Metal Laminates: Composition, Processes, and Uses

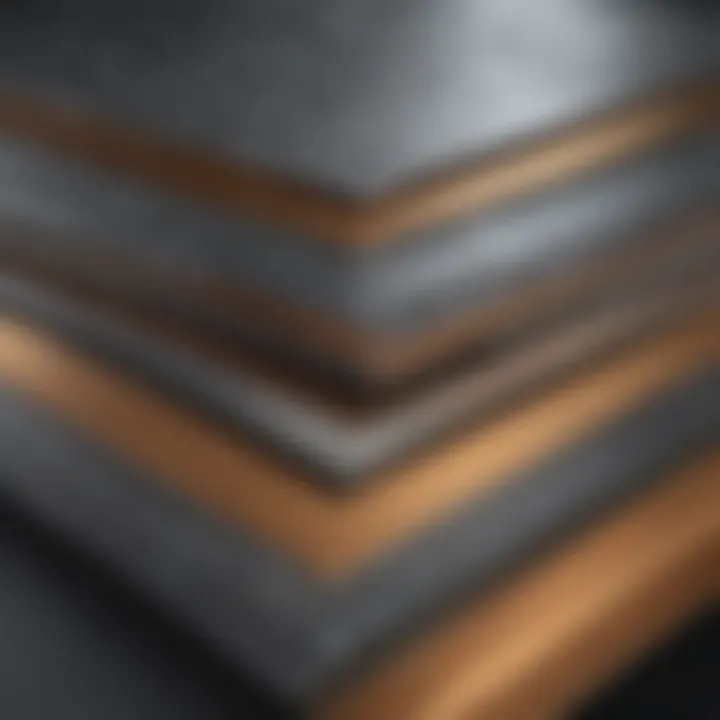
Intro
In the realm of material science, metal laminates emerge as a fascinating subject worthy of in-depth exploration. These composites, which consist of multiple layers of metal, present unique properties that offer advantages in both practical applications and aesthetic appeal. At the core of their composition lies a blend of metals, often paired with other materials, which grant them remarkable strength and versatility in various industries.
Understanding the fundamental principles guiding the creation and usage of metal laminates is essential for professionals and enthusiasts seeking to leverage their potential. This article will shed light on their manufacturing processes, applications, and the innovations that are shaping their future.
Methodology
To gain a comprehensive perspective on metal laminates, this section outlines the approach taken in researching this topic. By adopting a systematic study design, we aimed to capture both foundational concepts and advanced applications of these materials.
Study Design
A mixed methods approach was employed during this research, combining qualitative analyses with quantitative measurements. The study involved reviewing existing literature related to metal laminates, their properties, and industry applications. This allowed for a thorough understanding of current trends, as well as the identification of gaps where further research could be beneficial.
Data Collection Techniques
Data was gathered through various sources:
- Peer-reviewed articles and journals to understand theoretical perspectives.
- Industry reports that highlight practical applications in sectors such as aerospace, automotive, and construction.
- Interviews with professionals in the field to gain insights into real-world challenges and innovations surrounding the use of metal laminates.
Discussion
Interpretation of Results
The findings reveal a striking convergence between the technical benefits of metal laminates and their growing role in modern manufacturing. Notably, the use of composite materials can significantly reduce weight while maintaining structural integrity, which is particularly advantageous in the aerospace and automotive industries.
Additionally, metal laminates have gained traction in architectural design due to their aesthetic qualities, allowing for creative expression without compromising functionality. This intersection of artistry and engineering speaks to the dual nature of metal laminates, serving utilitarian and visual needs simultaneously.
"The combination of form and function within metal laminates opens up endless possibilities, making them a favorite in innovative designs across various sectors."
Limitations of the Study
While this study provides valuable insights, it is not without its limitations. The rapid advancement in laminate technology often outpaces available literature, making it challenging to cover all recent developments comprehensively. Moreover, variations in regional regulations and standards can influence the adoption and usage of these materials, highlighting the need for context-specific research.
Future Research Directions
Looking ahead, several avenues for further investigation emerge:
- The environmental impact of metal laminates during and after their lifecycle should be scrutinized to align with sustainable practices.
- Exploring new combinations of materials that could enhance the properties of metal laminates further could yield innovative applications.
- Studying the long-term performance of metal laminates in extreme conditions, such as high humidity or severe temperature fluctuations, may reveal additional strengths or weaknesses.
Foreword to Metal Laminates
In today's fast-paced manufacturing world, metal laminates have carved out a significant niche. These composite materials not only boast enhanced properties but are also adaptable to various applications across numerous industries. Understanding the fundamentals of metal laminates is crucial for professionals engaged in fields such as aerospace, automotive, architecture, and even electronics. Their increasing relevance lies in their ability to combine different metals, bringing together the best properties of each material, resulting in robust and lightweight structures.
