In-Depth Insights on Liquid Photoresist
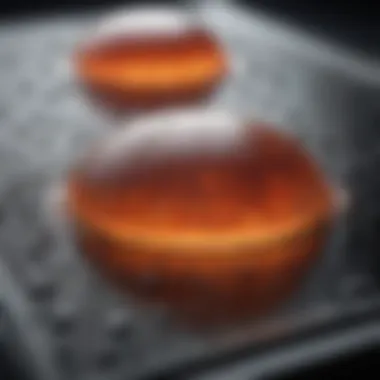
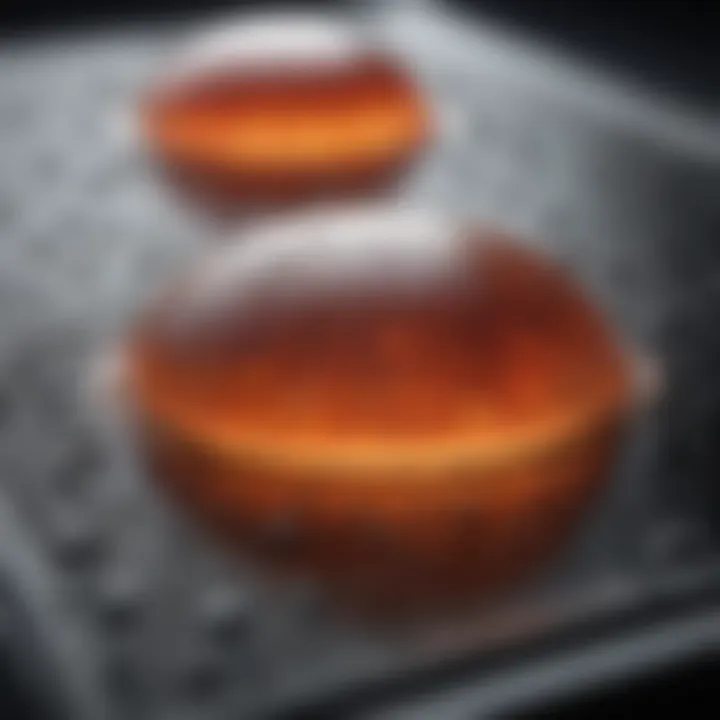
Intro
Liquid photoresist plays a vital role in the complex landscape of photolithography, especially within the semiconductor manufacturing sector. Understanding this material not only sheds light on its chemical properties but also emphasizes its pivotal functions during the microfabrication process. It’s intriguing how liquid photoresists have evolved, adapting to the relentless pace of technological advancements, and influencing various high-tech applications.
The burgeoning field of semiconductor technology increasingly relies on precise patterns and structures which are made possible through the use of liquid photoresist. This surprising liquid, containing a mixture of polymers and solvents, transforms into a hardened state when exposed to light, which is essential for creating intricate designs on semiconductor wafers.
Throughout this exploration, we will delve into the methodological aspects of liquid photoresist development, its applications, the inherent benefits, and the limitations that come along with its use. More importantly, we will cast an eye toward future innovations and research directions in this ever-evolving field.
Methodology
Study Design
To garner an in-depth understanding of liquid photoresist, a multifaceted approach is adopted. This involves reviewing scientific literature, analyzing case studies from industry practices, and evaluating advancements in the composition of photoresist materials. The study design also includes qualitative assessments of recent technological breakthroughs.
Data Collection Techniques
The collection techniques for this study predominantly stem from academic publications, patent databases, and industry reports. Interviews with experts working in semiconductor fabrication provide valuable insights not easily found in written sources, adding a practical dimension to our knowledge.
Furthermore, collaborative discussions on platforms like Reddit allow the aggregation of unique perspectives from practitioners who are actively engaged in processes that utilize liquid photoresist.
Discussion
Interpretation of Results
Examining the efficacy of liquid photoresists reveals several key insights. For one, their ability to create complex and minute features significantly contributes to the miniaturization of electronic components. Utilizing various formulations helps tailor the resist's sensitivity to light, allowing for more precise control over pattern resolution.
Limitations of the Study
However, as with any research, limitations do exist. One of the principal challenges faced by liquid photoresist is its sensitivity to environmental factors. Temperature and humidity can drastically alter the outcomes of the photolithographic process, potentially leading to inconsistent results. Additionally, not all formulations of liquid photoresist are suitable for every application, which means optimization is essential but complicated.
Future Research Directions
Looking ahead, there’s a strong impetus to explore new materials that might enhance the properties of liquid photoresist. Research into biodegradable forms and those with improved quantum efficiency could be groundbreaking, as the industry seeks to balance performance with environmental responsibilities. Furthermore, advancing computational techniques for simulation and modeling can significantly reduce trial and error in developing new formulations.
