Digital Accelerometers: Function, Applications & Future
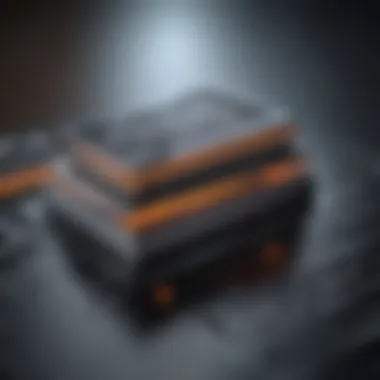
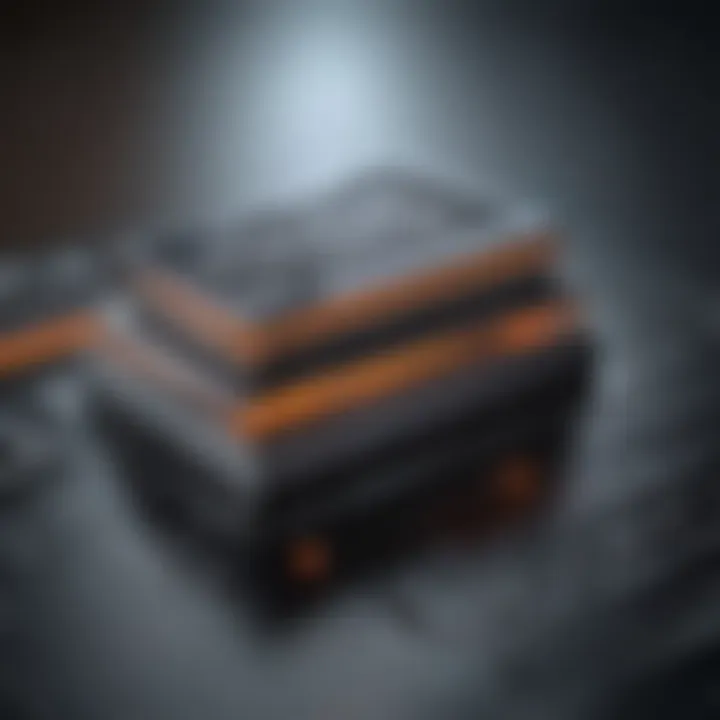
Intro
Digital accelerometers are integral to multiple technological advancements today. Their primary function is to measure acceleration forces and changes in motion. This capability has allowed various industries to enhance their products by incorporating precise motion detection features. The applications are vast, spanning consumer electronics like smartphones to critical systems in automotive and aerospace fields. Through this detailed exploration, we will break down their construction, types, and operational principles.
Understanding digital accelerometers requires not only recognizing their physical components but also grasping the mechanisms that allow them to produce accurate data. These devices play a crucial role in vehicle navigation and the functionality of mobile devices. Thus, developing a more profound comprehension of their operation can significantly benefit students, educators, researchers, and professionals alike.
Next, we will discuss the methodology employed in studying these devices, focusing on their design and data collection techniques used in the industry.
Prelims to Digital Accelerometers
Digital accelerometers are critical devices that measure changes in velocity and are widely used across various fields including consumer electronics, automotive, and aerospace industries. Their ability to provide precise data on acceleration forces is vital for enhancing performance and safety in technology.
Digital accelerometers leverage solid-state technology, which means they are not only compact but also efficient in processing data. The importance of understanding digital accelerometers lies in their application range and the fundamental role they play in numerous systems. For professionals and enthusiasts alike, grasping the basics of how these instruments function can lead to better implementation and innovation in projects.
Definition
A digital accelerometer is an electronic device that measures the rate of change of velocity of an object. It senses linear acceleration along one or several axes and converts this measurement into a digital signal. The data from these sensors can then be utilized in various applications ranging from motion detection to stabilization of vehicles and smartphones.