Definition of Metal Laminates
Metal laminates are materials that consist of layers or sheets of metals that are bonded together, creating a composite structure. These layers can be composed of various types of metals like aluminum, steel, or titanium, which are intimately joined using various methods such as adhesives or mechanical fasteners. The resultant laminate exhibits unique properties that often surpass those of individual layers. Metal laminates can be engineered to achieve specific characteristics, such as increased strength or better corrosion resistance, making them versatile in application.
Historical Context
The journey of metal laminates is intertwined with advancements in materials science. Historically, engineers and artisans understood the benefits of layering materials. For example, the ancient Egyptians utilized combinations of copper and other metals to create stronger tools and items. However, the modern notion of metal laminates began to take shape during the mid-20th century, particularly as industries sought lightweight yet strong materials for aircraft and automobiles. As technology progressed, the methods of lamination evolved, leading to the sophisticated techniques we see today. This evolution not only improved the performance of metallic structures but also opened new doors for innovative applications in various technical fields.
"The history of metal laminates is a testament to human ingenuity and the relentless pursuit of improvement in material efficiency and performance."
Exploring the history and definition lays the foundation for comprehending the intricate composition and manufacturing processes that further enhance the potential of metal laminates.
Composition of Metal Laminates
The composition of metal laminates plays a crucial role in determining their overall performance and applicability across various sectors. In essence, metal laminates combine different metals, each adding its unique properties to create a composite material that overcomes the limitations of individual components. By carefully selecting these materials, manufacturers can enhance the durability, strength, and aesthetic appeal of the final product. Understanding the specific types of metals used and the techniques for layering them not only informs pressing choices for engineers and designers but also ensures the sustainability and efficiency of the materials in use.
Types of Metals Used
Aluminum
Aluminum is a light-weight champion often favored for its ease of handling and compatibility with diverse applications. This metal possesses a remarkable strength-to-weight ratio, allowing the creation of laminates that don't compromise on stability while keeping overall weight low. Its corrosion resistance is another highlight that contributes to longevity in harsh environments.
One unique feature of aluminum is its ability to form complex shapes and surfaces, which opens a door to aesthetic versatility. This property makes aluminum laminates a popular choice not only in functional applications but also in designs where appearance matters.
However, aluminum can be less rigid than other metals, which could be a consideration in high-load applications where stiffness is essential.
Steel
When it comes to strength, steel is a heavyweight contender. Renowned for its structural integrity, steel is a go-to in constructions where durability is paramount. Just like aluminum, steel exhibits excellent resistance to high temperature and wear, making it suitable for demanding applications.
A definitive characteristic of steel is its ability to be easily welded, allowing for seamless integration into larger structures. Steel laminates often deliver high load-bearing capacity, which can be advantageous in industries like construction and aerospace. On the flip side, steel can be heavier than aluminum and is more prone to rust without adequate protective coatings.
Copper
Copper brings a unique set of properties to the table, particularly with its high electrical and thermal conductivity. This makes it indispensable in electronics and electrical engineering applications. Copper laminates are often favored to create efficient heat sinks and circuit boards.
One extraordinary aspect of copper is its malleability, which allows for sophisticated designs in laminations. However, copper's tendency to tarnish when exposed to the atmosphere could require additional surface treatments to maintain aesthetic and functional qualities over time.
Titanium
Titanium distinguishes itself with its exceptional strength-to-weight ratio and outstanding corrosion resistance. It's often the metal of choice in high-performance applications, such as those found within the aerospace sector.
A notable feature of titanium is its biocompatibility, making it highly suitable for medical applications, including implants. However, working with titanium can be challenging due to its cost and the complexity in its machining processes. The heavy investment might deter smaller enterprises from incorporating titanium laminates, but for those who commit, the returns can be substantial.
