Steel Corrosion Protection: Strategies and Innovations
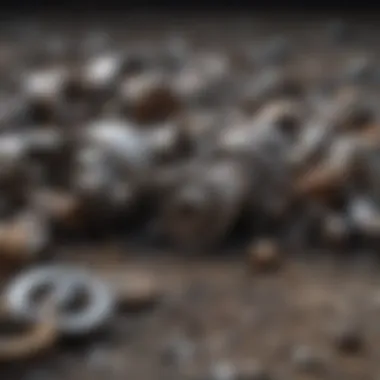
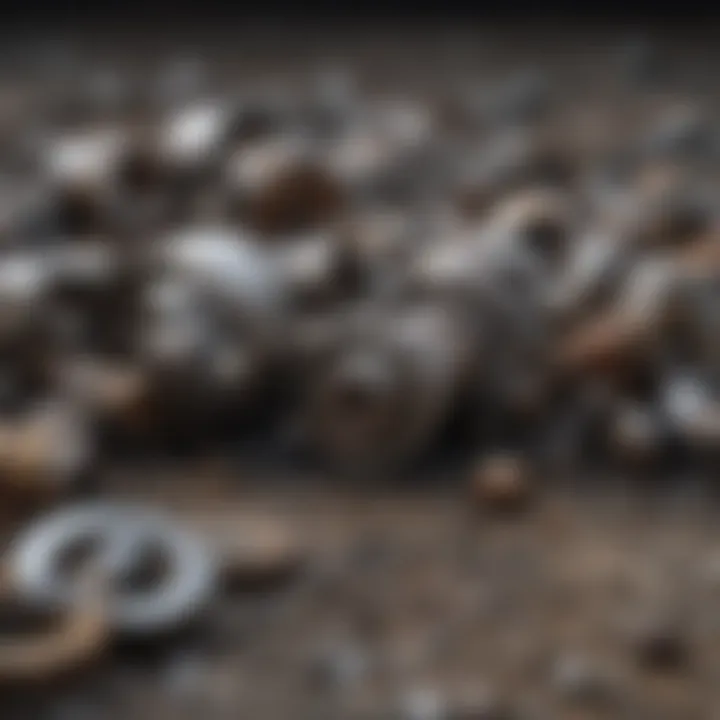
Intro
Corrosion of steel represents a significant challenge across various industries, affecting everything from infrastructure to manufacturing. The process of corrosion can lead to material failure, safety risks, and substantial economic losses. Therefore, understanding strategies for protecting steel from corrosion is crucial for engineers, researchers, and manufacturers.
This article delves into the dynamic realm of steel corrosion protection techniques. It provides a detailed overview of corrosion types, causative factors, and protective methods. By doing so, it aims to provide the foundation for ongoing discussion about best practices and recent technological innovations in combating corrosion. The insights presented here will aid in navigating the complex landscape of steel protection strategies.
Methodology
Study Design
The analysis of corrosion protection strategies involves two key components: evaluating existing methods and highlighting innovations. This study employs a comparative framework to assess various protection techniques such as coatings, galvanization, and cathodic protection. Each method is scrutinized concerning its effectiveness, application scenarios, and limitations.
Data Collection Techniques
To gather relevant data, this article incorporates a mix of literature review and case study analysis. Key resources include academic publications, industry reports, and standards from organizations like the American Society for Testing and Materials (ASTM). Additionally, insights from recent conferences and professional networking forums provide real-world context to theoretical findings, emphasizing the relevance of effective steel corrosion protection.
Discussion
Interpretation of Results
The findings underscore that no single corrosion protection method is universally applicable. For example, coatings such as paint or epoxy offer significant advantages in controlled environments but may fail under severe conditions. On the other hand, galvanization, though effective, presents its own set of challenges, especially in terms of coating thickness and adhesion.
Emerging techniques like smart coatings with sensors for real-time monitoring provide promising avenues for enhancing protective measures. These advancements reveal a shift towards more proactive rather than reactive strategies in managing corrosion.
Limitations of the Study
While the article aims to offer a comprehensive overview, it is important to acknowledge certain limitations. The focus is primarily on commonly used methodologies, potentially overlooking niche techniques that could be beneficial in specific applications. Additionally, the rapid pace of innovation in this sector means that some newly developed strategies may not yet be widely documented or studied.