There is always room for improvement and growth when it comes to liquid photoresist. As the semiconductor industry pushes for higher performance and tighter integration, the demand for smarter photoresists will only grow.
Liquid photoresist, with its intricate balance of chemistry and technology, stands as a cornerstone in modern semiconductor innovation, paving the way for future discoveries.
Preamble to Liquid Photoresist
Liquid photoresist plays a pivotal role in the field of photolithography, acting as a critical material that influences the quality and precision of microfabrication processes. As technology evolves, the relevance of liquid photoresists in manufacturing complex microstructures becomes increasingly apparent. Understanding its intricacies allows researchers, students, and professionals to grasp the underlying chemical principles and operational nuances that define this essential material.
Definition and Purpose
Liquid photoresist is essentially a light-sensitive coating applied to a substrate, usually silicon. The defining characteristic of this material is its ability to undergo a chemical transformation when exposed to light, typically ultraviolet (UV), resulting in either a positive or negative alteration in its structure. In other words, after going through a suitable development process, a pattern is created on the substrate that mirrors the light exposure sequence. The purpose of this process is vital: it facilitates the etching or deposition of materials on semiconductor wafers, enabling the production of microelectronic components such as transistors, capacitors, and integrated circuits.
For some, the intricacies of liquid photoresist can seem daunting. However, a clear apprehension of its definition helps demystify the processes at hand. Users of liquid photoresist often need not only a broad knowledge of the basic chemical properties but also an understanding of the different formulations that can be applied to specific manufacturing requirements. This sets the stage for exploring the range of types available and how these affect outcomes in the microfabrication realm.
Importance in Microfabrication
The significance of liquid photoresist in microfabrication cannot be overstated. It serves as the backbone for achieving high-resolution patterning necessary for the miniaturization of electronic devices. To put it plainly, without liquid photoresist, we would not be able to attain the intricate designs present in modern electronics.
Some key considerations that highlight the importance of liquid photoresist include:
- Precision Fabrication: The ability to create intricate patterns allows for more densely packed components, thereby enhancing the performance of microchips.
- Adaptability: Liquid photoresists come in various formulations designed to meet the specific demands of different applications, from thin-film transistors in displays to microelectromechanical systems (MEMS).
- Efficiency: Utilizing liquid photoresist solutions in the manufacturing process can lead to significantly reduced cycle times and lower material waste.
"The microfabrication landscape is increasingly intertwined with advancements in liquid photoresist technologies, factoring into the pace of innovation in electronics."
With these points in mind, it’s clear that liquid photoresist is not merely a component in the process; it’s fundamental to achieving the miniaturization trend prevalent in today’s semiconductor technology, where the functionality of devices dramatically hinges on the precision of these processes. Understanding the role of liquid photoresist within microfabrication opens up doors to exploring its composition, phases of development, and the myriad of applications that stem from its use.
Chemical Composition and Properties
Understanding the chemical composition and properties of liquid photoresist is essential for anyone looking to grasp its pivotal role in photolithography and semiconductor manufacturing. The unique blend of ingredients not only affects the performance of the photoresist but also determines how it reacts during the various stages of the microfabrication process. This section dives into the core components, elucidating how the properties are intertwined with the performance and usability of liquid photoresist in advanced technology.
Basic Chemical Components
The makeup of liquid photoresist typically includes several key chemical components, each contributing to its overall functionality. Commonly, these mixtures contain polymers, solvents, and photoactive compounds. The polymers act as the backbone, providing structural integrity and the ability to form a uniform film when applied. For instance, poly(methyl methacrylate) is a frequently used polymer that can enhance the tunability of the resist's thickness and adhesion properties.
Solvents are just as crucial; they help to dissolve these polymers and adjust the viscosity of the photoresist. This is important because a proper viscosity ensures the even coating of substrates, ultimately leading to better resolution in the final pattern. Furthermore, the photoactive compounds are what make the resist sensitive to light. These chemicals undergo a chemical change upon exposure to specific wavelengths, enabling the selective removal of either the exposed or unexposed areas during the development stage.
"A well-balanced formulation can make the difference between a blurry image and a sharply defined microstructure."
Viscosity and Flow Characteristics
Viscosity, which dictates how well a liquid flows, is a critical property of photoresist that influences coating techniques. If the viscosity is too high, the resist may not spread evenly across the substrate, leading to defects in the final pattern. Conversely, if it’s too low, there could be an excessive pooling of the liquid, which complicates the uniformity and detail of the coated surfaces.