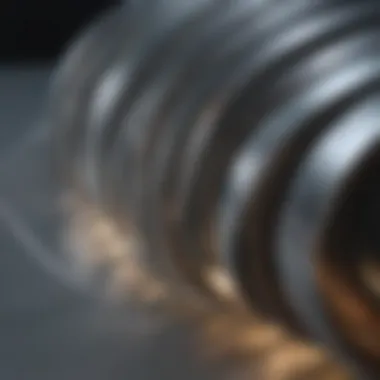
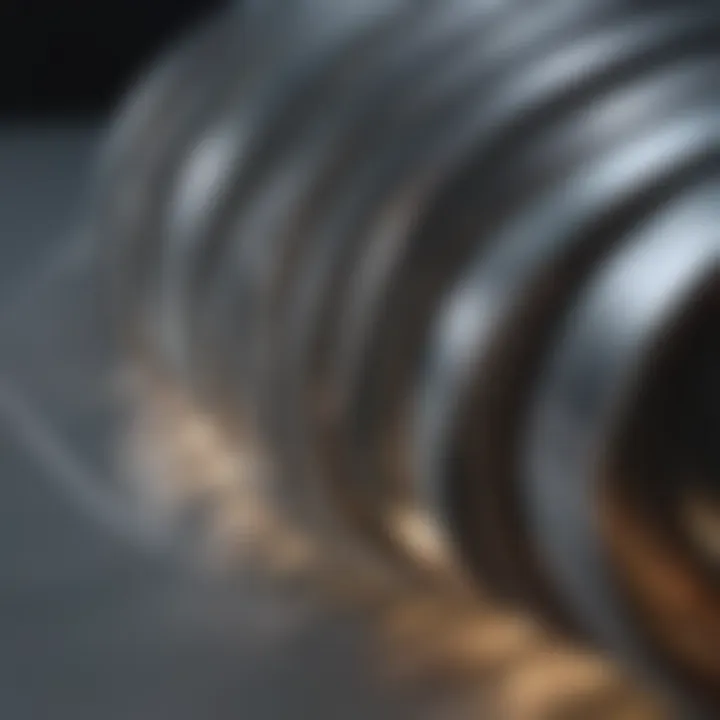
Layering Techniques
The process of layering metals into a laminate is just as critical as the materials themselves. Various techniques exist, each impacting the final properties of the laminate.
- Cold Lamination allows for precision layering without damaging the metals involved. It's often used when maintaining material integrity is crucial.
- Hot Lamination, on the other hand, involves the application of heat and pressure, which can bond metals more effectively, leading to lamination that can withstand harsher conditions.
Understanding these techniques is essential to producing effective laminates that meet specific industry standards and end-user needs.
Manufacturing Processes
The manufacturing processes for metal laminates are pivotal in determining their quality, performance, and overall suitability for various applications. Understanding how these materials are produced can help professionals recognize the best options for their specific needs. The right processes enhance both functionality and aesthetic appeal, while also ensuring cost-effectiveness. Factors such as method selection, material compatibility, and intended use must be kept in mind to achieve optimal results.
Lamination Techniques
Cold Lamination
Cold lamination is a straightforward yet effective technique, widely noted for its ability to maintain the integrity of the materials used. This method involves layering metal sheets without applying heat, relying instead on the use of adhesives or mechanical pressure. One of the key characteristics of cold lamination is the seamless bond it forms, making it a preferred choice in many industries.
Unlike hot processes, cold lamination preserves the material’s original properties, such as strength and ductility. This unique feature allows it to be advantageous in applications where excessive heat could be detrimental. However, it is not without its downsides. The bonding agents used may not withstand extreme temperatures or environmental stress over time, which could pose a risk in certain applications.
Hot Lamination
In contrast, hot lamination involves applying heat and pressure to bond metal layers. This method is beneficial because it often results in a more robust connection between layers. Hot lamination facilitates the merging of metals at a molecular level, which enhances the overall structural integrity of the laminate.
The heat applied can also enable the use of various alloys that wouldn’t normally work well with cold lamination, expanding the material palette available to manufacturers. However, a critical downside is that the heating process might induce warping or change in the characteristics of the base materials. Therefore, while hot lamination can yield superior performance in terms of strength, manufacturers must carefully manage the heat application to avoid compromising the material properties.
Joining Methods
Welding
Welding is a preferred joining method due to its strong bond and durability. It involves the melting of the base metals to create a solid connection, which results in high strength joints. This characteristic makes welding an ideal choice for applications requiring significant load-bearing capabilities. Another advantage is the versatility of welding; it can be applied to a variety of metal types, including aluminum and steel, making it widely applicable in different sectors.
However, welding may introduce residual stresses and requires careful control of parameters to avoid defects like warping or cracking, often necessitating additional finishing processes.
Adhesive Bonding
Adhesive bonding relies on specialized formulations that provide strong bonds between metal layers. The key benefit of this method is its ability to join dissimilar materials, which is often a challenge with traditional methods like welding. Adhesives can distribute stress more evenly across the joint, lowering the risk of failure. Additionally, adhesive bonding does not require heat, which preserves the mechanical properties of the materials involved.
On the flip side, adhesive bonds may be susceptible to environmental factors such as moisture exposure and temperature fluctuations, potentially compromising long-term performance.
Mechanical Fastening
Mechanical fastening incorporates the use of bolts, screws, or rivets to connect metal sheets. This approach offers the benefit of disassembly, allowing easy repair or replacement of parts without requiring invasive methods. The key characteristic of mechanical fastening is its straightforward implementation and reliability—components can be constructed securely without the need for extensive equipment or specialized training.
One limitation is that mechanical fasteners can introduce stress concentrations, which could lead to fatigue over time depending on the application's load conditions. Thus, while mechanical fastening remains an accessible and valid choice, careful design is needed to mitigate long-term durability issues.
