucial for applications in consumer electronics and other fields.
Inkjet and Extrusion Technologies
Inkjet and extrusion technologies are two primary methods within the additive manufacturing realm for circuit 3D printing. Inkjet technology involves the deposition of conductive inks to create circuit paths. This method has proven beneficial in terms of precision and flexibility. Inkjet printing allows for various substrates, such as flexible materials, which is essential for applications in wearables.
Extrusion technology, on the other hand, focuses on pushing material through a nozzle to form the desired shape. This is commonly used for thicker materials, like conductive filaments. It provides a robust output, but there may be some limitations in detail resolution when compared to inkjet printing.
Both approaches exemplify the diversity in circuit printing technologies, each offering advantages suited to different applications.
Integration of Electronics in 3D Printing
Integration of electronics into 3D printing represents a significant advancement in the field. Merging traditional electronic components with 3D printing opens up new pathways for innovative designs. For instance, manufacturers can create functional devices in one step, thus minimizing assembly time and reducing overall costs.
Additionally, integrating electronics allows for smart devices that can sense and respond to changes in their environment. This could lead to smarter homes, advanced medical devices, and improved automotive technologies.
However, this integration also raises challenges. The consistency and reliability of printed electronic circuits must meet stringent industry standards. Ongoing research aims to establish best practices for incorporating electronics effectively into 3D printed structures, ensuring both performance and safety.
This combination of electronics and 3D printing demonstrates not just a technological evolution but a paradigm shift in how devices are created and utilized.
Materials Used in Circuit 3D Printing
The significance of materials in circuit 3D printing cannot be overstated. These materials dictate the performance, efficiency, and applicability of printed circuits across various domains. The selection of the right substances directly influences the conductivity, durability, and overall functionality of the final product. With the rapid advancement of technology, innovations in materials employed have opened new avenues for creating sophisticated circuits integrated into more complex devices.
Conductive Inks and Pastes
Conductive inks and pastes serve as the backbone of circuit 3D printing. These materials enable the formation of electrical pathways on non-conductive substrates. Conductive inks usually consist of silver, copper, or carbon particles suspended in a binder. When applied to a surface and cured, these inks form a conductive layer. The choice of material here is paramount, as it impacts not only electrical performance but also the durability of the printed circuit.
Key properties include:
- Conductivity: The ability to conduct electricity effectively is critical. Silver inks typically offer excellent conductivity but at a higher cost compared to copper inks, which are cheaper but may tarnish over time.
- Viscosity: This affects how well the ink can flow through printing nozzles and how it adheres to various substrates.
- Curing Method: Different inks require different curing methods, such as thermal, ultraviolet (UV), or air curing, impacting production time and setup.
Using conductive pastes can also be beneficial. They often provide a thicker layer of conductivity and can be more resilient to environmental factors, particularly in outdoor applications.
Substrates for 3D Printed Circuits
Substrates play a crucial role in circuit 3D printing as they provide the foundation on which conductive inks adhere and electronic components are integrated. Selecting a suitable substrate can directly affect the mechanical properties and reliability of the printed circuit. Commonly used substrates include polyimide films, PET (polyethylene terephthalate), and FR-4 (glass-reinforced epoxy).
Important considerations for substrate choice are:
- Thermal Stability: The substrate must withstand the printing process without deforming. Polyimide, for example, has high thermal tolerance, making it a favorite.
- Adhesion: The ability of conductive materials to stick to the substrate is vital. Poor adhesion can lead to functional failure in circuits.
- Flexibility: For wearables and flexible electronics, substrates need to be lightweight and pliable, allowing for integration into various products without compromising their integrity.
Thermal and Mechanical Properties of Materials
Understanding the thermal and mechanical properties of materials is critical when developing circuit 3D printing technologies. These properties determine how well printed circuits can withstand operating conditions and physical stressors.
Some critical factors include:
- Thermal Conductivity: This indicates how effectively a material can dissipate heat. In applications where circuit density is high, such as in computer processors, effective thermal management is essential to prevent overheating.
- Mechanical Strength: Printed circuits must endure bending, tension, and torsion without failure. Materials with high mechanical strength can better withstand these forces, ensuring a longer lifespan for the device.