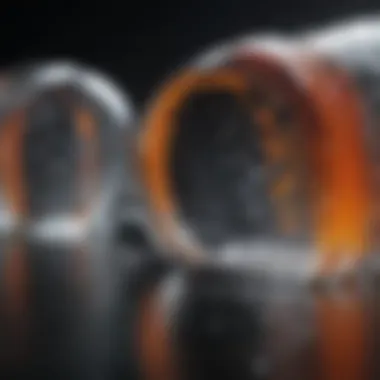
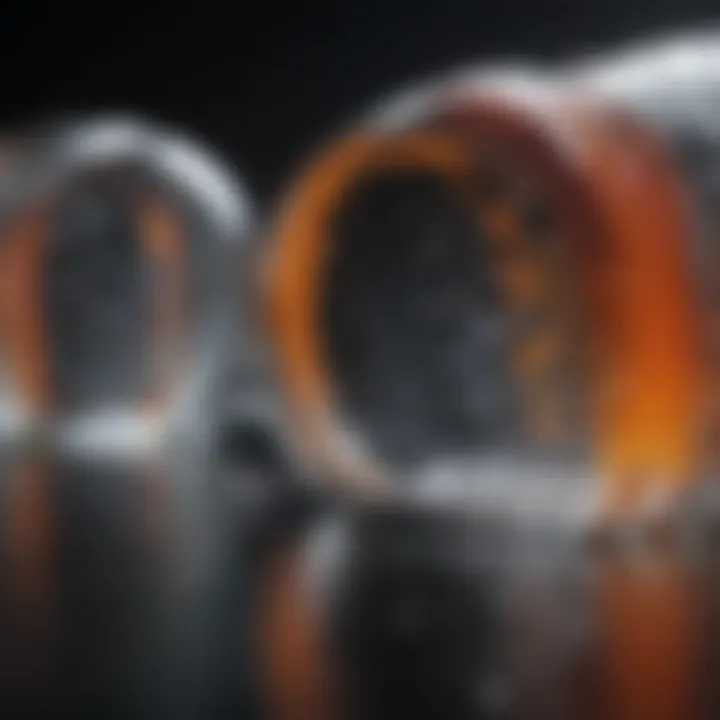
Here are some aspects intertwined with viscosity and flow:
- Temperature Dependency: The viscosity of photoresist can vary with temperature changes. It’s not uncommon for manufacturers to heat resist during the application process to achieve optimal flow characteristics.
- Shear Thinning: Many photoresists exhibit shear-thinning behavior, meaning they become less viscous when subjected to shear forces, such as those involved in spin coating. This property is advantageous because it promotes even layer thickness across different substrates.
- Material Interaction: How a photoresist interacts with the substrate also plays into its flow characteristics. For example, surfaces with higher energy may require a denser photoresist mixture to prevent beading or uneven spreading.
Response to Exposure
The reaction of liquid photoresist to exposure is a crucial aspect that ultimately dictates its effectiveness. Upon being exposed to light, the photoactive compounds within the resist undergo a transformation. With positive photoresists, the areas hit by light become soluble during the development process, while the unexposed areas remain intact. In contrast, negative photoresists harden when exposed, leaving the unexposed portions to be washed away.
Here are key parameters regarding exposure response:
- Sensitivity: This relates to how effectively a photoresist reacts to the amount of light exposure. A more sensitive photoresist can yield high-resolution patterns even with shorter exposure times, an essential factor in fast-paced manufacturing environments.
- Wavelength Compatibility: Different types of photoresists are designed to respond to various wavelengths of light, which impacts the selection based on the specific application. For instance, deep ultraviolet (DUV) light is often used in advanced semiconductor fabrication.
- Post-Exposure Bake: After exposure, a post-exposure bake process helps in the further polymerization of the resist, improving its etch resistance and overall definition in the final structure.
In summary, the chemical composition and its associated properties form the backbone of liquid photoresist functionality. Understanding these elements is not just an academic exercise; they are foundational to the practical applications in semiconductor fabrication and beyond.
Types of Liquid Photoresists
Liquid photoresists come in various formulations, each tailored to specific applications and requirements in photolithography. Understanding the types of liquid photoresists is crucial for researchers and engineers in the semiconductor manufacturing sector. It allows for better material selection based on performance characteristics, sensitivity to light, and the desired resolution for microfabrication tasks. The distinctions between these types also highlight how certain formulations cater to different technological advancements and process needs.
Positive Photoresists
Positive photoresists are known for their straightforward working principles. Upon exposure to light, these materials undergo a chemical change, resulting in the removal of the exposed areas during development. This feature is particularly essential in applications where intricate patterning is required, such as the production of integrated circuits. The design ease gained from using positive photoresists leads often to higher resolution patterns, making them the go-to choice in many scenarios.
