In-Depth Study on Vanadium Titanium Alloy Properties
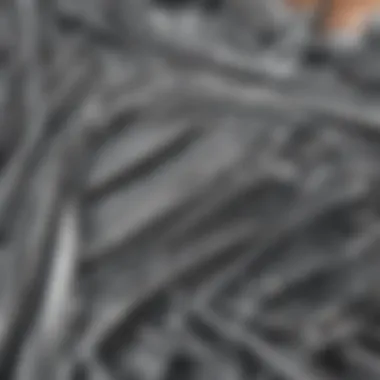
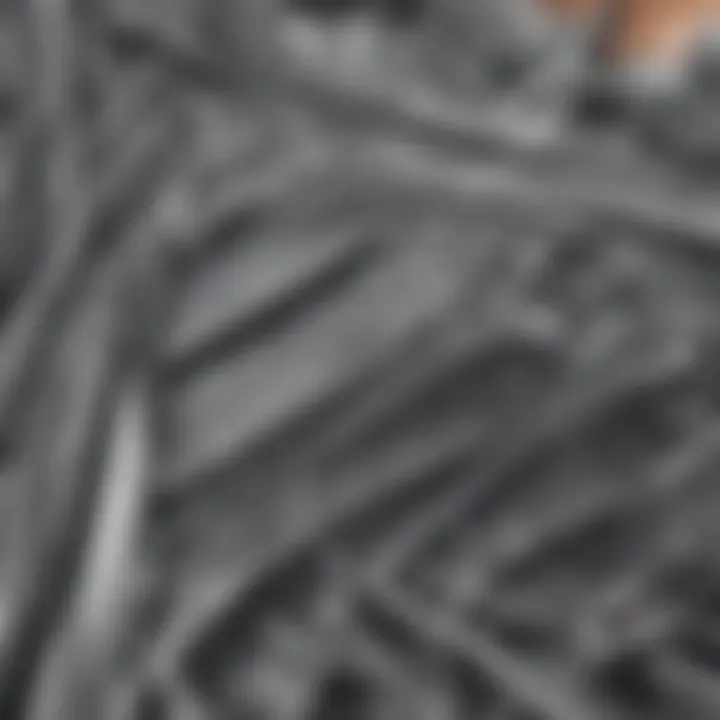
Intro
In the landscape of advanced materials, vanadium titanium alloy stands out as a subject of intense scrutiny due to its remarkable properties and an array of industrial applications. This unique alloy, composed primarily of vanadium and titanium, has drawn the attention of scholars and industry experts alike, thanks to its exceptional strength-to-weight ratio and corrosion resistance. With such qualities, this alloy is making waves in sectors that demand materials capable of withstanding extreme conditions, particularly in aerospace, automotive, and biomedical fields.
The exploration of vanadium titanium alloy not only highlights its elemental characteristics but also scrutinizes the intricacies involved in its processing. From the methods of alloying to the resultant mechanical properties, every detail plays a pivotal role in maximizing the utility of this material. It’s essential to pave the way for innovations that can push the boundaries of its existing applications and explore avenues yet to be mined.
As we delve deeper into this analysis, we aim to bridge the gap between theoretical knowledge and real-world applications, catering to students, researchers, educators, and professionals eager for a nuanced understanding of material science. Through a careful examination of the alloy’s properties, industrial relevance, and future directions, readers will gain substantial insight into the ongoing research and applications of vanadium titanium alloy.
Intro to Vanadium Titanium Alloy
The examination of vanadium titanium alloy serves as a cornerstone in understanding the advances in materials science and engineering. In this article, we delve into this unique alloy to uncover its distinctive properties, key applications, and ongoing innovations in its production and use. The relevance of vanadium titanium alloy extends beyond mere academic interest, as it plays a crucial role in diverse industries like aerospace, automotive, and bioengineering. By understanding its fundamental characteristics, one can appreciate why professionals in these fields prioritize research on this alloy.
Understanding Alloys
Alloys are composite materials formed by combining two or more elements, where at least one is a metal. This amalgamation creates a new material with properties that differ significantly from those of its constituents, enhancing strength, ductility, and corrosion resistance.