Properties of Metal Laminates
Metal laminates are celebrated for their distinct properties that inherently contribute to their rising popularity across various industries. Understanding these properties is essential, as they not only reveal the intrinsic benefits of metal laminates but also elucidate their role in modern engineering and design. This section will delve deeper into the mechanical, thermal, and corrosion-resistant properties that make metal laminates a pivotal choice in many applications.
Mechanical Properties
Mechanical properties make up the backbone of any material's composition, and for metal laminates, they are no different. These properties mainly emphasize strength, ductility, and stiffness, which play a resonant role in how metal laminates are employed in real-world situations.
Strength
Strength is, arguably, one of the most crucial factors when it comes to materials used in construction and manufacturing. In this article, the focus on strength underscores its significance in ensuring that the end product can withstand various stresses during use.
- The key characteristic of strength in metal laminates is its ability to combine different metals, which not only enhances durability but also allows for weight reductions.
- Factors such as tensile strength and yield strength determine how much load a metal laminate can handle before deforming or failing, thus making it a favorable choice for industries where structural integrity is non-negotiable.
- The unique feature of strength in metal laminates is their exceptional capacity to withstand both static and dynamic loads. This property translates into advantages like increased safety in aircraft and automotive applications, while any potential downside, such as increased costs in high-strength materials, is often mitigated by the long-term savings in maintenance and durability.
Ductility
Ductility refers to a material's ability to deform under tensile stress, which is a vital aspect of metal laminates. It's not just about how strong a material is, but how well it can bend and take shape under pressure without breaking.
- The key characteristic here is that ductile materials can be formed into complex shapes, giving designers and engineers great flexibility in their projects.
- Ductility is essential for applications requiring bent or complex structures, making it a popular choice in various fields including automotive and aerospace.
- A unique feature of ductility in metal laminates is how it complements strength; they can absorb energy in impacts without fracturing, reducing the risk of catastrophic failure. However, this can also pose disadvantages in situations where rigidity is required, as excessive ductility can lead to unnecessary deformations.
Stiffness
Stiffness is a measure of a material's resistance to deformation when subjected to an applied force, and it's undeniably an important property in metal laminates.
- A key characteristic of stiffness lies in its direct impact on the rotational and lateral stability of structures, thus affecting their overall behavior under load. High stiffness often signifies a material's capability to maintain its form under stress, which is crucial in applications like bridges or architectural components.
- In this article, stiffness is introduced as a beneficial choice due to its provision of structural integrity and reduced vibrations, which is invaluable in construction and aerospace structures.
- The unique feature of stiffness within metal laminates is its tunability. By adjusting the combination of metals and layering techniques, engineers can produce laminates with desired stiffness properties. On the downside, increased stiffness can also lead to reduced ductility and an increased likelihood of cracking under certain conditions.
Thermal Properties
For many applications, the thermal properties of materials can determine their suitability. Metal laminates offer valuable traits in terms of conductivity and heat resistance that are vital for operability in extreme conditions.
Conductivity
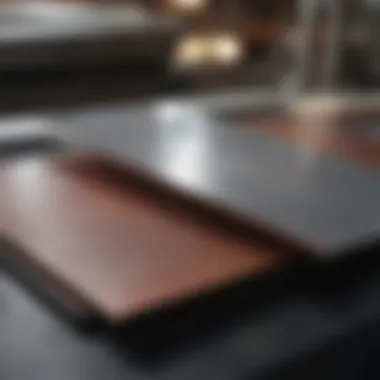
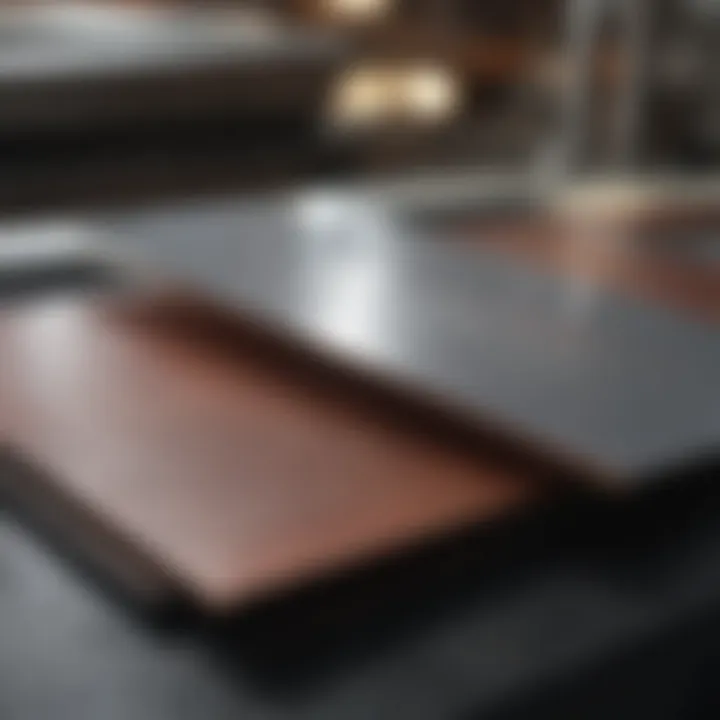
Conductivity, specifically thermal conductivity, represents how well a material can conduct heat. This property is especially crucial in applications ranging from electronics to cooking equipment.