The compositions of positive photoresists typically include:
- Novolac Resins: These provide the necessary structure for patterning and resistance.
- Photoactive Compounds: These components change chemically when exposed to light, facilitating pattern development.
- Solvents: They adjust the viscosity for optimal coating characteristics.
It’s crucial to note that the sensitivity of positive photoresists can vary widely, affecting the exposure conditions needed. High-sensitivity formulations can enable faster processing times, which is beneficial in high-throughput environments.
Negative Photoresists
In contrast to their positive counterparts, negative photoresists function on the principle of cross-linking upon exposure to UV light. When the material is exposed, the areas hit by light harden, creating a pattern where the unexposed areas can be washed away during the development process. This method can be beneficial in fabricating structures like MEMS devices, where a robust final product is essential.
The structure of negative photoresists usually comprises:
- Polymer Resins: These undergo cross-linking, resulting in a tougher, more resilient material.
- Sensitizers: These enhance the ability of the resist to respond to specific wavelengths of light.
- Additives: They improve the overall performance and optimize the resolution.
The dual advantages of durability and resolution can make negative photoresists an appealing choice for specific applications, especially in cases where environmental stability is vital.
Hybrid Formats
As the industry progresses, hybrid photoresists have emerged, incorporating the beneficial aspects of both positive and negative formulations. This innovative combination aims to tackle the limitations inherent in using a single photoresist type, providing versatility in application and enhancing fidelity in pattern reproduction.
Key characteristics of hybrid formats include:
- Enhanced Sensitivity: Combining components offers improved responsiveness to light.
- Adaptive Processing Conditions: They can be tuned to accommodate various lithographic processes, providing flexibility to engineers.
- Increased Resolution: By leveraging the best of both positive and negative resists, hybrids can achieve finer details and more complex structures.
Hybrid photoresists are particularly appealing in cutting-edge fields like nanotechnology. The ability to customize formulations allows for applications that demand extreme precision without sacrificing the convenience of liquid photoresists.
"Understanding the types of liquid photoresists is not just a matter of preference; it’s about meeting the technical demands of modern manufacturing processes."
At the end of the day, the choice of photoresist type can significantly impact the overall efficacy of the manufacturing process, determining everything from the resolution of circuits to the robustness of microelectromechanical systems.
In summary, whether adopting positive, negative, or hybrid formats, one must deeply evaluate the specific needs of the application. Each type contributes uniquely to the ever-evolving landscape of semiconductor technology.
Photolithography Process
Photolithography is a fundamental process in the world of microfabrication and semiconductor manufacturing. It is the technique utilized to transfer patterns onto substrates with exceptional precision. The liquid photoresist plays a critical role in this process, as it determines the ultimate resolution of the printed features.
The process begins with the application of liquid photoresist to the substrate. The quality of the coating, its uniformity, and, in turn, its subsequent exposure to light directly contribute to the efficacy of the photolithography process. Without this well-defined layer, achieving the desired detailed patterns becomes quite troublesome.
Coating Techniques
Coating techniques are key to achieving an even and consistent layer of liquid photoresist. Several methods are used, depending on the specific requirements of the application. Among these, spin coating is the most common approach, involving the rapid rotation of the substrate after the application of resin. This technique ensures that the photoresist is spread uniformly, thus forming a smooth and thin film. The thickness of the film can be controlled by adjusting the spin speed and time. Another noteworthy technique is the spray coating method, which can cover larger areas but is less commonly utilized due to its dependence on an even spray pattern and can result in uneven thickness.
When working with advanced materials, one might also explore slot-die coating or ink-jet techniques for specific applications, as these methods can provide enhanced precision and uniformity.
Exposure Methods
Once the substrate has been coated with photoresist, it is crucial to expose it to light. The exposure methods can vary significantly based on the requirements of the end product. Traditional processes employ ultraviolet (UV) light for exposure, allowing the photoresist to react according to its chemical formulation. This reaction essentially forms a latent image, where the regions that are exposed undergo changes in their solubility, allowing selective removal in the development stage.
Moreover, emerging technologies have introduced alternative light sources, such as extreme ultraviolet (EUV) and electron beams, that can provide higher resolution and more intricate patterns than conventional UV light. These innovative methods reflect the continual advancement and sophistication of photolithography technologies, pushing the limits of what can be achieved in microfabrication.
Development Process
The development process is where the exposed photoresist is sopped away. After exposure, the substrate is treated with a developer solution, which selectively removes either the exposed or unexposed areas, depending upon whether a positive or negative photoresist is used. This stage is crucial as it defines the final pattern on the substrate, resulting in a highly detailed mask that will guide further etching or deposition steps in the manufacturing process. As a result, any inconsistency or error at this stage can greatly affect the quality of the end product.