Vanadium titanium alloys specifically benefit from the unique characteristics of both titanium and vanadium. Titanium brings lightweight strength and excellent corrosion resistance, while vanadium enhances the toughness and wear resistance of the alloy. When these elements are blended, they form a material that can handle extreme conditions, making it invaluable in applications ranging from high-performance vehicles to medical devices.
From a technical perspective, the phase composition of an alloy can determine its final properties. This makes understanding the metallurgy and the interactions of various elements critical for engineers and designers. For instance, varying the proportions of vanadium and titanium can yield different mechanical properties, allowing for customization based on specific application requirements.
Historical Context of Vanadium and Titanium
The journey of vanadium and titanium through history is as fascinating as their properties are useful. Vanadium was first discovered in the early 19th century by the Spanish chemist Andrés Manuel del Río, although it didn’t gain significant attention until the early 1900s, when it was recognized for its ability to strengthen steel. On the other hand, titanium was isolated in 1791 by the clergyman and chemist William Gregor, but it wasn't until the mid-20th century that its potential as a structural material was truly realized.
Both elements saw their use thrive during and after World War II, where high-performance materials were in dire need. Titanium became essential for aircraft components, while vanadium’s properties fortified steels and other alloys.
In modern times, the integration of vanadium and titanium into a singular alloy has led to groundbreaking developments in various sectors. The ongoing research focuses not just on their mechanical and chemical advancements, but also on their environmental impacts and sustainability practices in production.
This historical context underscores the importance of exploring the properties and applications of vanadium titanium alloy today. Understanding their past helps inform present and future advancements, illustrating how these elements contribute significantly to modern material science.
Chemical Properties of Vanadium Titanium Alloy
Understanding the chemical properties of vanadium titanium alloy is key to appreciating its multifunctionality and adaptability in various domains. This section dives into the heart of what makes this alloy not just an interesting subject for chemists but also a significant component in modern engineering. The blend of reactivity, stability, and phase characteristics provides insights into its performance across industrial applications, from aerospace to bioengineering.
Reactivity and Stability
Vanadium titanium alloy demonstrates a unique balance of reactivity and stability, which is critical in determining its performance in demanding environments. Reactivity refers to the tendency of the alloy to undergo chemical changes when exposed to various conditions. In contrast, stability ensures that the alloy maintains its properties over time.
In practical applications, this means that the alloy can withstand harsh oxidizing environments often found in aerospace or energy sectors. For example, vanadium's ability to form oxides at high temperatures does present challenges. However, when combined with titanium, these oxides can offer protective layers which prevent further degradation. In essence, the combination offers an effective shield against environmental factors.
It's important to note that reactivity varies depending on both temperature and exposure to other elements. This leads to intriguing possibilities, such as intentional oxidation which can enhance surface properties for specific applications. The result? Enhanced adhesion of coatings and improved resistance against wear, making the alloy suited for components subjected to friction.
Regardless of the advantages, considerations must be made regarding the alloy's specific application. Prolonged exposure in certain environments can lead to a reactive nature that may not be desirable for specific uses. This makes proper characterization essential for engineers and developers when designing components.
Phase Diagram Analysis
The importance of phase diagram analysis cannot be overstated as it lays the groundwork for understanding how vanadium titanium alloy behaves under varying temperatures and compositions. A phase diagram serves as a map, depicting the phases of an alloy and their stability ranges under different conditions.
In a typical vanadium titanium phase diagram, the interactions between vanadium and titanium can be analyzed. The diagram allows us to visualize liquid and solid phases and how they change as temperature and titanium content fluctuate.
The alpha phase, a solid solution of titanium, with its hexagonal close-packed structure, and the beta phase, having a body-centered cubic structure, are the two key phases to watch out for. The transformation from alpha to beta phase—and vice versa—can significantly influence the mechanical properties of the alloy, such as hardness and ductility. Furthermore, the composition of each phase is crucial when considering potential applications. For instance, an increase in vanadium content will typically shift the phase boundaries, altering the material’s behavior.