- The key characteristic of conductivity in metal laminates lies primarily in the choice of metals used. For instance, laminates that utilize copper tend to exhibit superior thermal conductivity, which is critical for applications requiring efficient heat dissipation.
- High conductivity is a beneficial trait in the electronics industry, where heat management is essential for performance and longevity of components, making metal laminates favorable for heat sink applications.
- An intriguing aspect of conductivity is the layering itself; different metals can be combined to strategize thermal conductance. However, the disadvantages may arise in weight considerations, as higher conductivity materials can also mean increased mass.
Heat Resistance
Heat resistance speaks to a material’s ability to withstand high temperatures without significant degradation. This property often dictates the durability of metal laminates in high-temperature settings.
- A key characteristic of heat resistance in metal laminates is their formation utilizing heat-tolerant metals, making them ideally suited for sectors like aerospace or automotive.
- Heat resistance is essential for maintaining performance under thermal stress, especially in environments subject to fluctuating temperatures.
- The unique feature of heat resistance in metal laminates comes from their potential to be tailored for specific heat-related challenges. This adaptability can be a double-edged sword, for while laminates might provide resistance at certain temperatures, without proper selection, they might also fail in more extreme scenarios.
Corrosion Resistance
Lastly, corrosion resistance is another vital property of metal laminates that cannot be overlooked. It concerns the material's capacity to withstand degradation due to environmental factors.
- Corrosion resistance enhances durability and lowers the need for frequent replacements, a crucial aspect in industries like automotive or construction, where exposure to harsh elements is commonplace.
- Metal laminates often employ protective surface treatments or combine corrosion-resistant alloys, allowing them to endure in various environmental conditions.
- While corrosion resistance provides significant advantages, it’s important to note that not all combinations of metals offer the same level of protection, necessitating careful selection and consideration in metallurgical design.
"In today’s rapidly advancing industrial landscape, understanding the properties of metal laminates is not just an academic exercise; it's a gateway to innovation and efficiency."
In summary, the properties of metal laminates are integral to understanding their applications across various sectors. These include mechanical attributes like strength, ductility, and stiffness, as well as thermal properties, such as conductivity and heat resistance, culminating in corrosion resistance. Each aspect contributes to a material profile that is adaptable, durable, and efficient.
Applications of Metal Laminates
The applications of metal laminates are vast and varied, penetrating multiple industries due to their unique properties. They are not just a passing trend; they are becoming fundamental in sectors where strength, weight, and aesthetic appeal are paramount. The importance of understanding these applications allows professionals and enthusiasts alike to leverage the advantages that metal laminates offer, enhancing product performance and durability. This segment aims to provide a clear perspective on where these materials shine the most and why they are often preferred in various contexts.
Aerospace Industry
In the aerospace realm, where every gram counts, metal laminates have become pivotal in constructing lightweight yet strong aircraft components. The combination of metals like aluminum with stronger substrates results in parts that boast remarkable strength-to-weight ratios. Here, performance isn't just an add-on; it's the essence of flight.
Consider the use of laminates in aircraft wings. They require structures that can withstand extreme forces while minimizing mass. Metal laminates, with their layered structure, provide the necessary flexibility and resilience against the stresses of altitude and speed. Furthermore, these materials greatly increase fuel efficiency, contributing to better environmental performance, a growing concern in the aerospace sector.
Automotive Applications
The automotive industry, known for its relentless push towards innovation, is also embracing metal laminates in various ways. Here, safety and aesthetics come hand in hand. Car manufacturers are increasingly integrating metal laminates into body panels and structural components, which not only enhance aesthetic appeal but also bolster crashworthiness.
Imagine a vehicle where the body panels are composed of metal laminates. This design mitigates dents and scratches while reducing overall weight, allowing for dynamic driving experiences. In addition, as electric vehicles gain traction, lighter materials are essential to extending battery lives and range. Thus, the role of laminates extends from performance to sustainability, aligning with the industry's evolving goals.
Architectural Uses
Architecture is not just about erecting buildings; it’s about creating experiences. Metal laminates bring a unique aesthetic flair to structures, offering visually striking façades and interiors without the weight burden of solid metal. They are becoming a go-to choice for architects seeking to achieve modern designs with clean lines and appealing finishes.
