An In-Depth Exploration of Jig Boring Techniques
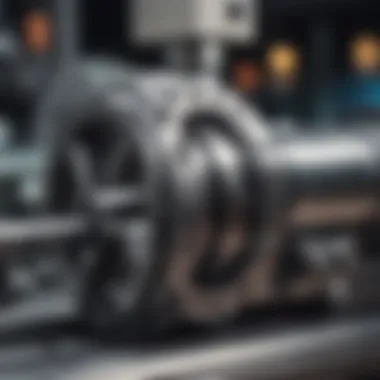
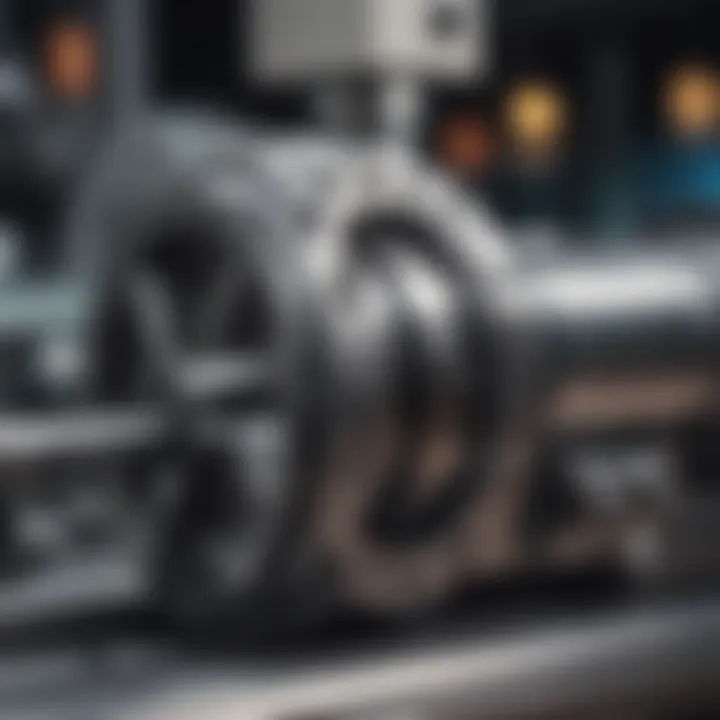
Intro
Jig boring is a vital process in precision machining that facilitates the creation of accurately positioned holes in various materials. Its significance cannot be overstated, especially in industries like aerospace, automotive, and manufacturing. By understanding jig boring, we unlock insights into tools and techniques that elevate manufacturing standards.
This article guides you through the principles and practices of jig boring. We will discuss its historical evolution, operational techniques, and applications across different sectors. Beginning with a methodological overview, the reader will gain a solid foundation regarding the technical components and performance expectations inherent in jig boring.
Methodology
Study Design
The exploration into jig boring techniques employs a qualitative approach, emphasizing practical insights drawn from academic literature, expert interviews, and historical analysis. This enables a comprehensive understanding of both traditional practices and contemporary advancements.
Data Collection Techniques
Data collection for this investigation includes:
- Review of academic papers and technical journals on jig boring.
- Interviews with industry professionals who specialize in precision machining.
- Analysis of existing machinery used in jig boring, focusing on advancements and innovations.
Engagement with these resources provides a layered perspective on methods and applications, enhancing the overall discussion.
Discussion
Interpretation of Results
The findings indicate that jig boring is characterized by precision and versatility. It is crucial for creating templates, molds, and dies. Moreover, the skill set required varies from basic understanding to advanced technical proficiency depending on the complexity of tasks.
Limitations of the Study
This analysis is limited by available resources and expert perspectives, which may not cover every aspect or application of jig boring. Some newer techniques may also be underrepresented, warranting further exploration.
Future Research Directions
Future research can focus on:
- The impact of automation and technology on jig boring.
- Comparative studies between traditional jig boring and emerging alternatives.
By exploring these avenues, we can better understand how jig boring will evolve and adapt in an increasingly technology-driven environment.
Jig boring serves as a pillar of precision machining, underpinning countless applications across diverse industries. Its continued relevance and technical sophistication make it a field worthy of detailed examination.
This article will expand on these elements systematically, offering insights tailored to students and professionals aiming to deepen their expertise in precision machining.