Understanding these phase relationships is particularly useful for manufacturing processes. Engineers design processes by leveraging these phase changes to optimize mechanical properties for specific applications, whether in light-weight structural components or highly resilient parts for engines.
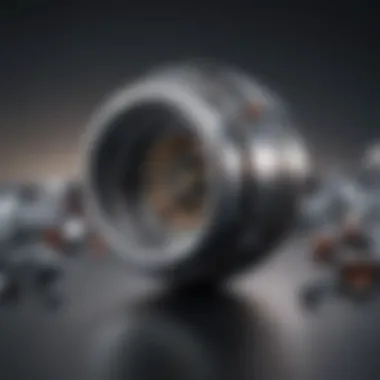
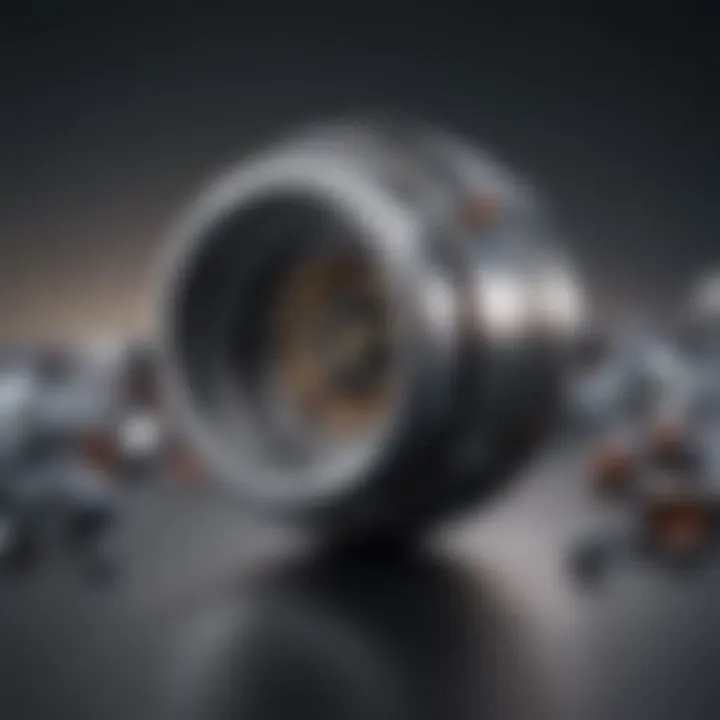
"The phase diagram of an alloy is like a cheat sheet for understanding how the mixture of elements will perform under different conditions. A little tweak can lead to entirely new properties, and thus applications."
Overall, a thorough grasp of both reactivity and phase diagram characteristics is invaluable. It shapes the way researchers and practitioners approach developments in the use of vanadium titanium alloys and influences future innovation. The intricacies of these chemical properties form a crucial backbone upon which the alloy’s applications are built.
Mechanical Properties
Understanding the mechanical properties of vanadium titanium alloy is crucial for various industries that rely on materials with specific strength, durability, and adaptability under different conditions. Mechanical properties encompass how a material reacts to external forces, which is vital to ensure safety and efficiency in applications ranging from aerospace to biomedical devices. Manufacturers must consider these properties to optimize their structures for performance, longevity, and reliability.
Strength and Ductility
Strength is one of the primary attributes of vanadium titanium alloy, significantly influencing its utility in demanding applications. This alloy boasts remarkable tensile strength, which makes it suitable for high-stress environments. For instance, in aerospace components, the lightweight yet robust nature of the alloy helps in reducing overall fuel consumption and enhancing energy efficiency.
On the other hand, ductility allows the material to deform under stress without breaking, which is another appealing quality. The combination of high strength and good ductility means that components made from vanadium titanium alloy can withstand significant loads while still being capable of undergoing some form of deformation. This is critical in processes like shaping and forming components during manufacturing.
"The balance between strength and ductility determines how well a material will perform in real-world applications."