A notable example is in high-rise buildings, where the cladding systems often incorporate metal laminates. These applications create dramatic visual effects while providing essential insulation and weather resistance. Additionally, the varied textures and finishes available allow architects to play with light and shadow, enhancing the building's profile against the skyline. This blend of functionality and artistic expression makes metal laminates an attractive option in contemporary architecture.
Electronics and Electrical Engineering
The electronics sector, too, is feeling the impact of metal laminates. They find significant use in heat sinks and circuit boards due to their thermal conductivity and lightweight characteristics. In this fast-paced, ever-evolving industry, the ability to dissipate heat efficiently can be the difference between a product’s success or failure.
Key components, like those in computers and mobile devices, leverage metal laminates for specific heat management applications. This ensures longer product lifespans and optimal performance, aligning with consumer demands for reliability. Moreover, the aesthetic appeal of metal laminates makes them suitable for visible components, blending functionality with design.
In summary, metal laminates are shaping the future across diverse sectors, offering innovative solutions to old problems, while also pushing the boundaries of what is possible in design and engineering.
Understanding the scope of metal laminate applications highlights their integration into our modern world. As industries continue to evolve and seek sustainable alternatives, metal laminates stand out not only for their mechanical benefits but also for their artistic potential.
Benefits of Utilizing Metal Laminates
Metal laminates have carved out a distinctive niche in modern materials engineering, offering a plethora of advantages that cater to various industries. Their unique characteristics allow them to meet complex demands that traditional materials often fail to satisfy. Let’s unwrap these benefits one by one, considering their importance in application and functionality.
Enhanced Strength-to-Weight Ratio
The strength-to-weight ratio in engineering materials often plays a crucial role, especially when it comes to sectors such as aerospace and automotive. Metal laminates deliver an impressive feat; they combine the robustness of metals with a lighter profile than traditional solid metals.
For instance, when you think about an airplane wing that needs both durability and lightness, it becomes clear why the strength-to-weight ratio is paramount. Engineers are turning increasingly towards materials like aluminum laminates for structural components. These laminates can withstand considerable stress while maintaining a low weight, leading to improved fuel efficiency and reduced energy consumption.
The savvy choice of metal laminates for high-performance projects hinges on their exceptional strength-to-weight ratio, helping accelerate advancements in technology and design.
Scholars and practitioners alike are more inclined to explore metal laminates in projects that require optimization of load-bearing capacity yet should not weigh a ton. In this context, utilizing metal laminates becomes not merely advantageous but also imperative for enhanced performance.
Aesthetic Versatility
A frequently overlooked benefit of metal laminates is their aesthetic versatility. Appearance and style are increasingly significant for many applications, especially in sectors like architecture and consumer products. With an almost infinite variety in finishes, colors, and textures available through metal laminations, designers can craft visually striking surfaces that catch the eye while offering functionality.
For instance, consider high-end appliances or decorative panels in commercial spaces; metal laminates afford the flexibility to match different aesthetics—from industrial to ultra-modern—while maintaining resilience against wear and tear. The natural metallic sheen can elevate the perceived value of the product, transforming ordinary items into luxurious fittings that draw attention.
This versatility translates directly to customer satisfaction. When consumers see a product that is not only durable but also impeccably styled, it adds immeasurable value and sets products apart in competitive markets.
Cost-Efficiency
Let’s not beat around the bush—the financial aspect is a critical consideration for any engineering decision. Metal laminates offer enhanced cost-efficiency over time, which can significantly influence project budgets. While initial costs may fluctuate depending on the specific metals and processes used, the longevity and reduced maintenance needs of laminated products add value that becomes evident over the long haul.