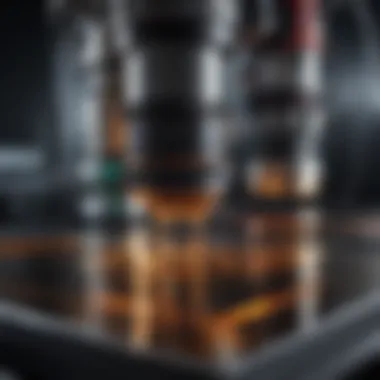
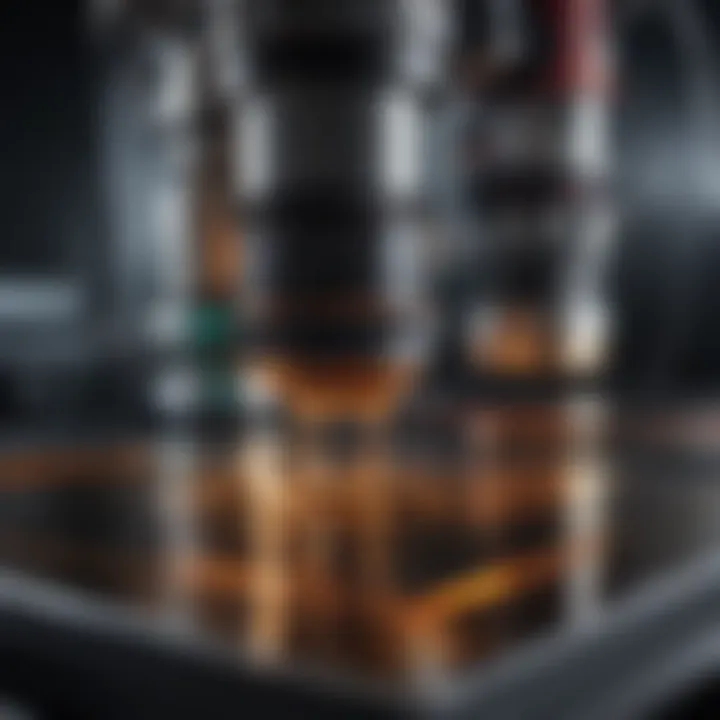
In summary, the photolithography process not only showcases the importance of liquid photoresist in microfabrication but also highlights the intricate relationship between various techniques used for coating, exposure, and development. A well-executed photolithography process can lead to higher yields and better performance in semiconductor devices and microsystems.
Applications in Semiconductor Manufacturing
In the intricate realm of semiconductor manufacturing, liquid photoresists are invaluable. They play a significant role in defining patterns on various substrates during the photolithography process. This section aims to delve deep into the prominent applications of liquid photoresists, underlining their impact on integrated circuits, MEMS fabrication, and advancements in nanotechnology.
Integrated Circuits
Integrated circuits (ICs) are the backbone of modern electronic devices. Liquid photoresists are crucial in creating the finely detailed patterns required for the tiny components within these circuits. The process often begins with a clean silicon wafer, which is coated with a layer of liquid photoresist. Upon exposure to light, the photoresist reacts, altering its solubility. This transformation allows for precise etching, crucial for producing functionalities like transistors and capacitors.
Benefits of Liquid Photoresists in ICs include:
- High resolution allowing for smaller feature sizes, which is essential as technology scales down.
- Fine control in etching ensuring that critical dimensions are adhered to, reducing variations in performance.
- Compatibility with other manufacturing processes such as chemical vapor deposition or ion implantation, making them versatile.
As technology and market demands evolve, the need for enhanced performance in ICs drives the development of novel liquid photoresist formulations.
MEMS Fabrication
Micro-electromechanical systems (MEMS) represent a fascinating intersection of mechanical and electrical engineering at very small scales. Liquid photoresists are particularly potent in this field due to their adaptability in processes designed to create intricate mechanical structures, such as sensors and actuators.
For MEMS, high aspect ratio features are often necessary, and liquid photoresists can be engineered to provide this. Furthermore, their sensitivity can be tuned to allow for various membrane structures or micro-machined devices.
Challenges and considerations in MEMS fabrication include:
- Material suitability: It’s vital to ensure the photoresist can withstand the operational environments of MEMS devices.
- Feature scalability: As applications in MEMS continue to advance, the ability to create ever smaller components becomes essential.
- Processing methods: The choice of coating and developing techniques can influence the final functionality and reliability of MEMS.