Future Research Directions
Future exploration into corrosion protection should aim to integrate multidisciplinary approaches. By combining materials science with digital technologies, researchers can develop more effective solutions. There is also a need for longitudinal studies that measure the long-term effectiveness of corrosion protection strategies in various environments.
As the demand for durable materials continues, ongoing research in protective technologies will be vital in fostering advancements and enhancing the lifespan of steel structures.
Understanding Steel Corrosion
Steel corrosion is a critical topic that significantly impacts infrastructure, machinery, and overall material performance. Understanding this phenomenon is vital for engineers, researchers, and stakeholders in various industries. Corrosion leads to deterioration, which can cause safety hazards and economic losses. By comprehending the nature and types of corrosion, one can design effective mitigation strategies and improve the service life of steel structures.
The concept of steel corrosion encompasses several factors. Mechanistically, it is an electrochemical process influenced by environmental factors. Temperature, humidity, and presence of certain chemicals can accelerate corrosion. Identifying these factors allows for the development of robust protection methods, enhancing durability and reliability. Consequently, a thorough understanding of corrosion supports better decision-making in material selection and maintenance practices.
Furthermore, studying corrosion unlocks innovations in protective technologies. The industry continuously seeks advanced materials and methods to combat corrosion. This pursuit not only conserves resources but also ensures safety and extends the lifespan of critical infrastructure. Thus, understanding steel corrosion is not just an academic exercise but a practical necessity in today's world.
Nature of Corrosion
Corrosion is a natural process that occurs when metals interact with their environment, leading to the degradation of the material. This interaction involves both chemical and physical phenomena. Typically, it manifests as rust, which significantly weakens the integrity of steel structures.
Types of Corrosion
- Uniform Corrosion
Uniform corrosion is characterized by an even loss of material across a surface. This type is usually predictable and easily manageable. The main benefit of uniform corrosion is that it allows for systematic inspections and maintenance. Engineers can estimate how long a steel component will last under specific conditions. - Pitting Corrosion
Pitting corrosion presents localised areas of corrosion that resemble small pits. This type can be especially dangerous as it often leads to sudden failure. Its unpredictability is a key characteristic. Notably, pitting corrosion can be challenging to detect early. - Galvanic Corrosion
Galvanic corrosion occurs when two dissimilar metals are in contact in the presence of an electrolyte. This process accelerates the corrosion of one of the metals. A significant feature is that it can be anticipated and mitigated through material selection and design. However, attention must be paid to cathodic protection methods for effective management. - Crevice Corrosion
Crevice corrosion happens in confined spaces where stagnant liquid creates an oxygen concentration difference. This type can develop in areas like gaskets or joints. It requires special attention during design to prevent hidden corrosion. Monitoring and routine checks can help prevent such challenges.
Mechanisms of Corrosion
- Electrochemical Reactions
Electrochemical reactions drive corrosion processes. They involve the movement of electrons and ions, leading to material loss. This process is fundamental in understanding all types of corrosion. A key aspect to appreciate is that controlling these reactions can significantly reduce corrosion rates. - Oxidation Processes
Oxidation processes occur when metals react with oxygen. This aspect of corrosion often leads to formation of rust and other compounds. One crucial point is that oxidation is a natural phenomenon that needs to be managed, particularly in humid environments, to preserve steel's integrity. - Environmental Influences
Environmental factors play a significant role in corrosion. These include humidity, temperature, and the presence of salts. Each element can accelerate or hinder the corrosion process. Recognizing how these influences interact with materials leads to better protection strategies.
Factors Influencing Corrosion Rates
The issue of corrosion is layered and intricate. Understanding the factors affecting corrosion rates is crucial for effective mitigation strategies. Effective corrosion prevention relies not just on surface treatments but also on comprehending underlying conditions. Many elements influence corrosion, such as chemical properties, environmental conditions, and mechanical factors. Each factor plays a unique role. By analyzing these, one can develop more reliable steel applications.