- Dielectric Strength: This property defines how much electrical stress a material can tolerate before breakdown. In sensitive electronics, it's essential to use materials with high dielectric strength to protect against voltage spikes.
The evolution of materials used in circuit 3D printing not only enhances product performance but also broadens application possibilities, from consumer electronics to advanced biomedical devices.
Applications and Innovations
The realm of circuit 3D printing emerges as a transformative force within various industries. This technology has evolved far beyond simple prototyping, unlocking myriad applications that fundamentally alter how electronic devices are designed and manufactured. Understanding these applications helps appreciate the significance of circuit 3D printing in the current technological landscape. The innovations arising from this field provide substantial benefits, such as improved design flexibility, reduced material waste, and enhanced integration of electronics into everyday products.
Consumer Electronics
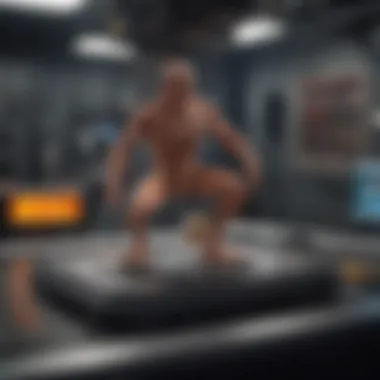
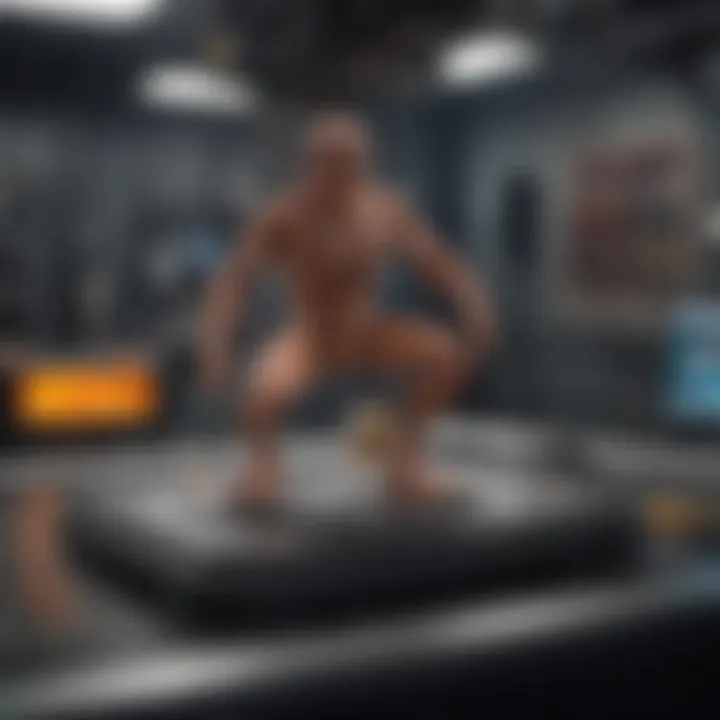
Consumer electronics stand as one of the most prominent fields benefiting from circuit 3D printing. This application encompasses devices like smartphones, tablets, and smart home products. Traditionally, manufacturing these technologies involved multiple processes and significant time, increasing production costs. With the introduction of circuit 3D printing, companies can now create complex circuit designs rapidly and affordably.
For instance, circuit 3D printing allows for the embedding of circuits directly into housing structures, removing the need for separate components. This minimizes potential points of failure and enhances durability. The design possibilities become nearly limitless, enabling personalization and innovation at scale. Additionally, companies can iterate designs quickly, adapting to market changes without extensive new tooling requirements.
Biomedical Devices
In the biomedical realm, circuit 3D printing finds numerous applications crucial to health and wellbeing. From wearable devices that monitor physical conditions to implants designed with integrated sensing technology, the advantages of this innovation are evident. The capacity to print intricate circuitry alongside biocompatible materials enables more efficient and effective personal health monitoring solutions.
Moreover, customized devices can be produced to meet specific patient needs. This tailored approach improves device effectiveness while mitigating the risk of adverse reactions often caused by generic solutions. Future developments promise to push the envelope even further, potentially leading to smart medical implants that can communicate health data in real-time.