Defining Jig Boring
Jig boring is a critical process in precision machining. Understanding this topic is essential for anyone involved in manufacturing and engineering. Jig boring supports the creation of high-precision components. This process operates under specific machining principles. Its importance lies not only in its technical execution but also in the quality of the final product.
What is Jig Boring?
Jig boring refers to a type of machining geared towards producing accurate holes and features in a workpiece. Unlike conventional drilling, jig boring provides exceptional precision. A jig borer is designed to hold the jig, which guides the tool to achieve the desired accuracy. This method is commonly used when tight tolerances are necessary. It can involve creating holes, slots, or complex shapes, making it versatile for different applications.
Many industries find jig boring indispensable. It is prevalent in aerospace, automotive, and manufacturing sectors. The process relies on both mechanical fixtures and the advanced capabilities of jig boring machines. The results contribute significantly to the overall functionality of mechanical assemblies.
Key Characteristics of Jig Boring
Jig boring machines have distinctive features that set them apart from other machining tools. Here are some key characteristics:
- Precision: Jig boring is synonymous with high precision. It achieves tolerances that traditional drilling methods cannot.
- Flexibility: These machines can accommodate various jigs, allowing for a range of operations on different materials.
- Versatility: Jig boring can be adapted for various shapes and sizes, making it an essential tool for many applications.
In addition to these characteristics, jig boring machines typically include:

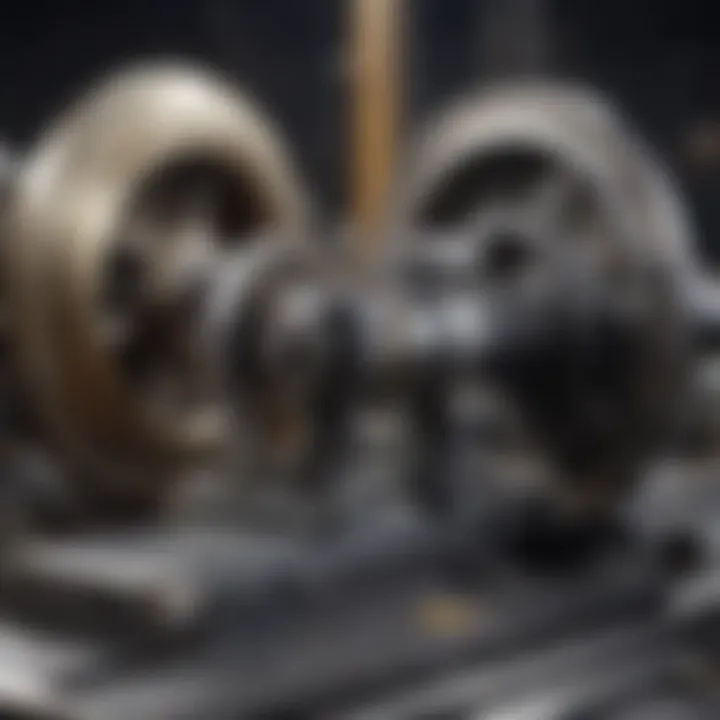
- Vertical Spindle Orientation: This design is crucial for accurate depth control.
- Manual and CNC Options: Many jig borer models offer both manual and computer numerical control, catering to different user needs.
"Jig boring's true strength lies in its ability to transform complex engineering requirements into precise outcomes."
Historical Context of Jig Boring
The historical context of jig boring is crucial for understanding its evolution and significance in precision machining. Since its inception, jig boring techniques have adapted through various industrial milestones. They provide insight into how manufacturing has transformed, reflecting advancements in technology and changing production demands.
The Emergence of Jig Boring Techniques
Jig boring techniques emerged in the early 20th century as a solution for producing precision holes in complex components. The need for accuracy in manufacturing grew with the rise of industries such as aerospace and automotive. Initially, traditional machining methods struggled to achieve the tolerances required for intricate parts.
The invention of the jig borer changed this narrative. This machine specialized in creating holes with unparalleled precision, allowing for the design of more complex geometries. As the aerospace sector flourished during and after World War II, the demand for precise machining grew exponentially. Jig boring techniques became essential in producing components like engine parts and airframes. The evolution of this technique reflects not only advancements in machine technology but also the increasing need for reliability and performance in engineered products.