Fatigue Resistance
Fatigue resistance refers to a material’s ability to withstand cyclic loading, which is important in applications where components experience repeated stress over time. Vanadium titanium alloy demonstrates impressive fatigue properties, making it suitable for parts used in aircraft or machinery that undergo continuous operation. The material's microstructure often enables it to absorb energy without forming cracks, which is critical for longevity.
In aerospace engineering, for instance, fatigue can lead to catastrophic failures. Ensuring that components made of this alloy can handle cyclic stresses allows designers and engineers to create safer, more reliable aircraft. It provides the assurance that parts will maintain their integrity even after prolonged usage.
Thermal Properties
Thermal properties of a material include how it conducts heat and reacts to changes in temperature. Vanadium titanium alloy displays significant thermal stability, which is beneficial in environments where temperature fluctuations are common. This property is especially relevant in aerospace applications, where components are exposed to high temperatures during flight.
Additionally, the alloy’s thermal expansion characteristics can aid in maintaining dimensional stability under varying thermal conditions. Ensuring that components do not expand or contract excessively is vital in preventing mechanical failures or misalignments.
Manufacturing Processes
The manufacturing processes of vanadium titanium alloy are essential for ensuring the material’s integrity and optimally harnessing its unique properties. With applications spanning industries from aerospace to biomedical, understanding these processes can greatly impact service performance and longevity. The complexity of alloy production influences various characteristics, such as mechanical strength and corrosion resistance. It is this interplay between method and material that underscores the importance of manufacturing processes in this article.
Alloy Production Techniques
Production of vanadium titanium alloy involves a series of carefully managed techniques that come together to form a composite material that maintains the advantageous properties of its elemental components. Several methods are commonly used, each offering its own benefits and applications.
- Powder Metallurgy: This process begins by mixing the titanium and vanadium powders. These powders are compacted under high pressure and then sintered in a furnace. The result is a dense, homogeneous alloy that can exhibit superior mechanical properties. This technique is particularly valued for its ability to precisely control the alloy composition and minimize impurities.
- Vacuum Arc Melting: In this approach, titanium and vanadium are melted in a vacuum to prevent oxidation. The molten metal is then allowed to solidify into a single ingot, which can be further processed or used for complex components. This method excels in producing high-purity alloys, which is crucial for applications demanding exceptional reliability, such as aerospace and medical devices.
- Electron Beam Melting: Similar to vacuum arc melting, this technique involves melting the metal using a focused electron beam under vacuum. It offers advantageous characteristics such as rapid solidification and fine control over the alloy’s microstructure. This level of control can significantly enhance the final product's mechanical properties.
The selection of production technique ultimately depends on the desired properties and application of the final alloy. Keeping a close eye on these techniques is crucial, as small variations can lead to significant differences in performance and durability.
Forming and Machining Methods
Once the alloy is produced, forming and machining processes come into play to attain specific shapes and dimensions suitable for various applications. These methods ensure that the material can be integrated into broader systems effectively.
- Forging: This process involves shaping the alloy using compressive forces. It’s often done while the material is heated, enhancing its ductility. Forging not only shapes the alloy but also improves its mechanical properties through grain refinement, making it an excellent choice for components subjected to heavy loads.
- Casting: With this method, molten alloy fills a pre-shaped mold and solidifies into the desired form. Casting is versatile and can be used for complex shapes that would be difficult to achieve through other processes. However, achieving a high-quality cast requires careful control of cooling rates and mold design to avoid defects, such as porosity.
- Machining: This encompasses subtractive processes to shape the material post-production. Techniques such as milling, turning, and grinding are commonly employed. Machining allows for high precision in creating intricate components. Moreover, using advanced machining strategies, it’s possible to achieve smooth finishes, critical for applications in sensitive fields like medical devices.
Combination of these forming and machining processes allows manufacturers to tailor vanadium titanium alloy products to meet specific performance needs efficiently. Each step, from production to final shaping, must be undertaken with precision to maximize the alloy’s inherent advantages.