Smart Wearables and IoT Devices
The integration of circuit 3D printing in smart wearables and Internet of Things (IoT) devices reflects a significant shift in device capabilities. Wearables, such as smartwatches and fitness trackers, greatly benefit from the ability to integrate sensors and circuits in compact formats. This leads to more efficient power usage, a critical aspect for battery-operated devices.
The manufacturing flexibility allows for designs that are not only functional but also aesthetically pleasing. In an era where personalization plays a significant role in consumer preferences, circuit 3D printing provides a pathway for brands to deliver unique and customized products. IoT devices, infused with smart functionalities, similarly rely on the advancements in circuit 3D printing for seamless integration and improved performance.
Automotive and Aerospace Applications
The automotive and aerospace industries are now leveraging circuit 3D printing to enhance both performance and safety. For automobiles, the ability to integrate sensors directly into components can lead to smarter vehicles that provide real-time data on performance and safety. This innovation could revolutionize maintenance schedules and reduce failures significantly.
In aerospace, weight savings are of utmost importance. By using circuit 3D printing, manufacturers can produce lighter parts without compromising integrity. The ability to create complex geometries also enhances aerodynamic properties. Rationalizing component structures leads to more efficient fuel usage and reduced operational costs for airlines.
"Circuit 3D printing is more than just a trend; it is a paradigm shift that challenges traditional manufacturing norms across industries."
Understanding the applications of circuit 3D printing informs us of its potential impact on our lives. Each sector benefits from enhanced design processes and functionalities that were once impossible. As innovations continue to surface, the boundaries of what can be achieved with circuit 3D printing expand, promising a future rich in possibilities.
Challenges in Circuit 3D Printing
The field of circuit 3D printing presents exciting possibilities but also significant challenges. Understanding these challenges is crucial as it shapes the future of this innovative manufacturing process. Without addressing the issues that arise from material choices, design constraints, and production scalability, the potential applications of circuit 3D printing may not fully realize their promise. This section examines key hurdles and offers insights into their implications for the growth of this technology.
Material Limitations
Materials play a vital role in circuit 3D printing. Conductive materials are essential for the functioning of electronic circuits. However, there are limitations in the range and quality of materials currently available. Conductive inks and pastes can struggle with conductivity levels that traditional methods achieve. The mechanical properties of these materials also vary, affecting durability and reliability in applications.
For instance, while some conductive inks are suitable for printing flexible circuits, they may lack the strength necessary for rigid applications. The adaptability of substrates also poses challenges. Not all materials can withstand heat associated with soldering processes. Therefore, researchers and manufacturers need to innovate and develop new materials to tackle these limitations effectively.
Design Constraints
Design plays a crucial role in circuit 3D printing. The technology allows for complex geometries and layered structures. However, these advantages come with constraints that must be considered during the design phase. The printing process requires specific design features to ensure functionality, which can restrict creative freedom.
Moreover, features like narrow traces or intricate circuitry can be challenging to print accurately. Design software must be compatible with 3D printing technology, ensuring that designs can be executed with precision. These software limitations can hinder efficiency, leading to longer production times and increased costs, making it imperative to seek advancements in both design tools and methodologies.
Scalability and Production Issues
The challenge of scalability in circuit 3D printing is significant. While prototyping is often manageable, transitioning to large-scale production brings different complexities. Reproducibility of printed circuits must scale without compromising quality. This factor is paramount for industries where reliability is non-negotiable, such as automotive or aerospace.
Production speed is also a consideration. When compared to traditional manufacturing methods, current 3D printing technology can be slower. This discrepancy can impact a company's ability to meet market demands effectively. Navigating these issues means then focusing on innovations in printing techniques and machinery to enhance efficiency and optimize production lines.
"The ability to scale 3D printing technology for circuit production can lead to significant innovations across various industries."
Future Directions in Research
The future of circuit 3D printing is filled with promise and potential. Research in this domain is essential as it aims to overcome current limitations and significantly enhance the applications of these technologies. The continual development of advanced materials, improved printing techniques, and sustainable practices will play a crucial role in shaping the next generation of electronic devices.