Historical Context
The development of accelerometers dates back to the mid-20th century when analog versions were primarily in use. Originally, mechanical systems were relied upon, which tended to be bulky and less accurate. With the advancement of technology in the late 20th century, microelectromechanical systems (MEMS) emerged. These miniature devices allowed for the integration of accelerometers into common electronics, dramatically increasing their prevalence and versatility.
The shift to digital technology brought improved accuracy, reduced noise, and enhanced power efficiency. As a result, applications of digital accelerometers expanded rapidly, enabling innovations in various fields. Today, they are an integral part of safety features in automobiles, provide data in mobile devices, and are essential in aerospace for monitoring flight dynamics.
The Science Behind Acceleration
The science behind acceleration is central to understanding how digital accelerometers function. It dives into the fundamental principles that govern motion and how these principles are translated into measurable data. Each of the concepts outlined here plays a crucial role in helping scientists and engineers design better accelerometers, ensuring they provide accurate readings in various applications.
Basic Concepts of Acceleration
Acceleration refers to the rate of change of velocity of an object. In simple terms, it describes how quickly something speeds up or slows down over time. This can be measured in units such as meters per second squared (m/sΒ²). Understanding these concepts is essential for the proper application of digital accelerometers, as they are designed to detect these changes and convert them into electrical signals.
Key characteristics of acceleration include:
- Magnitude: This is the strength of the acceleration. A higher magnitude indicates a more significant force acting on an object.
- Direction: Acceleration is vectorial, meaning it has a direction as well as a magnitude. Direction is significant, especially in applications needing precise positional information.
- Types of Acceleration: Acceleration can be classified into different types, such as uniform, non-uniform, linear, and angular. This classification helps in distinguishing various motion characteristics that accelerometers may detect.
Understanding these basic elements allows for improved application of digital accelerometers in both industrial and consumer products. The principles of acceleration are not just theoretical; they influence practical design and usage in various systems.
Forces and Motion
The interaction of forces is vital to the study of acceleration. Newton's laws of motion serve as the foundation for this relationship. The first law states that an object at rest will remain at rest unless acted upon by an external force. This means that digital accelerometers must account for external influences when measuring motion.
The second law explains how a net force acting on an object results in acceleration proportional to the mass of the object. This relationship can be defined by the equation:
F = m*a
where F is the force, m is the mass, and a is the acceleration.
Understanding this interaction is critical for the design of accelerometers, which have to discern between various forces acting on an object and convert that information accurately into measurable data.
Factors influencing forces and motion include:
- Mass of the Object: Heavier objects require more force to accelerate, affecting the readings of digital accelerometers.
- Friction: This resistance affects how an object moves. It can lead to inaccuracies if not calibrated properly.
- External Influences: Environmental factors, such as vibrations or impacts, can also impact the motion being measured.
In summary, the concepts of acceleration and the forces acting upon objects provide the necessary framework for understanding how digital accelerometers function. By applying these scientific principles, designers and engineers can enhance the performance and accuracy of accelerometer technology.
Types of Digital Accelerometers
Understanding the various types of digital accelerometers is crucial for their effective application in various fields. Each type has its own strengths, weaknesses, and unique construction that make them suitable for specific tasks. Recognizing these characteristics can aid in selecting the appropriate device for a given application. This section will explore four main types of digital accelerometers: Microelectromechanical Systems (MEMS), capacitive accelerometers, piezoelectric accelerometers, and optical accelerometers.
Microelectromechanical Systems (MEMS)
Microelectromechanical Systems, or MEMS, are small devices made using microfabrication technology. They are widely used in consumer electronics due to their compact size and low power consumption. MEMS accelerometers typically consist of a mass suspended by springs. When the device experiences acceleration, the mass moves relative to the frame, causing a change in capacitance or other signal that is converted into an acceleration measurement.
These accelerometers are appreciated for their high sensitivity and ability to be produced in bulk. However, they can be sensitive to temperature and other external conditions. Thus, calibration is critical to ensure accuracy. MEMS technology represents a significant trend in modern acceleration measurement, making these accelerometers invaluable across industries such as smartphones, gaming systems, and health monitoring devices.