Chemical Factors
The chemical environment surrounding steel is a prominent aspect that determines its corrosion behavior. Factors like pH levels, oxygen concentration, and ionic strength significantly affect corrosion rates.
pH Levels
The pH level of a solution plays a pivotal role in steel corrosion. A lower pH can accelerate corrosion processes. This happens because acidic environments favor oxidizing conditions that lead to increased metal dissolution. Conversely, neutral or slightly alkaline conditions often provide better corrosion resistance. Metals tend to passivate, forming a protective oxide layer in such conditions. Hence, monitoring pH levels is essential in industries where steel is used in aqueous environments. Yet, extreme pH levels can also weaken protective coatings, a double-edged sword that may necessitate careful balance.
Oxygen Concentration
Oxygen concentration in the surrounding environment affects the rate of electrochemical reactions. Elevated oxygen levels can enhance corrosion due to increased oxidation rates on the steel surface. In contrast, environments with low oxygen tend to slow down corrosion. Nonetheless, it is critical to maintain enough oxygen for necessary passivation processes without fostering excessive corrosion. Thus, oxygen concentration becomes a fundamental aspect in assessing steel corrosion risk in various applications, influencing protective measures accordingly.
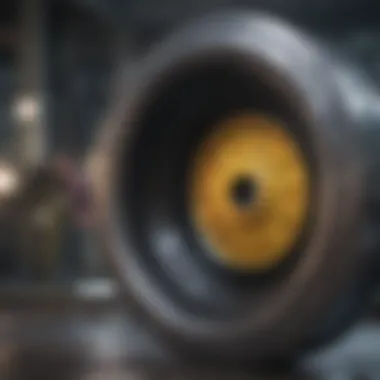
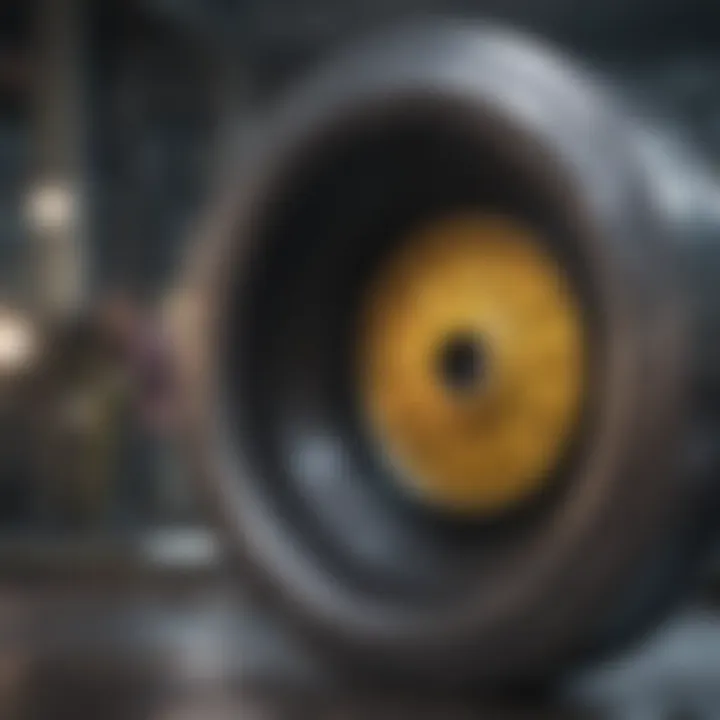
Ionic Strength
Ionic strength refers to the concentration of ions in a solution and significantly influences steel corrosion. Higher ionic strength typically enhances the conductivity of the solution, facilitating electrochemical reactions. This can lead to localized corrosion, such as pitting. While some ions may inhibit corrosion processes, others can accelerate it. The challenge lies in understanding the specific interactions between the metals and various ions present in their environment. This aspect makes ionic strength a critical factor in corrosion mitigation strategies.
Environmental Conditions
Environmental factors are also instrumental in determining corrosion rates. Variations in humidity, temperature, and the presence of salts can substantially influence steel integrity.
Humidity
Humidity levels in the environment can lead to accelerated corrosion. High humidity facilitates moisture accumulation on steel surfaces, creating an ideal medium for electrochemical reactions. This is particularly relevant in coastal regions or industrial settings. Managing humidity through proper ventilation or dehumidification can significantly enhance the longevity of steel structures. However, indoor environments can also be misleading as humidity can vary, necessitating continual monitoring.