Advanced Materials Development
The ongoing improvement of materials is vital for the success of circuit 3D printing. Conductive inks, ultra-thin substrates, and thermally stable polymers are of key interest. Researchers are focused on developing materials that not only offer high conductivity but also flexibility. For instance, silver nanowires and carbon nanotubes are gaining attention for their excellent electrical properties. The incorporation of these materials can lead to more efficient circuits in wearable technology and biomedical devices.
The following benefits result from advanced materials development:
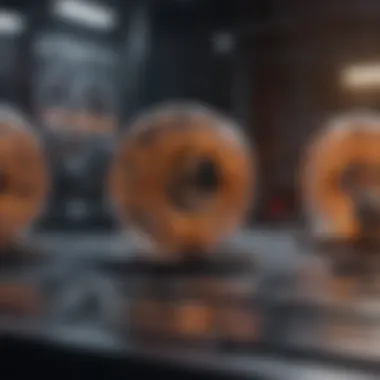
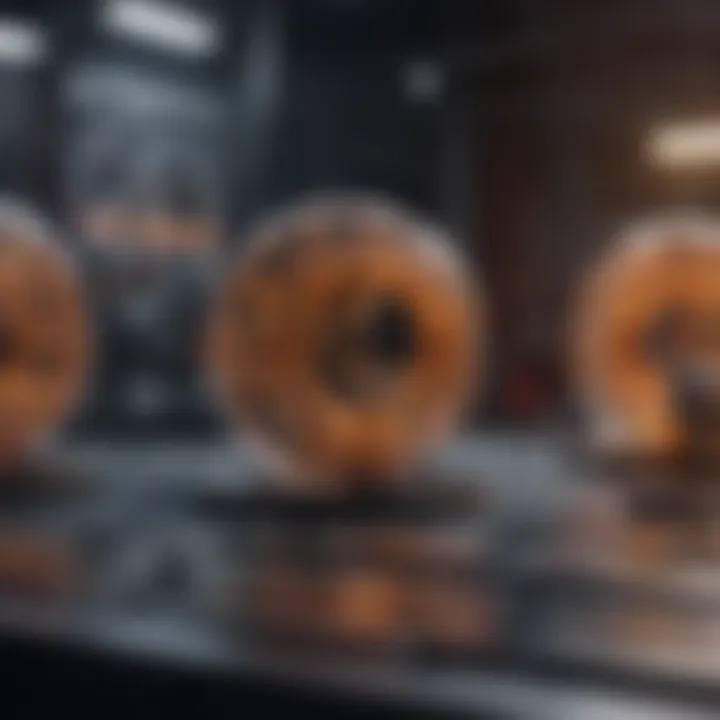
- Enhanced conductivity: Greater efficiency in electronic components.
- Flexibility and durability: Suitable for wearables and complex geometries.
- Cost-effectiveness: Reduction in production costs through innovative material usage.
Improved Printing Techniques
As technology evolves, printing techniques must also advance. Traditional methods sometimes limit the design capabilities of 3D printed circuits. Innovations such as multi-material printing and improved layer adhesion can enhance the resolution and precision of printed electronic devices.
Improved techniques such as inkjet printing and direct ink writing offer significant advantages. They allow for:
- Fine detail and precision: Facilitating more complex designs.
- Scalability: Enabling mass production while maintaining quality.
Moreover, research in biocompatible materials could lead to breakthroughs in medical devices, ensuring safety for human interaction.
Sustainability in Circuit Fabrication
With increasing environmental concerns, sustainability in circuit fabrication is a fundamental aspect of future research. The focus is on lessening waste in the production processes and utilizing renewable materials. Biodegradable inks and recyclable substrates are potential pathways to achieve this goal.
This sustainability focus brings multiple considerations:
- Reduction in hazardous waste: Minimizing environmental impact.
- Energy efficiency: Developing processes that consume less energy.
- Lifecycle analysis: Ensuring products are designed with end-of-life disposal in mind.
"The integration of innovative materials and techniques will undeniably redefine circuit printing, pushing the boundaries of what is possible in electronics."
By embracing these future directions, researchers and industry leaders can work together toward a more efficient and sustainable future in circuit 3D printing.