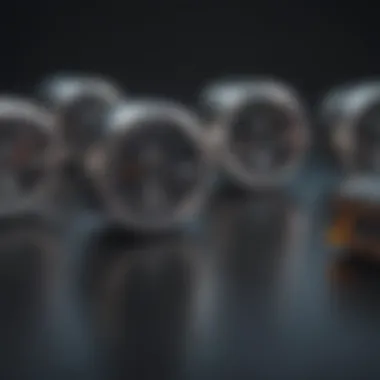
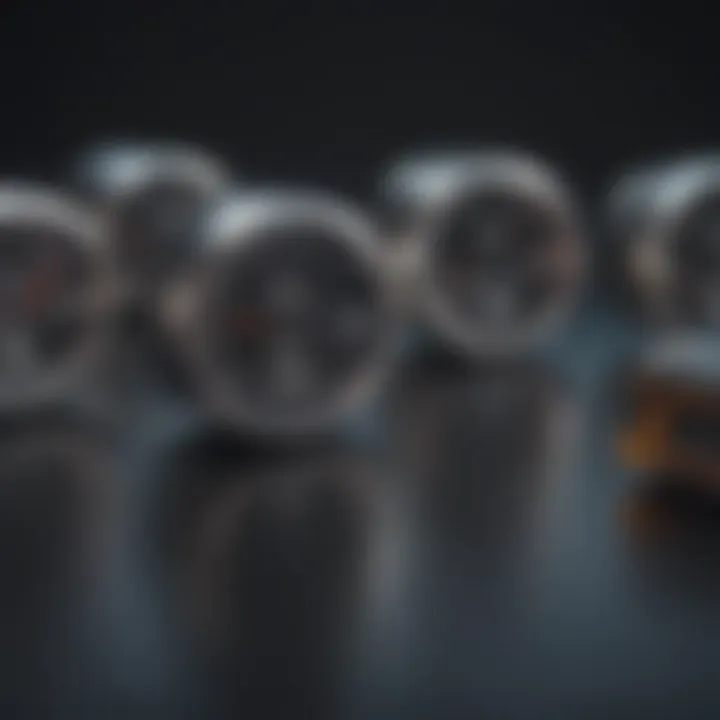
Capacitive Accelerometers
Capacitive accelerometers utilize capacitive sensing to measure acceleration. They operate by detecting changes in capacitance resulting from the acceleration acting on a mass. This type of accelerometer is known for its ability to achieve high levels of sensitivity and resolution, making them ideal for precision applications.
Capacitive accelerometers tend to have a wide frequency response, allowing for the detection of rapid accelerations. However, they are more complex to design compared to MEMS accelerometers and can be more expensive. Their precise measurements are often leveraged in scientific research, industrial machinery monitoring, and automotive systems where accurate detecting of vibrations and shocks is critical.
Piezoelectric Accelerometers
Piezoelectric accelerometers are based on the piezoelectric effect, where certain materials generate an electric charge in response to mechanical stress. They are especially useful in measuring dynamic acceleration, such as vibrations or shocks. Piezoelectric materials, such as quartz or ceramic, are typically used for the sensor elements in these accelerometers.
One of the primary advantages of piezoelectric accelerometers is their ability to handle high-frequency signals while maintaining good accuracy. However, they may not perform as well in static conditions, as they primarily measure changes in motion rather than steady acceleration. These devices are often utilized in aerospace applications, structural health monitoring, and any scenario where dynamic force measurement is essential.
Optical Accelerometers
Optical accelerometers represent a newer and more advanced type of acceleration measurement device. These utilize light and optical fibers to detect acceleration through the change in light path caused by motion. They are unique due to their ability to provide highly accurate and low-noise measurements, which are significant in sensitive applications.
While they can be more expensive and complex to manufacture, optical accelerometers can excel in environments where electromagnetic interference could affect performance. Their high precision and reliability make them attractive for use in research labs, space technology, and specialized industrial applications.