Historical Innovations in Machining
Throughout history, several key innovations have influenced the development of jig boring. One significant milestone was the introduction of numerically controlled machines, which allowed for automated and repeatable machining processes. This innovation increased efficiency and precision, making jig boring more accessible for larger production runs.
Another notable advancement was the integration of computer-aided design (CAD) into the jig boring process. CAD software allows engineers to design parts with complex geometric shapes and geometrically define hole placements accurately. The combination of CAD and jig boring machines has enabled the production of parts that were previously considered unattainable.
The history of jig boring, marked by its emergence and the various innovations in machining, illustrates a progression toward greater precision and efficiency. As manufacturing continues to evolve, the principles and techniques of jig boring remain relevant, adapting to new technologies and methodologies with each passing era.
"The evolution of jig boring not only reflects the technical prowess of engineers but also the demands of an ever-expanding industrial landscape."
Principles of Jig Boring
The principles of jig boring are fundamental to comprehending the precision and efficiency that define this specialized machining process. Understanding these principles allows professionals and enthusiasts alike to grasp how jig boring fits into the broader field of precision engineering. This section discusses basic mechanisms and accuracy factors that underpin jig boring techniques.
Basic Mechanisms of Jig Boring
Jig boring machines utilize a series of mechanisms that enhance their precision. At its core, jig boring involves a specifically designed tool that allows for accurate hole placement and depth control. This accuracy is primarily achieved through the use of a jig—a device that holds the workpiece in a fixed position and guides the tool during operations. The tool is typically mounted on a spindle that operates in a linear motion along multiple axes.
Key components of jig boring machinery include the table, which holds the workpiece, and various adjustments that enable fine-tuning of the vertical and horizontal positioning. The use of a rotary table often complements these machines, facilitating the processing of complex geometries and multiple features without repositioning the workpiece.
Subdivision of these mechanisms into finer processes enhances the overall productivity. For instance, the incorporation of hydraulic systems aids in maintaining constant pressure during operations.
Accuracy Factors in Jig Boring
Accuracy is a defining characteristic of jig boring, which sets it apart from other machining methods. Multiple factors play a crucial role in achieving high precision levels. These factors include:
- Machine Calibration: Frequent calibration of the jig boring machine ensures that all components function within optimal parameters. This reduces the likelihood of errors during operations.
- Tool Quality: The quality and sharpness of the cutting tool significantly impact the machining accuracy. Dull or worn tools can lead to deviation in the dimensions of the holes.
- Material Stability: The material being machined should possess adequate stability. Variations in material properties can cause distortion, leading to inaccuracies. Metals like steel and aluminum are commonly used due to their reliable characteristics.
- Environmental Conditions: External factors such as temperature and humidity should be monitored, as they may affect material behavior and machine performance.
The precision achieved through jig boring is vital for industries requiring tightly controlled tolerances, such as aerospace and automotive manufacturing.
Overall, the principles guiding jig boring execute an essential role in maintaining high levels of accuracy and control. Each aspect is intricately linked, ensuring the process meets the demands for precision in modern manufacturing.
Jig Boring Machinery
Jig boring machinery plays a crucial role in the jig boring process, which is recognized for its accuracy and precision in creating complex parts. These machines are designed specifically to handle the intricacies involved in machining, providing the required tolerances that standard machining methods often cannot achieve. The significance of discussing jig boring machinery lies in its various components and types, which are tailored to meet the different machining requirements across industries.
The machines themselves are built to handle precision tasks, minimizing errors and ensuring consistency. This capability makes them essential in sectors such as aerospace, automotive, and medical device manufacturing, where precision is not just a preference but a necessity. Additionally, understanding the machinery helps professionals select the right equipment for specific projects, enhancing operational effectiveness in their respective fields.
Components of Jig Boring Machines
Jig boring machines comprise several components that work together to achieve high precision. The key components include:
- Base: The foundation of the machine, providing stability.
- Column: This vertical structure houses the spindle drive mechanism.
- Table: The surface on which the workpiece is mounted, often adjustable for height and angle.
- Spindle: The rotating component that holds the cutting tools and provides power for machining.
- Feed Mechanism: Allows controlled movement of the workpiece or spindle, which is critical for achieving precise depths and locations.