Regulatory and Safety Considerations
Regulatory and safety considerations in circuit 3D printing are paramount for ensuring the technology's safe and effective integration into various applications. As the field rapidly evolves, it becomes crucial to navigate the landscape of standards and regulations that govern the use of materials and processes. This scrutiny is not only necessary for compliance but also for fostering consumer confidence in products resulting from circuit 3D printing.
Industry Standards
Industry standards represent a framework that helps organizations ensure quality and safety in their circuits produced via 3D printing. Bodies like the International Organization for Standardization (ISO) and the Institute of Electrical and Electronics Engineers (IEEE) set forth guidelines that facilitate interoperability, safety, and reliability in electronic components. For instance, materials used in 3D printing must pass certification tests to ensure they meet electrical and mechanical performance criteria. Such regulations align with the need for products to withstand operational stress and ensure reliable function over time.
Key aspects of industry standards include:
- Material Safety: Guidelines ensure materials are appropriately tested for toxicity and performance.
- Process Quality: Standards dictate preparation and handling processes that reduce error rates in production.
- Testing Protocols: Regular testing of prototypes for compliance helps catch design flaws early.
These standards enable manufacturers to create safer products that consumers can trust, ultimately driving further adoption of circuit 3D printing technology.
Health and Environmental Impacts
Health and environmental impacts arise due to the materials and processes involved in circuit 3D printing. The use of conductive inks, plastics, and metal powders can have health implications during production. Proper ventilation and personal protective equipment (PPE) are necessary to mitigate exposure to potentially harmful substances. Moreover, understanding the life-cycle of materials used in circuit printing is essential to reduce ecological footprints.
Some important considerations include:
- Toxicity of Materials: Evaluating the chemical composition of inks and other materials helps in managing health risks.
- Waste Management: Effective strategies are needed to handle waste generated in the printing process, especially hazardous materials.
- Sustainability Practices: Emphasizing eco-friendly materials and processes can help minimize the environmental degradation associated with manufacturing and disposing of printed circuits.
The integration of regulatory frameworks and safety measures in circuit 3D printing not only safeguards human health but also promotes sustainable practices, making it critical for future advancements in the field.
In summary, addressing regulatory and safety issues in circuit 3D printing is crucial for the responsible development of this technology. It ensures that products are safe, reliable, and environmentally sound, paving the way for wider adoption in various industries.
Culmination
The exploration of circuit 3D printing highlights a significant evolution in both manufacturing and electronics. This conclusion serves to synthesize the findings of the article and emphasizes the transformative implications of this emerging field.
Summary of Key Points
Circuit 3D printing is not just a novelty; it embodies a paradigm shift. The key points discussed include:
- Technological Foundations: The foundations of additive manufacturing and how inkjet and extrusion technologies integrate electronic components.
- Materials: A deep dive into the conductive inks and substrates, emphasizing their thermal and mechanical properties.
- Applications: The diverse applications across consumer electronics, biomedical devices, and automotive settings, showcasing how this technology is being utilized today.
- Challenges: An honest look at material limitations, design constraints, and the scalability of production practices that currently hinder broader adoption.
- Future Directions: Advanced material development and improved techniques, where sustainability becomes a critical focus.
- Regulatory Aspects: The necessity of industry standards and health considerations that will shape future developments.
The accumulated knowledge shapes our understanding of how circuit 3D printing can impact various industries.
Implications for Future Technologies
Circuit 3D printing is poised to revolutionize not only how electronic circuits are manufactured but also how efficiently they integrate into a variety of applications. The implications for future technologies are profound.
- Integration of AI: As AI advances, circuit 3D printing could enable smarter design possibilities, allowing for the optimization of circuit layouts for performance and efficiency.
- Cost-Effectiveness: There is potential for drastically reduced costs in electronic manufacturing, enabling smaller companies to compete in the market.
- Customization: The ability to create tailored circuits for specific needs, whether in biomedical applications or in consumer electronics, could increase product efficiency.
- Environmental Considerations: With sustainability becoming a focal point in technology development, circuit 3D printing offers an avenue for reducing waste and utilizing eco-friendly materials.