Temperature
Temperature affects chemical reactions and corrosion processes. Generally, higher temperatures tend to accelerate corrosion rates due to heightened chemical activity. However, certain coatings may perform differently across various temperatures. For instance, temperature swings can lead to dehydration or moisture accumulation on surfaces, influencing protective barriers. Understanding temperature impacts is crucial for designing steel structures, especially in settings with extreme weather changes or temperature fluctuations.
Presence of Salts
The presence of salts is another significant contributor to the corrosion process. Salts can increase conductivity in water, promoting electrochemical reactions. This is particularly true for sodium chloride, commonly found in marine environments and roadways during winter. Managing exposure to salts through coatings or strategic design can mitigate their impact. However, the challenge lies in predicting salt exposure, which can vary widely based on location and usage.
Mechanical Factors
Lastly, mechanical factors like stress corrosion cracking, surface finish, and coating integrity are critical in understanding corrosion rates. These elements often interact synergistically with environmental and chemical conditions.
Stress Corrosion Cracking
Stress corrosion cracking occurs when tensile stress combines with corrosive environments. This phenomenon can lead to sudden steel failure, making it a critical consideration in design. Engineers must account for stress factors in exposed or loaded areas to mitigate risks. Strategies may include selecting less susceptible materials or applying stress-relieving techniques during fabrication. Thus, management of stress corrosion is imperative in high-stress applications.
Surface Finish
The surface finish of steel can determine its vulnerability to corrosion. Smoother surfaces are often less prone to corrosion as they present fewer sites for corrosion initiation. However, achieving optimal finishes can involve extensive processing, which can be costly and time-consuming. Evaluating surface characteristics might provide insights into corrosion resistance, hence guiding proper finishing in construction and manufacturing processes.
Coating Integrity
Coating integrity is vital for protection against corrosion. Deteriorated or damaged coatings can expose steel to corrosive agents. Regular inspection and maintenance of coatings are critical to ensure optimal performance. Sometimes, the use of advanced coatings that are more resistant may offer longer service life. However, the balance between performance and cost remains crucial, necessitating innovative solutions to sustain integrity over time.
Understanding how these factors influence steel corrosion rates can enhance preventive measures and extend the life of steel structures. By grasping these elements, industries can implement more effective corrosion management strategies.
Preventive Measures for Steel Corrosion
Preventive measures for steel corrosion are crucial to maintaining the integrity and longevity of steel structures. These measures not only prolong the lifespan of steel but also reduce maintenance costs and enhance safety. In environments where conditions promote corrosion, effective strategies can greatly mitigate degradation.
Several techniques can be implemented to protect steel from corrosion, including protective coatings, galvanization, and cathodic protection. Each method has its unique features and effectiveness, making it important to choose the right one based on specific requirements and conditions. Understanding and applying these preventive measures can result in significant benefits for industries relying on steel.
Protective Coatings
Paints and Sealants
Paints and sealants serve as a primary defense mechanism against corrosion. They create a barrier that prevents moisture and corrosive agents from reaching the steel surface. One key characteristic of paints and sealants is their ability to be easily applied on various steel structures, which makes them a convenient choice.
The unique feature of these products is their versatility. They come in various formulations to suit different corrosion threats and aesthetic needs. However, their performances can vary, as they may require regular maintenance and touch-ups, leading to higher long-term costs in certain situations.
Polymer Coatings
Polymer coatings have gained popularity due to their exceptional resistance to chemicals and moisture. These coatings can significantly enhance the protective qualities of steel. A notable characteristic of polymer coatings is their flexibility, which allows them to withstand movement and thermal expansion without cracking.
The unique feature of polymer coatings lies in their self-healing properties. In case of minor damages, the polymer can restore itself, offering a sustained protection. However, these coatings can sometimes be more expensive compared to traditional options, which might limit their use in budget-sensitive projects.
Zinc Coatings
Zinc coatings, commonly applied through hot-dip galvanizing, offer a robust solution for protecting steel. The primary characteristic of zinc is its high corrosion resistance, which provides sacrificial protection; this means that zinc will corrode before the underlying steel does.
The unique feature that makes zinc coatings effective is their longevity. They provide long-lasting protection and can withstand harsh environments. The disadvantages include their limited aesthetic appeal and the challenges associated with repairing damaged areas, as zinc cannot be easily painted over.