Applications of Vanadium Titanium Alloy
The diverse applications of vanadium titanium alloy underscore its pivotal role across several high-tech industries. Understanding where this alloy finds its bread and butter offers valuable insights into its importance, enhancing our grasp over its contributions. Vanadium titanium alloys, noted for their excellent mechanical strength, corrosion resistance, and lightweight characteristics, are increasingly seen as vital materials in sectors ranging from aerospace to biomedical fields. Each of these realms leverages the alloy's unique properties to solve specific challenges, making it a subject of considerable interest.
Aerospace Industry
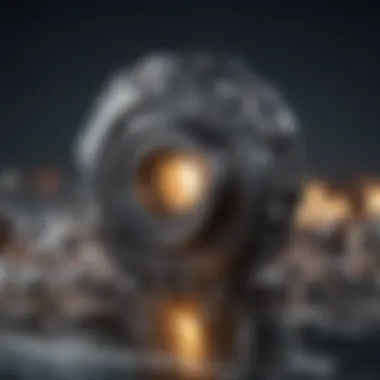
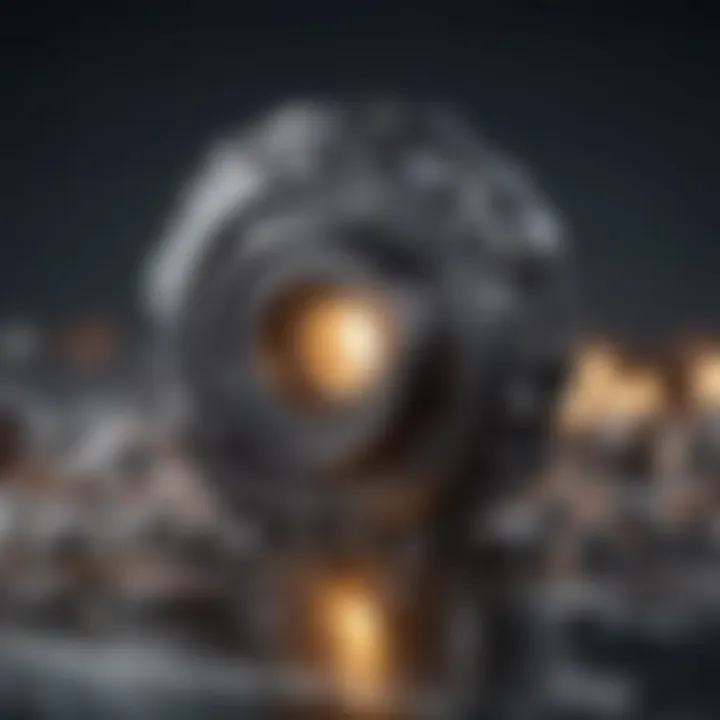
In the realm of aerospace, vanadium titanium alloys are treated much like a golden ticket. Their high strength-to-weight ratio is essential for aircraft, spacecraft, and various components that must withstand harsh conditions without adding excessive weight. The aerospace industry continually pushes the boundaries of performance, and these alloys perfectly fit the bill due to their combination of durability and lightness.
Some noteworthy applications include:
- Airframe Components: The fuselage, wing structures, and other critical parts benefit from the alloy’s robustness while keeping aircraft weight low, which in turn boosts fuel efficiency.
- Engine Components: Turbine blades and other engine parts demand materials that can endure extreme temperatures. Here, vanadium titanium alloys excel because of their thermal stability, ensuring reliability and safety during flight.
Moreover, as new aviation technologies emerge, particularly those focused on sustainable practices, the demand for vanadium titanium alloys is likely to surge further. In short, without this alloy, modern aerospace engineering would be firmly grounded.
Automotive Sector
The automotive industry is another major player bringing vanadium titanium alloys to the forefront. With an increasing focus on efficiency and sustainability, automakers are keen on incorporating advanced materials to reduce vehicle weight while ensuring safety and performance. Vanadium titanium alloys are making waves here as well, contributing to fuel economy and emissions reductions.
Key applications in this sector include:
- Vehicle Chassis and Frames: Utilizing these alloys helps car manufacturers create lighter structures, leading to energy-efficient vehicles that do not sacrifice strength or safety.