Nanotechnology Applications
As we venture into nanotechnology, the role of liquid photoresists becomes even more distinct. The ability to pattern at nanometer scales opens doors to revolutionary innovations in fields such as quantum computing, advanced sensors, and bioengineering.
Liquid photoresists facilitate the fabrication of nanoscale devices, which can lead to significant improvements in speed and efficiency.
Key aspects of liquid photoresists in nanotechnology include:
- Nanoscale resolution: The capability to achieve resolutions below 100 nm is critical for the development of next-generation semiconductor devices.
- Customization: Researchers can experiment with hybrid formulations that blend different types of photoresist to cater to specific nanofabrication needs.
To sum up, the adaptability and precision of liquid photoresists not only support current applications in semiconductor manufacturing but also pave the way for future innovations. Their role in ICs, MEMS, and nanotechnology is indispensable and will continue to evolve as new challenges and opportunities arise in the tech spectrum.
Advantages of Liquid Photoresists
Liquid photoresists offer a bouquet of advantages that make them indispensable in the field of photolithography. Their roles are not just a footnote in semiconductor manufacturing; rather, they are a mainstay that can significantly influence the quality and efficiency of processes. Let’s unpack the key benefits associated with utilizing these materials.
High Resolution and Sensitivity
One of the standout features of liquid photoresists is their high resolution and sensitivity. This capability is paramount in applications where precise patterning is critical, such as in the manufacture of integrated circuits. The resolution, or the ability to reproduce fine details, is boosted by the liquid's inherent properties. Once exposed to light, the chemical reactions in these resists can create remarkably fine features, well below the diffraction limit of the light used. Their sensitivity means that they can respond effectively to lower doses of radiation, saving both materials and time in the process.
Furthermore, advancements in formulations have contributed to even better resolution. The incorporation of nanometer-scale additives has pushed the envelope, allowing for structures that are densely packed and intricately detailed. This high sensitivity makes liquid photoresists an attractive choice, especially as technologies trend towards smaller, more complex designs.
Versatility in Applications
Another notable advantage of liquid photoresists is their versatility in applications. These materials are not limited to just semiconductor manufacturing. They find their way into various domains, including MEMS (Micro-Electro-Mechanical Systems), displays, and even biochips. The ability to tweak their chemical compositions allows manufacturers to tailor properties specific to the needs of different applications.
Consider, for instance, photoresists used in fabricating MEMS. These systems require specific mechanical characteristics and thermal stability, all of which can be engineered into liquid photoresists, thereby broadening the scope of their utility.
Moreover, as industries evolve, so too do the demands for new and innovative designs. This adaptability means that researchers and engineers can rely on liquid photoresists for pioneering projects, from solar cells to three-dimensional microstructures. Here’s a list highlighting the range of applications:
- Semiconductor devices
- Microfabrication of sensors
- Photonic devices
- Medical devices
Ease of Use in Processing
Lastly, liquid photoresists stand out for their ease of use in processing. The application of these materials can be less labor-intensive than their dry counterparts. Their flow characteristics allow for uniform coating, which is crucial for creating a consistent base layer necessary for precise lithography. Moreover, liquid photoresists can be easily dispensed using various techniques, such as spin coating or spray coating, making them user-friendly.
After exposure and while developing, the handling of liquid photoresists is usually straightforward. The development process can often be completed with simple solvents, streamlining steps in the manufacturing pipeline. As a result, designers and engineers spend less time fussing over application methodologies and more time focusing on achieving desired results.
"The flexibility, cohesiveness, and easy application of liquid photoresists inspire innovation in fields that demand cutting-edge solutions."
To summarize, liquid photoresists are not just a blip on the radar of semiconductor fabrication but are central to the industry's evolution. Their high resolution, versatility, and ease of use make them crucial for both current and future technological advancements.
Challenges in Liquid Photoresist Development
The development of liquid photoresist is no walk in the park. This crucial material is tightly intertwined with the technological fabric of modern semiconductor manufacturing, yet it faces several significant hurdles. Each challenge carries weight not just for researchers and manufacturers, but also for the sustainability and future of the technology itself.
Tackling these challenges is essential to push the boundaries of performance and ensure that liquid photoresists can meet ever-growing industry demands. Let’s dive into the key elements of the challenges faced in this area, with attention toward environmental, performance-related, and competitive issues that can hinder progress.