Galvanization
Hot-Dip Galvanizing
Hot-dip galvanizing is a widely used method of corrosion protection for steel. This process involves immersing steel in molten zinc, which adheres to the surface and forms a thick protective layer. Its significant characteristic is the strength of the bond formed between zinc and steel, providing excellent protection.

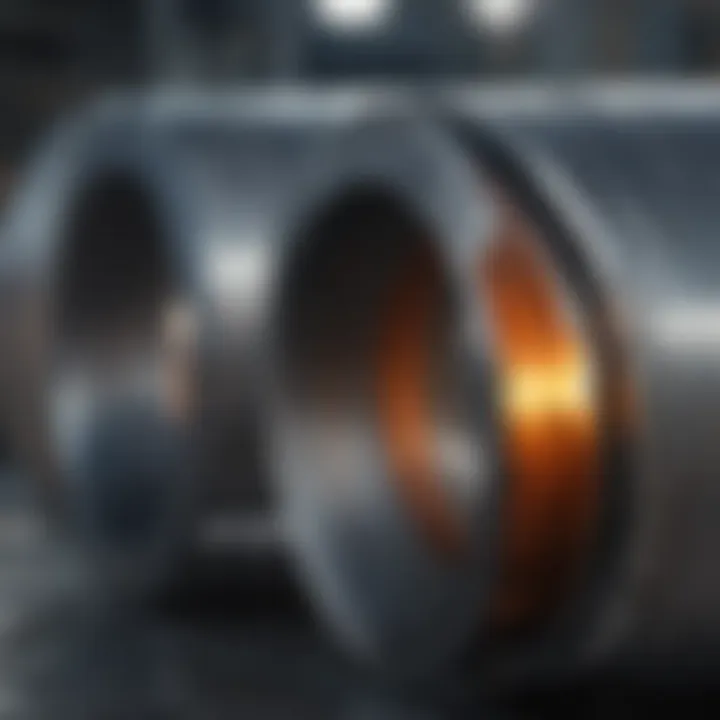
This method is beneficial due to its robust nature, ensuring long-term corrosion resistance suitable for various applications. However, a drawback is the potential for uneven coating thickness and a limited range of colors for aesthetic choices.
Electrogalvanizing
Electrogalvanizing involves applying a thin layer of zinc to steel through an electrochemical process. This method is known for producing a smoother finish, which is particularly beneficial when a clean appearance is required. Its main characteristic is the uniformity of the zinc layer, leading to consistent protection.
While electrogalvanizing can enhance aesthetic appeal, it may not provide the same level of corrosion resistance as hot-dip galvanizing, especially in highly corrosive environments. This could lead to a need for more frequent inspections and repairs.
Advantages and Limitations
The advantages of galvanization include substantial improvements to steel's durability, extended service life, and reduced maintenance. However, limitations exist, such as costs and potential challenges during application. Over time, careful consideration of these factors is essential in choosing galvanization as a protective strategy.
Cathodic Protection
Impressed Current Systems
Impressed current systems play a critical role in protecting steel structures from corrosion. They work by supplying a constant electric current to the steel, making it the cathode in an electrochemical cell. A key feature of this system is its flexibility in design, allowing it to be tailored to specific structures and environments.
Impressed current systems are beneficial because they can provide effective protection even in highly corrosive environments. However, they require a more complex installation and maintenance than other methods, which could lead to increased costs in the long run.
Galvanic Systems
Galvanic systems rely on electrochemical processes to prevent corrosion by using sacrificial anodes. These anodes corrode instead of the protected steel, thereby prolonging its life. A key characteristic of galvanic systems is their simplicity; they do not require external power sources, making them easy to install and maintain.
The unique feature of galvanic systems is their self-regulating nature, often suited for smaller structures. However, their effectiveness can diminish over time as the anode is consumed, leading to a limited service life that must be factored into overall corrosion management strategies.
Design Considerations
Design considerations for corrosion protection are essential for effective implementation. Factors such as environmental conditions, structure size, and intended use must be analyzed when developing a protection scheme. A critical characteristic is the need for an interdisciplinary approach, combining knowledge from materials science, electrical engineering, and environmental science.
The unique aspect of design considerations is their ability to impact the long-term success of corrosion protection methods. Properly designed systems maximize effectiveness and efficiency while minimizing costs. However, poor design could result in insufficient protection and costly repairs, emphasizing the importance of thorough planning in corrosion management.