- High-Performance Parts: For performance vehicles, components like suspension and exhaust systems often require materials that can withstand dynamic stresses. The alloy’s resilience ensures long-lasting performance.
In recent years, with the rise of electric vehicles, vanadium titanium alloys have gained attention, signaling potential for future innovation in battery technology. Their role here might be a game-changer, optimizing energy storage systems.
Biomedical Applications
A critical area where vanadium titanium alloys shine is in biomedical applications. In medical devices and surgical implants, the demand for materials that offer high biocompatibility, corrosion resistance, and strength makes vanadium titanium alloys particularly valuable. They are employed in situations where performance is not just a goal, but a necessity for human health.
Applications include:
- Implants: The use of the alloy in orthopedic implants, such as joint replacements and dental implants, illustrates its capability to integrate well within the human body. The materials can endure bodily stresses while resisting corrosion from bodily fluids.
- Surgical Instruments: Instruments fashioned from vanadium titanium provide precision and durability, contributing significantly to surgical advancements.
The biocompatibility of these alloys plays a huge role in their acceptance in the healthcare sector, making patient safety a top priority.
Energy Sector Roles
The energy sector also taps into the advantages offered by vanadium titanium alloys. With ongoing pursuits in renewable energy and power generation, these materials serve multiple roles that facilitate innovation and efficiency. Widespread applications in energy capture and storage are changing the landscape of energy solutions.
Consider the following roles:
- Wind Turbines: Components made from vanadium titanium alloys can endure the mechanical stresses and environmental challenges faced by wind turbines, ensuring longevity and efficiency.
- Energy Storage Systems: There's potential for these alloys in improving the performance of energy storage solutions like batteries, especially with the push for enhanced technology.
In summary, the versatility of vanadium titanium alloys allows them to make significant contributions to the aerospace, automotive, biomedical, and energy sectors. This adaptability is fueling ongoing research and innovation, highlighting their pertinence in contemporary materials science.
Corrosion Resistance and Environmental Impact
Understanding corrosion resistance is paramount when discussing vanadium titanium alloys. These alloys, known for their impressive strength and lightweight properties, also demonstrate notable resistance to corrosion, which plays a pivotal role in their functionality across diverse environments. With the increasing focus on sustainability and environmental protection, examining the corrosion mechanisms and conducting life cycle analyses has become essential in evaluating the impact of these alloys on our planet.
Corrosion Mechanisms
Corrosion affects metals through various mechanisms, and vanadium titanium alloy is no exception. A few key mechanisms include:
- Uniform Corrosion: Often caused by exposure to atmospheric conditions or saline environments. This type leads to a general thinning of the alloy surfaces, which can compromise structural integrity over time.
- Localized Corrosion: This includes crevice corrosion and pitting, typically more severe. These occurrences are often due to stagnant conditions or impurities in the alloy itself. For example, crevices in joints or connections may trap moisture, leading to highly localized degradation.
- Galvanic Corrosion: Arises when two dissimilar metals are in contact, leading to accelerated corrosion of one metal. Within complex structures, understanding the alloy's role in preventing such occurrences is crucial.
The alloy's composition significantly influences its resistance to these various forms of corrosion. For instance, the addition of other elements can enhance protection against galvanic corrosion. Moreover, the relatively stable oxidation layer that forms on titanium helps shield the underlying metal, contributing to overall durability.