- Coolant System: Aids in the cooling of tools and workpieces, which helps in maintaining accuracy over long machining times and reduces wear on tools.
Each of these parts must work seamlessly together, so any malfunction can lead to significant errors in production. The continued advancements in the technology of these components have allowed for even higher levels of precision and productivity in jig boring.
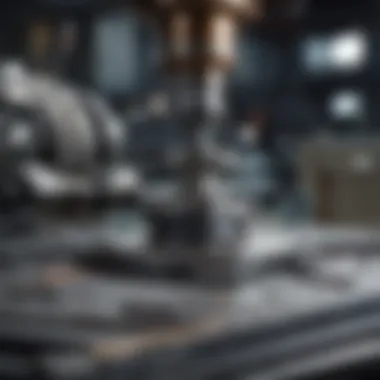
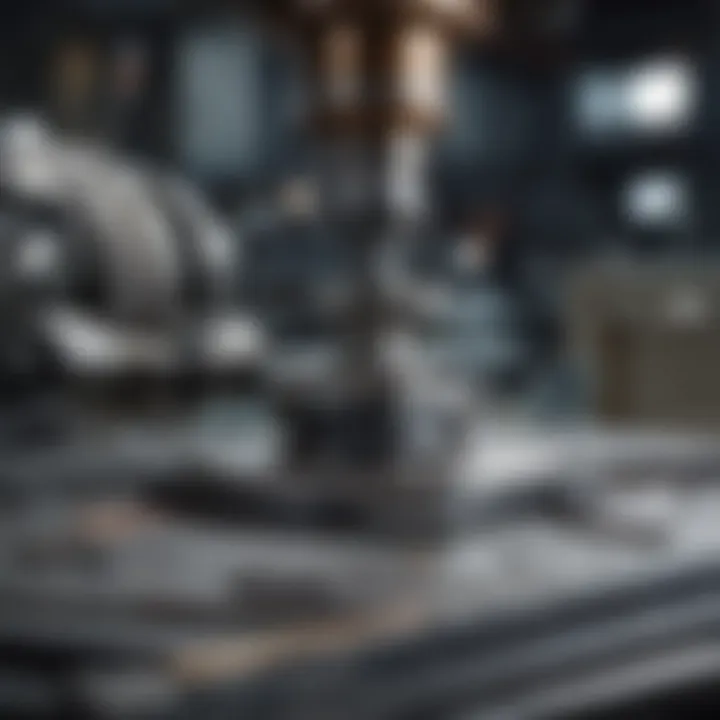
Popular Types of Jig Boring Equipment
There are several types of jig boring equipment, each designed for specific tasks and levels of precision. Notable ones include:
- Universal Jig Borer: Known for its flexibility, it can be used for various types of work and adjustments. Ideal for shops with a wide range of tasks.
- Vertical Jig Borer: Primarily used for vertical operations, it is efficient for creating accurate holes in flat surfaces.
- Horizontal Jig Borer: Suited for larger workpieces, this type offers enhanced stability for machining longer components.
- CNC Jig Borer: Incorporates computer numerical control (CNC) technology, allowing for automation and increased precision in complex operations.
Selecting the appropriate jig boring equipment depends on the specific machining requirements, including the type of material and the desired precision level. Understanding these options provides valuable insights for professionals in the machining industry.
"Precision is not just an art; it is a necessity in machining—especially in jig boring processes where even minute errors can lead to substantial setbacks in production."
By examining these components and equipment, one gains a greater appreciation for the intricate design and functionality that defines jig boring machinery. This understanding serves as a foundation for applying these techniques effectively in various manufacturing scenarios.
Materials Used in Jig Boring
The selection of materials in jig boring is critical to achieving the desired precision and durability in machining. These materials not only dictate the performance of the boring process but also affect the longevity and reliability of the finished components. Understanding which materials are commonly used and their intrinsic properties can guide decisions in manufacturing and engineering applications.
Common Materials for Jig Boring
Jig boring machines work with a variety of materials, each chosen based on the specific requirements of the project. Some of the most common materials include:
- Steel: Its strength and ease of machining make steel a preferred choice for many precision applications. High-strength steel alloys deliver improved durability.
- Aluminum: This lightweight material is ideal for projects requiring lower density. Aluminum offers good machinability and corrosion resistance, making it popular for precision components.