Advancements in Corrosion Protection Technologies
The field of corrosion protection has seen significant advancements in recent years. This progress is crucial for improving the longevity and reliability of steel structures. With the increasing costs associated with corrosion damage, innovative technologies can offer more effective solutions. The focus on these advancements is not only about enhancing traditional methods but also about integrating new materials and monitoring techniques. As a result, industries can benefit from both performance efficiency and economic savings.
Nanotechnology Applications
Nanocoatings
Nanocoatings are thin layers that incorporate nanomaterials. These coatings provide superior protection against corrosion. One of their key characteristics is the ability to form a dense barrier that minimizes exposure to corrosive environments. This property makes them a popular choice in various applications, from automotive to construction. A unique feature of nanocoatings is their self-cleaning ability, which allows them to maintain their protective qualities over time. However, there are disadvantages, such as the cost and complexity of application.
Smart Coatings
Smart coatings represent another leap in corrosion protection. These coatings can actively respond to environmental changes. This characteristic not only prolongs their life but also reduces maintenance needs. Their popularity comes from their versatility in various applications. A unique feature of smart coatings is the incorporation of sensors. These sensors can detect corrosion and signal through color change or other means. However, this technology can be expensive and requires careful calibration to function optimally.
Self-Healing Materials
Self-healing materials have unique properties that allow them to restore their integrity after damage. This characteristic is vital for maintaining corrosion protection under harsh conditions. These materials are beneficial due to their ability to prolong the lifespan of steel structures without requiring immediate repair. A notable feature is the embedded microcapsules containing healing agents that can activate when fissures occur. The main disadvantage lies in their still-developing nature, where long-term performance and costs can be a concern.
Innovative Alloy Development
Corrosion-Resistant Alloys
Corrosion-resistant alloys are specially designed to withstand corrosive environments. Their key characteristic lies in the composition, which is tailored to enhance resistance against specific corrosion types. These alloys are a beneficial addition to the industry due to their ability to extend the service life of components. A unique aspect is their adaptability, as they can be used in various applications from marine to chemical processing. However, they often come with a higher upfront cost compared to standard steel.
Composite Materials
Composite materials combine different substances to achieve desirable properties. The significant advantage of composite materials is their resistance to corrosion without compromising structural integrity. They are gaining popularity due to their lightweight characteristics and compliance with diverse specifications. A notable feature is the use of polymer matrix composites that are exceptionally resistant to environmental degradation. However, these materials can be limited in high-stress environments due to lower mechanical strength compared to metal alloys.
Research Trends
Research trends focus on understanding new methods and materials for corrosion prevention. Highlighted is an emphasis on sustainability through eco-friendly solutions. This focus benefits industries looking to reduce their environmental impact. One important aspect of ongoing research is the development of biodegradable coatings that can offer protection without harmful residues. However, the challenge remains in balancing performance with environmental considerations, which can sometimes lead to compromises in capabilities.
Corrosion Monitoring Technologies
Electrochemical Impedance Spectroscopy
Electrochemical Impedance Spectroscopy (EIS) is a powerful technique for assessing corrosion processes. Its key characteristic is the ability to measure the impedance of a material when subjected to an electrical stimulus. This method is beneficial in providing real-time data on the condition of steel, enabling proactive maintenance decisions. A unique feature of EIS is its non-destructive nature, which means it does not harm the structure being tested. However, interpreting EIS data can be complex and requires expertise.