Life Cycle Analysis
Conducting a life cycle analysis (LCA) for vanadium titanium alloys provides a comprehensive assessment of their environmental impact, from raw material extraction to end-of-life disposal. An LCA typically involves several stages:
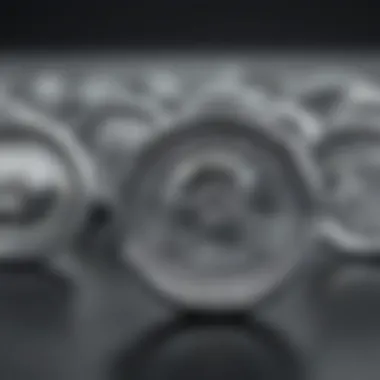
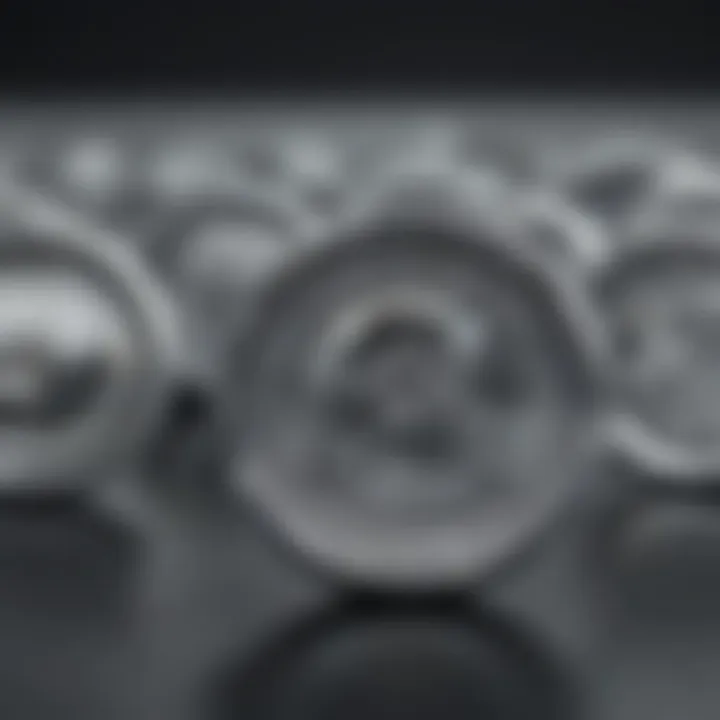
- Raw Material Extraction: The mining and processing of vanadium and titanium have significant ecological footprints. Responsible sourcing practices can mitigate adverse effects, emphasizing the importance of sustainable mining operations.
- Manufacturing: This involves evaluating energy consumption, emissions, and waste generation during production. Innovations in processing techniques can optimize efficiency, reducing the overall carbon footprint.
- Product Use: Vanadium titanium alloys exhibit exceptional durability and corrosion resistance, leading to longer service life in applications. Consequently, the reduced frequency for replacement mitigates environmental strains.
- End-of-Life Management: Finally, how these materials are disposed of or recycled affects their overall environmental impact. Recycling vanadium and titanium can drastically lower environmental impacts while also conserving resources.
Conducting an LCA leads to more informed decisions and highlights opportunities for enhancing sustainability in the usage of vanadium titanium alloys.
"The environmental footprint of materials is profoundly important, demanding our attention in age of renewable resources and sustainability considerations."
Research and Development Trends
The exploration of vanadium titanium alloy is deeply entwined with ongoing research and development trends that have transformative implications across various sectors. With an ever-increasing thrust towards innovation, understanding these trends is crucial for unlocking the alloy's full potential. It provides insights that benefit not just manufacturers but also researchers, educators, and industry practitioners. Through this section, we will delve into the specific advancements in alloy composition and processing techniques that are shaping the future of vanadium titanium alloys.
Advancements in Alloy Composition
The quest for enhanced performance in vanadium titanium alloys has spurred significant advancements in their composition. Researchers are closely studying the effects of varying the ratios of vanadium and titanium, often looking to tailor properties suited to specific applications. For instance, increasing the vanadium content can enhance certain mechanical properties such as strength and hardness, yet too much can make the alloy brittle. Getting it right is like walking a tightrope; the balance is essential.
- Here are some notable influences on alloy composition changes:
- Microalloying Elements: Incorporating elements like aluminum or niobium can improve wear resistance and ductility.
- Phase Manipulation: Adjusting the alloying elements allows for control of phase transformations, optimizing mechanical properties.
- Thermodynamic Improvements: Considerations of thermodynamics can lead to compositions that are not just stronger but also more stable at high temperatures.
Employing advanced materials characterization techniques, researchers are identifying precisely how these compositions behave under various conditions. They are utilizing tools such as scanning electron microscopy (SEM) and X-ray diffraction (XRD) to study microstructures, which can reveal hidden potentials in the alloy.