- Bronze: Ideal for applications needing wear resistance and low friction. Bronze is often used in the production of bushings and bearings due to its mechanical properties.
- Plastics: Various thermoplastics are sometimes used in jig boring to create lighter parts that need to be resistant to corrosion. They are beneficial in reducing material costs while ensuring ease in machining.
- Cast Iron: Known for its vibration-damping qualities, cast iron is frequently used in the production of machine frames and supports, contributing to stability during the machining process.
Selecting the right material is fundamental in optimizing performance and ensures that the components produced will meet their intended specifications.
Material Properties Impacting Machining
The properties of materials used in jig boring significantly impact the machining outcomes. Key properties to consider include:
- Hardness: This property impacts the wear resistance of tools and the overall tool life. Harder materials can lead to increased tool wear, requiring careful consideration of tool selection.
- Machinability: Materials with higher machinability ratings allow for quicker processing times. Steel, for example, offers good machinability compared to some alloys, affecting production efficiency.
- Thermal Conductivity: This property influences heat dissipation during machining. Materials like aluminum dissipate heat quickly, reducing the risk of thermal deformation in precision applications.
- Tensile Strength: High tensile strength materials are essential for parts that endure significant stress. Materials must handle the forces applied during the boring process without deforming.
Understanding these material properties aids machinists in choosing the best tools and methods for manufacturing, preserving quality throughout the jig boring process.
Applications of Jig Boring
Jig boring plays a vital role in precision machining and is immensely important across various fields. This machining technique is specifically designed to create accurately placed holes within components, hence it finds its applications primarily in industries that demand high levels of precision. Understanding the applications of jig boring sheds light on its significance in modern production processes.
The precise nature of jig boring allows it to be utilized for creating components that require intricate details. It is critical in fields such as aerospace, automotive, and medical device manufacturing. The ability to achieve tight tolerances is essential in these industries where even a minute error can lead to catastrophic failures or safety hazards.
Moreover, this technique is not just about drilling holes. Jig boring can also enhance the overall quality of finished products by ensuring that parts fit together seamlessly. This ability to maintain quality control is apparent in the production of complex assemblies where multiple components are involved.
Key benfits of jig boring include:
- Increased accuracy: Jig boring addresses the need for high tolerances in manufacturing settings.
- Versatile applications: From creating molds to producing parts used in sensitive electronics, jig boring offers a wide range of functional uses.
- Cost-effectiveness: By reducing the need for rework due to errors, jig boring contributes to overall efficiency and cost savings in production.
Jig boring is, therefore, not just a method of machining, but it is an integral part of a larger context in manufacturing. It is essential for industries aiming to maintain a competitive edge through high precision and quality standards.
Industries Utilizing Jig Boring
The industries that benefit from jig boring techniques are numerous and diverse. Each sector has specific demands that only jig boring can fulfill.
- Aerospace: In this sector, maintaining tight tolerances is critical due to safety requirements. Components like brackets and housings that require precision are often produced using jig boring.
- Automotive: Parts such as engine blocks and transmission components often rely on jig boring for precise machining, ensuring they fit accurately in the assembly process.
- Medical Devices: The production of implants and surgical instruments demands the highest levels of accuracy, making jig boring indispensable in the manufacturing process.
- Electronics: The production of circuit boards and housing components for various electronic devices involves precision machining techniques like jig boring, which ensures reliability and functionality.
These industries are just a few examples that illustrate jig boring's reach and effectiveness. The precision it offers meets the rigorous standards required to ensure safety and performance.
Precision Components and Jig Boring
Jig boring finds its home in creating precision components, which are fundamental in many engineering applications. The effectiveness of this technique lies in its ability to produce parts that require exact specifications, often well below a 0.001-inch tolerance.