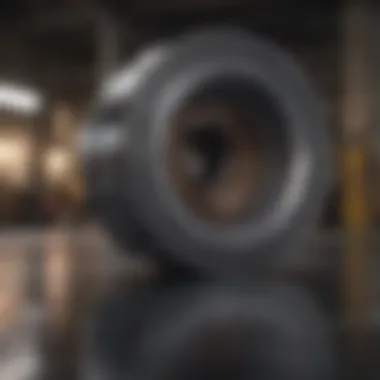
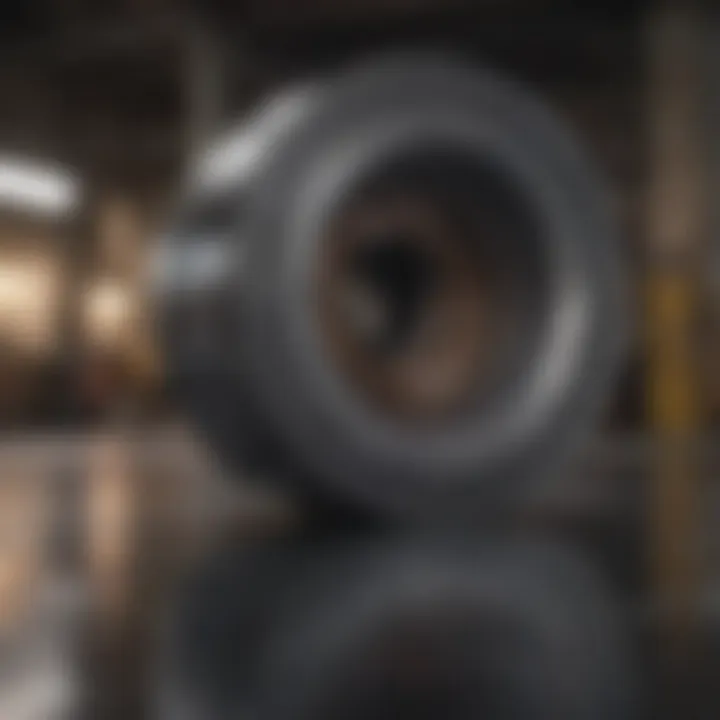
Moreover, because metal laminates often require less raw material due to their layered structure without compromising strength, manufacturing can become more streamlined. Manufacturers can achieve economical production runs with less waste, ultimately lowering material costs.
In essence, the cost-efficiency of metal laminates serves not just as a claim but a tangible boon, encouraging industries to favor metal laminates in designs that aim for both economy and high performance.
Challenges and Limitations
When discussing metal laminates, it’s crucial to not only highlight their advantages but also address the challenges and limitations they present. Understanding these factors is essential for professionals engaged in material science, engineering, and related fields. While metal laminates are celebrated for their versatility and utility across several industries, several hurdles must be navigated during manufacturing and application.
Manufacturing Challenges
The road to creating metal laminates is not always smooth. Manufacturers often grapple with a few persistent issues that can affect output and quality.
- Precision Defects: Achieving the exact tolerances required for metal laminates can be challenging. Misalignments during assembly can lead to defects that compromise the structural integrity of the final product.
- Adhesive Limitations: While different joining methods exist, adhesive bonding can have its pitfalls. Factors such as temperature fluctuations, humidity, and surface preparation drastically impact the effectiveness of adhesives, which may lead to delamination over time.
- Cost of Equipment: Specialized machinery capable of producing high-quality metal laminates can be prohibitively expensive, often deterring smaller firms from entering the market. This can result in less competition and innovation in an industry that could otherwise benefit from diverse approaches.
These obstacles necessitate an ongoing investment in technology and skills development. As manufacturers adapt to these challenges, innovations are likely to arise that not only address current limitations but also expand the potential applications of metal laminates.
Environmental Concerns
As environmental issues become more pressing, the practices surrounding the production and disposal of metal laminates come under scrutiny. Moving forward, it’s imperative for manufacturers and users to consider the ecological footprint associated with these materials.
- Resource Intensive Production: The fabrication of metal laminates often requires significant amounts of energy and raw materials. This can contribute to environmental degradation if not managed responsibly.
- Recycling Challenges: Once a metal laminate has reached the end of its lifecycle, recycling can pose complications. The layered nature of these materials may inhibit efficient recycling processes, leading to increased waste.
- Air Pollution: Processes involved in the production of metal laminates can emit pollutants, which have implications for air quality and overall community health.
"Adapting sustainable practices not only makes economic sense, it is fast becoming essential for compliance with regulations worldwide."
Manufacturers must take these concerns seriously, integrating greener practices into their workflow. Studies suggest that prioritizing sustainability can also foster innovation, creating new markets and opportunities within the sector.
Both manufacturing and environmental challenges present significant barriers, yet they also highlight the areas where the industry can grow and evolve. As we move forward, addressing these limitations will be key to harnessing the full potential of metal laminates in an ever-changing landscape.
Future Directions for Metal Laminates
The exploration into the future directions for metal laminates not only allows us to foresee the potential advancements in the field but also emphasizes the critical role these materials play in various industries. As technology progresses, the expectations for metal laminates are evolving, the implications reaching into realms like aerospace, automotive, and electronics. Various specific elements come into play when considering the direction of metal laminate technology, from innovations in material science to increased sustainability efforts.
Innovations in Material Science
The drive for innovation in material science is crucial. By pushing the boundaries of existing metal laminate technology, researchers are focusing on the development of hybrid composites. This involves combining metals with polymers or ceramics, leading to enhanced properties. For instance, a new aluminum-titanium laminate could offer significant strength while also being incredibly lightweight. The enhancements mean engineers can create structures that are lighter and require less energy to produce.
Furthermore, advanced manufacturing techniques such as additive manufacturing are reshaping how these materials are produced. These processes allow for the layering of materials to create unique structures that were previously impossible. Techniques like 3D printing are not just reducing waste but also enabling intricate designs that optimize performance while reducing weight. Innovations like these are becoming essential as industries look to meet performance standards while remaining cost-effective.