Innovations in Processing Techniques
While composition is vital, how an alloy is processed often determines its ultimate performance. Innovations in processing techniques are gaining traction in the field of vanadium titanium alloys. These methods are pushing the envelope on what can be achieved, leading to products that are stronger, lighter, and more durable.
Some notable innovations include:
- Additive Manufacturing: Techniques such as 3D printing are becoming increasingly popular. By using powder metallurgy, manufacturers can create intricate shapes and structures that were previously unattainable with traditional methods.
- Advanced Heat Treatment: Tailored heat treatment processes can significantly enhance mechanical properties, allowing for a better balance of toughness and strength.
- Friction Stir Processing: A relatively new technique that improves surface properties and microstructure. This method allows the creation of materials with a fine grain structure, enhancing wear and fatigue resistance.
"The evolving landscape of processing techniques represents not just a shift in manufacturing, but a revolution that aligns with today's demands for efficiency and precision."
In summary, the dynamic nature of Research and Development trends in vanadium titanium alloys is truly a game changer. By focusing on advancements in alloy composition and innovations in processing techniques, we see a future filled with possibilities that extend beyond traditional applications. This depth of research not only fosters growth within the industries directly using these alloys but also propels further inquiry among academics, ensuring that the alloy stays relevant in a rapidly changing technological landscape.
Future Outlook
The future outlook for vanadium titanium alloys is a tapestry interwoven with market dynamics, innovative advancements, and increasing awareness of environmental impacts. As industries shift towards more sustainable materials while demanding high-performance characteristics, the relevance of vanadium titanium alloys becomes ever more pronounced. This alloy holds significant promise in ensuring robustness, resistance to wear, and lightness, making it crucial for key sectors like aerospace and automotive.
Market Demand Projections
As we gaze into the crystal ball, the market for vanadium titanium alloys appears to be on a growth trajectory. With the rise of clean energy technologies and advancements in aerospace engineering, the appetite for these alloys is likely to expand.
There are several factors driving this increase:
- Aerospace Innovation: The aerospace industry continues to seek lightweight materials that promise higher fuel efficiency and reduced emissions. Vanadium titanium alloys’ strength-to-weight ratio positions them as ideal candidates.
- Automobile Manufacturing: Automotive manufacturers are progressively focused on reducing vehicle weight to enhance fuel economy. This emphasizes the need for versatile and durable materials like vanadium titanium alloys.
- Biomedical Applications: The demand for medical devices and implants that meet stricter standards for biocompatibility and strength is on the rise. Vanadium titanium alloys are meeting this need effectively.
Companies are expected to invest heavily in research to push the boundaries of alloy compositions and processing techniques, positioning themselves to capture a greater share of this flourishing market.
Potential Challenges and Solutions
Despite the favorable outlook, the path forward for vanadium titanium alloys is not without its bumps. Several challenges threaten to impede the smooth sailing of growth in this sector:
- Cost of Raw Materials: The extraction and processing of vanadium and titanium can be costly, affecting the overall pricing of the alloy. This needs addressing through more cost-effective production methods.
- Supply Chain Vulnerabilities: Erratic market fluctuations in sourcing these metals can create instability. Companies can consider diversifying their supplier base or investing in alternative materials as a hedge against supply disruptions.
- Technological Barriers: While advancements are happening, there’s still a learning curve for industries integrating these alloys. Continued education and targeted R&D investments are vital to overcome these technological challenges.
To sail through these waters, companies can adopt various strategies:
- Investing in New Technologies: Adapting more efficient production processes can lower costs while improving quality.
- Collaboration Across Industries: Sharing knowledge and resources between sectors can drive innovation and efficiency, supporting the advancement of vanadium titanium alloys in diverse applications.
The relationship between innovation and market stability is crucial for the future success of vanadium titanium alloys, paving a potential path toward leadership in material science.
As we look ahead, the future of vanadium titanium alloys is not merely promising; it’s ripe with potential, signaling a significant shift in how modern industries may approach material selection and application.