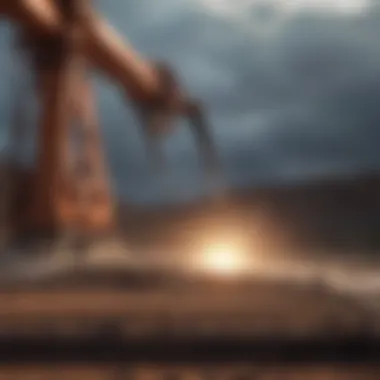
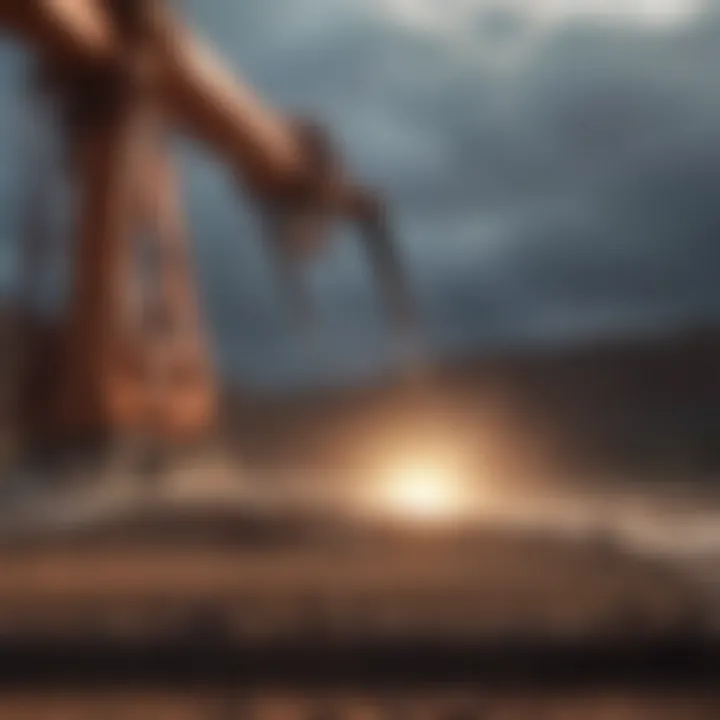
Wireless Monitoring Systems
Wireless monitoring systems allow for continuous tracking of corrosion conditions. Their main advantage is convenience, as they provide data remotely, reducing the need for physical inspections. These systems can integrate with existing infrastructure, making them a flexible option for industries. A notable feature is the use of sensors that transmit data to centralized platforms for analysis. Despite their advantages, these systems can face issues such as connectivity limitations in remote areas.
Predictive Maintenance Tools
Predictive maintenance tools use data analytics to forecast potential corrosion issues. Their key strength lies in the ability to schedule maintenance before failure occurs, thus extending asset life. This proactive approach is increasingly recognized as a cost-saving strategy across various industries. The unique feature of these tools is their ability to leverage historical data, enhancing decision-making processes. However, they require initial investments and ongoing data management to be effective.
Regulatory Standards and Guidelines
The role of regulatory standards and guidelines in steel corrosion protection cannot be overstated. They establish the norms and criteria that govern materials, processes, and applications in various industries. These regulations ensure compliance with safety, performance, and environmental requirements. For professionals in engineering and related fields, understanding these standards is crucial for both the design and maintenance phases of steel structures. Adhering to these guidelines not only enhances durability but also reduces costs associated with mitigation and repairs.
International Standards
ISO Standards
The International Organization for Standardization (ISO) develops standards that apply to numerous areas, including steel corrosion management. One significant aspect of ISO standards is their global recognition. They create a common framework for best practices that can be applied across different regions.
Key characteristics of ISO standards include reliability and comprehensiveness. They cover specifications for materials, coating systems, and even testing methods. This makes them a popular choice among engineers for ensuring product quality and performance.
One unique feature of ISO standards is the detailed criteria they provide for assessing corrosion-resistant materials. Their advantages include increased international trade compatibility and assurance of product quality. However, the generality of these standards can sometimes lead to discrepancies in implementation across various industries.
ASTM Standards
The American Society for Testing and Materials (ASTM) facilitates the development of specifications that define product properties and testing methods. ASTM standards are especially prevalent in the United States and are recognized for their specific focus on materials testing, which includes corrosion resistance.
A primary characteristic of ASTM standards is their rigorous testing methodologies. They are frequently updated, making them relevant to current technological advancements. This focus on continual improvement makes ASTM standards a beneficial choice for this subject.
A notable feature of ASTM standards lies in their specificity, which includes precise criteria for testing and evaluation. Such rigor ensures that the standards are aligned with the latest corrosion protection technologies. However, the frequent updates can necessitate constant adaptation by companies implementing these standards.
National and Regional Regulations
US Regulations
In the United States, several regulations govern the corrosion protection of steel structures. The Federal Highway Administration (FHWA) has issued guidelines regarding protective measures, particularly in infrastructure projects. A key characteristic of US regulations is their focus on infrastructural durability. The intention is to extend service life and reduce maintenance costs in public works.