In industries where performance is paramount, such as aerospace engineering, manufacturing precision components is non-negotiable. Components created through jig boring often include:
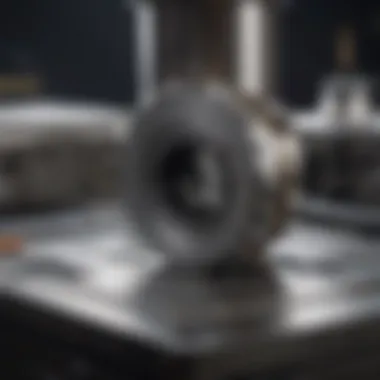
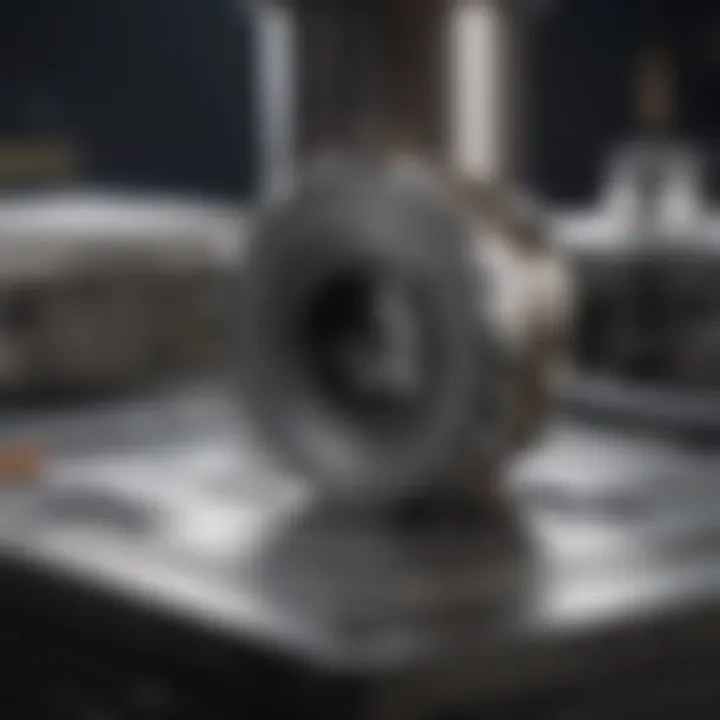
- Holes for fastening systems, where alignment is critical to operational integrity.
- Mold cavities that require exact dimensions to ensure proper product formation.
- Geometric profiles that facilitate components’ fit within larger assemblies.
By adhering to strict engineering standards, jig boring enhances the reliability and functionality of final products. Therefore, understanding the link between precision components and jig boring techniques is essential for engineers and designers focusing on high-performance applications.
Using jig boring enables industries to push the boundaries of what is possible, meeting the ever-growing demand for quality and precision in manufacturing.
"Jig boring is not merely a machining method; it is a cornerstone of precision engineering that serves to elevate the standards across multiple industries."
Through a comprehensive understanding of these applications, one can better appreciate the role of jig boring in the framework of modern manufacturing.
Skills and Competencies in Jig Boring
The domain of jig boring demands a specific set of skills and competencies that are crucial for precision machining. This section emphasizes the blend of technical knowledge, practical abilities, and problem-solving skills that professionals must harness to succeed in this field. With jig boring being a process central to creating high-precision components, the importance of these skills in maintaining quality and efficiency cannot be overstated.
Technical Expertise Required
To effectively engage in jig boring, individuals must possess a solid foundation in machining principles. This involves understanding the mechanics behind jig boring machines and how to operate them proficiently. Key areas of expertise include:
- Machine Operation: Familiarity with jig boring machines such as the Moore jig borer is essential. Technicians must know how to adjust settings for depth, feed rate, and tool selection.
- Dimensional Tolerance: Knowledge of tolerance levels is vital. Professionals need to understand how to achieve the required precision within specified limits. This includes using measuring tools accurately.
- Material Properties: Each material behaves differently under machining. Expertise in selecting and managing these materials enhances the overall outcome of the jig boring process.
Without a solid grasp of these elements, one risks compromising the quality of the output.
Training and Certification in Jig Boring
Training and certification are critical components for those looking to specialize in jig boring. Formal education helps ensure technicians are well-prepared to meet industry standards. Relevant aspects of training include:
- Vocational Education Programs: Many educational institutions offer programs focused on precision machining. Enroll in courses that specifically cover jig boring techniques to gain practical and theoretical knowledge.
- Hands-On Experience: Practical training is just as crucial. Internships or apprenticeships provide valuable exposure to real-world scenarios. This experience fosters confidence in machine operation and troubleshooting.