Environmental Concerns
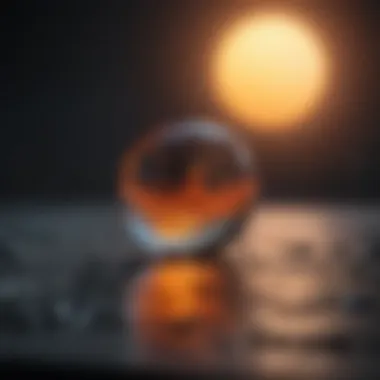
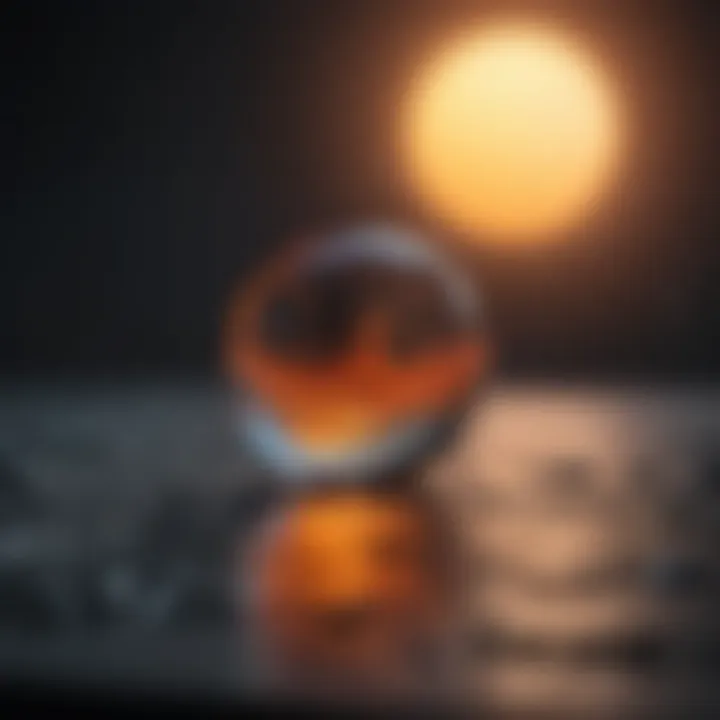
As the world takes a closer look at sustainability, liquid photoresist development cannot escape scrutiny. The environmental footprint of manufacturing processes is drawing significant attention. For instance, certain solvents used in photoresist formulations can be hazardous, posing risks during disposal and necessitating stringent regulatory compliance.
The following aspects emerge as noteworthy considerations:
- Solvent Emissions: The production and use of photoresists often emit volatile organic compounds (VOCs), which can contribute to air pollution and health risks.
- Resource Usage: Many formulations utilize non-renewable resources, creating a cycle that counteracts sustainability goals.
- Waste Management: Chemical waste management remains a precarious affair, with the disposal of unused or contaminated materials becoming critical for manufacturing facilities.
To combat these issues, R&D efforts are increasingly exploring greener alternatives, including bio-based solvents, which may change the landscape in liquid photoresist technology.
Performance Limitations
Even with cutting-edge innovations, liquid photoresists still have their limitations. The performance characteristics are paramount for applications in sub-micrometer feature size and high-resolution imaging. Some critical performance issues that must be addressed include:
- Resolution Limitations: High-density patterns in semiconductor manufacturing push photoresist materials to their limits. Ensuring sufficient resolution while maintaining contrast can be a tricky tightrope.
- Sensitivity: Some formulations may not respond adequately to the light exposure wavelengths used in modern lithography techniques. Their insensitivity can lead to under-exposure or over-exposure, compromising the fidelity of pattern transfer.
- Chemical Resistance: It’s essential that liquid photoresists hold up under various post-exposure treatments. Insufficient resistance to etching or developing solutions can lead to unwanted defect formation.
Finding a balance between these conflicting performance needs is critical for sustained innovation.
Market Competition
The competitive landscape in the photoresist market is as fierce as a hungry lion in the wild. Many players are vying for dominance, each one attempting to perfect their formulations to cater to advanced semiconductor needs. Market challenges include:
- Rapid Technological Advancements: As manufacturing techniques evolve, photoresist formulations must keep pace. Delays or shortcomings can lead to a loss of market share.
- Cost Considerations: Many companies face pressure to reduce costs without compromising quality. This financial balancing act can stifle innovation if not navigated wisely.
- Supplier Relationships: Relationships between manufacturers and suppliers play a crucial role. Shifts in supply chains, ingredient availability, or price fluctuations can present difficulties that are hard to predict.
"Innovation is not the product of logical thought, although the result is tied to logical structure."
— Albert Einstein
Future Directions in Photoresist Technology
As the semiconductor industry marches forward, the exploration of liquid photoresist technology continues to evolve at a rapid pace. The importance of advancing photoresist formulations, processing techniques, and sustainability initiatives cannot be overstated. Each of these elements plays a crucial role not only in enhancing the capabilities of microfabrication but also in addressing the mounting environmental pressures faced by this vital field.