These regulations are beneficial for ensuring public safety and long-term sustainability. The unique feature of US regulations is the incorporation of local environmental conditions into their design criteria. However, diverse applications and contexts might lead to inconsistent implementation across different states.
European Directives
European directives set stringent standards for environmental protection and sustainability, which significantly influence steel corrosion practices. These regulations aim to harmonize rules across member states to ensure the same level of safety and performance. A notable characteristic of European directives is their strong emphasis on minimizing environmental impacts.
This approach promotes innovative techniques and materials that are both effective and eco-friendly, making them a popular choice in the market. One unique aspect is the requirement for regular assessments and updates, ensuring that the governing standards remain current with emerging research. However, varying applications across different countries can complicate compliance for companies operating in multiple regions.
Industry Best Practices
Guidelines for Design
When designing steel structures, following established guidelines is essential for avoiding corrosion-related failures. Best practices emphasize a holistic approach by considering environmental conditions, material selection, and protective measures during the design phase. A key characteristic is the integration of corrosion resistance principles into all aspects of design, ensuring that the final structure is durable and reliable.
These guidelines are critical. They provide a framework that aids engineers in making informed decisions, thus reducing risks of premature failures. One unique aspect is the emphasis on initial lifecycle evaluations, which help in understanding long-term impacts. While beneficial, overly rigid guidelines can sometimes limit creativity in design.
Maintenance Protocols
Regular maintenance is a cornerstone in the fight against corrosion. Established protocols help in identifying and addressing potential corrosion issues before they escalate. These protocols focus on inspection, maintenance, and repair strategies that are essential for prolonging the lifespan of steel structures. A key characteristic is the systematic approach, which includes scheduled inspections and timely interventions.
These practices ensure the integrity of structures and provide peace of mind to stakeholders. Unique features include the flexibility to adapt to specific environmental conditions or material usages. However, some organizations may find it challenging to maintain consistent adherence to these protocols due to resource constraints.
Epilogue
The significance of understanding steel corrosion protection cannot be overstated. This article has explored various strategies and innovations aimed at preventing corrosion, illustrating the multifaceted nature of the challenge. Steel, widely used in construction and manufacturing, is essential due to its strength and versatility. However, its susceptibility to corrosion poses real threats to structural integrity and longevity.
Every protective measure, from coatings to cathodic protection, serves to enhance the durability of steel. They provide not only physical barriers but also chemical solutions that hinder the processes of degradation. The thorough examination of these methods reveals that no single strategy is universally applicable. Instead, the best results often arise from a combination of approaches, tailored to specific environments and conditions.
Moreover, engaging with regulatory standards and guidelines helps ensure that best practices are adopted across industries. Knowledge of these standards is crucial for professionals tasked with design, maintenance, and compliance. The discussion of advancements in technology, including nanotechnology and corrosion monitoring systems, suggests that the field is on the brink of significant transformation.
"The fight against corrosion is ongoing and requires both innovation and strict adherence to standards to be truly effective."
Synthesis of Findings
In synthesizing the findings, it is clear that corrosion protection is not merely about applying a solution; it involves a comprehensive understanding of the materials used and the environments they inhabit. Regular monitoring and assessment of corrosion risk factors can lead to timely interventions and cost savings in maintenance and repairs. Adopting corrosion-resistant materials or employing advanced protective technologies are vital strategies that ensure longevity in steel applications. The complexities revealed in the analysis emphasize that informed choices on corrosion prevention can lead to enhanced reliability and safety in all steel-reliant structures.
Future Research Directions
Future research should focus on several key areas to further improve steel corrosion protection. Firstly, investigations into more effective coatings that utilize advanced materials science could yield significant improvements. The development of smart coatings that respond to environmental changes and self-heal presents a promising avenue. Secondly, the integration of artificial intelligence in corrosion monitoring and predictive maintenance could pave the way for more proactive measures. This technology might allow for automatic data collection and analysis, providing insights into potential failure points.
Finally, the exploration of new alloy compositions with superior resistance to specific corrosion types is essential. These innovations could redefine standards for durability in extreme environments, such as marine or industrial settings. Overall, ongoing research and collaboration among scientists, engineers, and industry leaders are crucial in the battle against corrosion, ensuring that protective strategies evolve to meet the challenges ahead.