Sustainability Considerations
A significant consideration for the future of metal laminates is sustainability. The industries we serve are increasingly focused on reducing their carbon footprint, and metal laminates offer a pathway to achieve these goals. By using recycled metals in laminate production, manufacturers can contribute positively to environmental conservation. Besides, laminates often exhibit greater longevity compared to single-material solutions, reducing the frequency of replacements and thus waste.
Going further, industries are exploring how to incorporate bio-based adhesives and coatings that enhance the laminates' resistance to environmental factors. Such strides not only improve the lifespan of products but also reduce reliance on petrochemical resources.
"Future advances in metal laminates will certainly balance performance and sustainability, leading to innovations that will define the industry for years to come."
In nursing these directions, continual research is paramount. Validating the economic feasibility of next-gen materials and processes ensures broader adoption across various sectors. The subsequent developments will surely mark an era where metal laminates become not just materials of choice but also champions of environmental responsibility.
Epilogue
The exploration of metal laminates reveals the profound significance of these materials in various fields. From aerospace engineering to consumer electronics, the applications of metal laminates are both vast and transformative. Their ability to combine the strengths of multiple metals while minimizing weaknesses leads to innovative solutions that push the boundaries of design and functionality.
Summary of Key Points
- Definition and Composition: Metal laminates are composed of layers of different metals, creating a composite material that exhibits superior properties compared to individual metals. This composition not only optimizes performance but also allows for creative design solutions.
- Manufacturing Techniques: The processes involved in creating metal laminates, such as cold and hot lamination, are critical to achieving desired characteristics like strength and flexibility.
- Diverse Applications: Industries are leveraging metal laminates for their advantages in lightweight structures, thermal management, and aesthetic appeal, making them increasingly prevalent in modern engineering solutions.
- Benefits and Challenges: While metal laminates present solutions to many engineering problems, challenges—such as environmental impact during manufacturing and the need for specialized production techniques—remain significant.
The Importance of Continued Research
As technology advances, ongoing research into metal laminates is essential. Innovations in material science can lead to breakthroughs that further enhance their properties and applications. Moreover, understanding the environmental implications of metal laminate production paves the way for sustainable practices.
"Sustainability is not just a trend; it is a necessity that must be integrated into the fabric of material development. Metal laminates will be at the forefront of this shift."
Importance of References
The significance of references lies in several key elements:
- Credibility: References back up the data and claims made throughout the article. In the case of metal laminates, stating facts without sources could lead to misinformation. Including well-respected sources like academic journals, industry reports, and leading material science websites provides the necessary trustworthiness.
- Further Reading: For readers seeking to delve deeper, references serve as a roadmap. They guide students and professionals toward valuable materials, facilitating a richer understanding of complex concepts. For instance, linking to publications from the Journal of Materials Science extends knowledge beyond what's discussed here, sparking curiosity about advancements in the field.
- Historical Context: Understanding the evolution of metal laminates can be complex. Citing historical analyses and articles assists in building a timeline of innovations, challenges faced, and solutions found in the pursuit of optimizing metal laminates in various applications.
- Engagement with Experts: Citing credible experts in the field not only bolsters arguments but also connects readers to a community of professionals and researchers. Engaging with platforms like Reddit allows learners to ask questions and discuss nuances that aren’t covered deeply in articles, thereby enriching the discourse.
Benefits of Proper Citations
Utilizing references is not just about listing sources at the end. There’s an art in weaving citations throughout the article. When references are cited properly, here are some benefits:
- Supports Claims: Each statement or claim made can be traced back to reputable sources, affirming the writer's integrity.
- Enhances SEO: Well-cited articles often rank better on search engines, as they signal to algorithms that the content is well-researched.
- Fosters Learning: The inclusion of various types of references encourages readers to explore beyond the article, embracing lifelong learning.
Considerations About References
While it's clear that references are invaluable, there are several considerations to keep in mind:
- Relevance: The quality of sources matters much more than quantity. Citing outdated or irrelevant sources may mislead readers and diminish the impact of the article.
- Diversity: Including a mix of sources—academic, industry, and online discussions—provides a well-rounded perspective.
- Accessibility: Ensure that the references are easily accessible. Linking directly to online articles or databases can be beneficial for readers wanting instant information.
"References shouldn’t just be an afterthought; they are the backbone of a well-articulated argument."
Ultimately, the references section is an essential component of this article. It encapsulates the journey undertaken in exploring metal laminates and acknowledges the contributions of various scholars and practitioners who have advanced knowledge in the field. Properly handled, references become not only a tool for validation but also a bridge to further inquiry, fostering a culture of learning and curiosity among readers.