Innovative Formulations
Innovative formulations are the backbone of future advancements in photoresist technology. Research is currently focused on developing new chemical compositions that can improve both performance and resolution. The key goal is to create photoresists that can operate effectively at smaller scales, ensuring that features on semiconductor devices can be produced with exceptional precision.
For instance, advancements in polymer chemistry have ushered in a new era of photoresists that respond smarter and faster to exposure. This means they can produce finer details and more complex structures, essential in integrated circuit manufacturing. There's also significant interest in improving the sensitivity of these materials to reduce exposure times while maintaining high resolution. This could significantly streamline production processes.
Moreover, various additives are being explored to tailor the optical performance and thermal stability of photoresists. A standout example includes the incorporation of nanoscale materials that enhance optical properties and offer self-assembling capabilities, providing a fresh approach to achieving greater precision.
Emerging Processing Techniques
With newer formulations come the need for emerging processing techniques. The photolithography landscape demands continuous innovation to keep pace with the evolving features of liquid photoresists. One promising technique is maskless lithography, which utilizes direct writing methods instead of traditional photomasks.
This process allows for instantaneous adjustments to the design, enabling rapid prototyping and iteration. As integrated circuits demand increasingly intricate designs, such adaptability in manufacturing is crucial.
Additionally, speed and precision in coating techniques, such as slot die and meniscus-guided coating, are gaining traction. These methods can apply photoresist more uniformly over large surfaces, which is vital for scaling up production in industries that rely on uniformity and minimizing defects.
Sustainability Initiatives
The push towards sustainability is no longer just an option; it's a necessity for the future of all manufacturing sectors, including photolithography. Industry leaders are increasingly prioritizing sustainability initiatives that focus on reducing waste and the environmental impact of chemical processes.
One approach involves the development of eco-friendly photoresists that utilize renewable resources or biodegradable materials. Research is underway to create formulations that can reduce hazardous waste, leading to safer disposal methods.
Additionally, there is a strong shift towards improving energy efficiency in the processing stages of liquid photoresist application. By optimizing the use of ultraviolet light sources and reducing heating requirements, the overall energy consumption can be decreased, aligning with global goals for carbon neutrality.
"Adopting battery-less, energy-efficient processing solutions not only mitigates environmental impact but also greatly reduces operational costs."
Furthermore, the industry is beginning to embrace the concept of a circular economy, wherein materials can be reused or refurbished, ultimately providing a more sustainable lifecycle for photoresist products.
By focusing on these innovative formulations, processing techniques, and sustainability initiatives, the future of photoresist technology looks not only promising but also considerably more responsible and tailored to the demands of tomorrow’s semiconductor industry.
Epilogue
The discussion around liquid photoresist culminates in understanding its pivotal role in the photolithography landscape. This article serves as a comprehensive guide, shedding light on not just the science behind liquid photoresist but also its implications across various technological fields. Here’s a closer look at its significance.
Recap of Key Points
To recap, liquid photoresist is a cornerstone in the microfabrication process, integral to designing circuits and structures at the micro and nanometer scales. The composition, characteristics, and types of liquid photoresists have been explored, illustrating their varied applications. We've seen:
- Chemical Composition: The role of specific compounds that comprise liquid photoresists and how these influence performance.
- Application Scope: A survey of how these materials are essential in semiconductor manufacturing, especially in ICs, MEMS, and nanotechnology.
- Advantages and Challenges: While high resolution and versatility stand out as benefits, environmental concerns and market dynamics pose substantial challenges.
- Future Research Directions: Emerging formulations and sustainability efforts are crucial for the continuation of advancements in this field.
Connecting these dots affirms the relevance of liquid photoresist in today's tech-driven world.
Implications for Future Research
As we forge ahead, the implications for future research are profound. Liquid photoresist technology is on the brink of evolution, poised to embrace:
- Innovative Formulations: Research into new chemical compositions that enhance performance and reduce environmental impact could lead to groundbreaking developments.
- Emerging Processing Techniques: Exploring alternative methods that may offer efficiency and enhanced precision in application.
- Sustainability Initiatives: Investigating eco-friendly materials and processes is not just a trend but a requisite, ensuring compliance with increasing regulatory demands.
The pathway for liquid photoresist is marked by both challenges and opportunities, paving the way for a more productive and sustainable future in microfabrication. By nurturing advancements in these areas, researchers and industry professionals can play pivotal roles in shaping the next wave of semiconductor technologies.
"In the world of technology, innovation is fueled by the relentless pursuit of knowledge and betterment."
Thus, the essence of liquid photoresist goes beyond its current applications; it signifies a journey of continuous learning and adaptation, vital for the technological advances of tomorrow.