- Certification Bodies: Programs offered by organizations such as the National Institute for Metalworking Skills (NIMS) provide recognized certification. Achieving this certification can increase employability and enhance professional credibility.
Challenges in Jig Boring
Jig boring presents numerous challenges that can affect accuracy, efficiency, and overall project outcomes. Understanding these challenges is essential for anyone heavily invested in machining activities. This section outlines the most common obstacles faced during jig boring and suggests strategies to overcome them. Organizations that effectively address these issues can achieve higher productivity and improved quality in their machining processes.
Common Operational Challenges
- Alignment Issues: Maintaining the correct alignment during the jig boring process is vital. Misalignments can lead to dimensional inaccuracies, resulting in parts that do not meet specifications. This is particularly important in industries where precision is non-negotiable.
- Tool Wear: Tool wear is a common issue that affects machining operations. As tools wear, their effectiveness diminishes, which can lead to inconsistent results. Regular monitoring of tool conditions is necessary to ensure optimal performance.
- Material Variability: Different materials have varying properties, which can affect the jig boring process. Variations in hardness or density can complicate machining operations and lead to unexpected outcomes. Understanding material characteristics is critical for effective jig boring.
- Machine Limitations: Jig boring machines have their limitations, whether they are related to speed, power, or technology. Familiarity with machine capabilities can help operators optimize performance and avoid potential pitfalls.
Mitigation Strategies for Jig Boring Issues
To address the challenges identified, several strategies can be employed:
- Regular Maintenance: Conducting regular maintenance on jig boring equipment ensures machines operate at peak efficiency. This includes checking components for wear, adjusting calibrations, and replacing worn parts promptly.
- Thorough Training: Comprehensive training for operators reduces the risk of error during operations. Skilled operators are more likely to recognize early signs of misalignment and can make adjustments proactively.
- Implementing Quality Control: Instituting quality control measures, such as inspections throughout the process, can catch mistakes before they become serious issues. This can include measuring components at various stages of production.
- Material Selection: Choosing the right materials for specific applications can help minimize variability and inconsistencies. Understanding the interaction between the chosen material and the jig boring process is critical for success.
"Addressing operational challenges in jig boring enables manufacturers to enhance precision and efficiency, creating a competitive advantage."
By proactively managing these concerns, operations can significantly enhance the effectiveness and reliability of jig boring processes.
Future of Jig Boring
The future of jig boring is a topic of paramount significance within the sphere of precision machining. As industries continue to demand higher accuracy and efficiency, the techniques and technologies associated with jig boring must adapt. With a focus on specific elements such as technological advancements and evolving practices, the future landscape of jig boring will undoubtedly impact manufacturing processes on multiple levels. Understanding these trends is crucial for professionals, students, and educators alike.
Technological Advancements in Jig Boring
Technological advancements are reshaping the jig boring landscape significantly. Computer Numerical Control (CNC) technology, for instance, is streamlining the boring process. CNC jig borers enhance precision and repeatability in manufacturing, allowing for more complex designs to be executed without sacrificing performance.
Key advancements include:
- Automation of Processes: Automation improves operational efficiency, minimizes human error, and can lead to cost savings in production.
- Integration of CAD/CAM Systems: These systems facilitate better planning and design, enabling operators to simulate the jig boring process before actual machining starts.
- Enhanced Materials: New materials are being developed that enhance the machine's resistance to wear and temperature fluctuations, thus prolonging equipment life and ensuring consistent performance.
The adoption of these technologies can yield significant productivity boosts and lower production costs. Incorporating advancements like predictive maintenance through IoT (Internet of Things) also plays a key role in maximizing the potential of jig boring.
Predictions for Jig Boring Practices
Looking ahead, predictions for jig boring practices suggest a shift towards even more sophisticated techniques. As industries demand greater efficiency, manufacturers are likely to invest heavily in training and upgrading machinery.
Forthcoming trends may include:
- Increased Emphasis on Training: Operators will need to adapt to complex machinery and advancements in technology. Proper training will ensure they keep pace with the evolving demands of precision machining.
- Sustainability Considerations: As environmental consciousness grows, jig boring practices may evolve to focus on eco-friendly materials and processes that minimize waste and energy consumption.
- Continued Innovation in Software: Software developments will likely drive improvements in precision and speed of jig boring operations, integrating machine learning to optimize processes further.