The choice of accelerometer type directly impacts measurement quality and application suitability.
In summary, each type of digital accelerometer has unique advantages and considerations. Selecting the right one requires understanding the specific needs of the application, accuracy requirements, and environmental factors. This knowledge allows for the optimal integration of accelerometer technology into devices and systems.
Construction of Digital Accelerometers
The construction of digital accelerometers is critical in determining their overall performance and application range. Understanding the design and components involved can help users appreciate how these devices function in various environments. There is a careful balance between cost, efficiency, and robustness in the manufacturing process. Each aspect of construction plays a significant role in how the accelerometers respond to motion and environmental factors.
Integrated Circuit Design
The integrated circuit design is a fundamental part of digital accelerometers. It encompasses various microelectronic elements that interact to convert acceleration forces into digital signals. Typically, these circuits are designed to be compact and efficient. A well-designed integrated circuit can lead to increased sensitivity and reduced power consumption.
Some key considerations in IC design include:
- Signal Conditioning: Filtering out unwanted noise and amplifying the signal from the sensor is essential. This process includes analog-to-digital conversion, which is a core function of the circuit.
- Power Management: Efficient power consumption allows for longer battery life, especially in portable devices such as smartphones and IoT devices.
- Thermal Stability: The design must ensure consistent performance across a range of temperatures, as temperature variations can affect sensor readings.
Sensor Components
Sensor components form the heart of digital accelerometers. They react to accelerative forces and generate an output signal based on these movements. Various types of sensing technologies are used, including MEMS, capacitive, and piezoelectric sensors.
- MEMS Sensors: Microelectromechanical systems consist of tiny mechanical parts etched into silicon. They provide high sensitivity and are widely used in consumer electronics.
- Capacitive Sensors: These rely on changes in capacitance caused by acceleration forces. They are effective for low-frequency applications but can be sensitive to environmental changes.
- Piezoelectric Sensors: They generate an electric charge in response to mechanical stress. They are commonly used in dynamic applications where rapid changes occur.
Housing and Environment Protection
The housing of digital accelerometers is crucial for their performance and longevity. Proper housing protects internal components from physical damage, moisture, dust, and other environmental factors. Many accelerometers are used in harsh environments, such as automotive and aerospace settings.
Some important aspects of housing include:
- Material Selection: The housing is often made from materials like aluminum or plastic, depending on the requirements for weight, cost, and durability.
- Environmental Seal: Accelerometers must often be sealed to prevent the ingress of dust and moisture. This is particularly vital in automotive applications where exposure to the elements is common.
- Mounting Mechanisms: Proper mounting ensures that the accelerometer remains stable during operation. This stability directly affects the accuracy of the measurements.
"The careful construction of digital accelerometers ensures they meet the demands of various industries, from consumer electronics to aerospace."
In summary, the construction of digital accelerometers involves an intricate interplay of design, materials, and technology. Each of these elements contributes to the device's overall capability to provide accurate and reliable acceleration measurements. Understanding these components is paramount for those involved in technology, engineering, and related fields.
Operational Mechanisms
Understanding the operational mechanisms behind digital accelerometers is crucial. These instruments play a vital role in various aplications by providing accurate measurements of acceleration. Understanding how they function allows for optimal use in both design and practical scenarios.
How Digital Accelerometers Work
Digital accelerometers are designed to measure acceleration by using specific physical phenomena. Typically, they detect changes in motion through microelectromechanical systems (MEMS). When the device experiences an acceleration, a mass inside the accelerometer shifts. This movement causes a change in capacitance, which the sensor can measure.
The core components consist of a proof mass, springs, and sensors to detect the mass's displacement. The measured displacement of the mass is then converted into an electrical signal, representing the acceleration. This process ensures accurate and timely readings crucial for applications ranging from smartphones to automotive systems.
Signal Processing Techniques
Once the digital accelerometer captures the acceleration data, it requires signal processing. Signal processing is essential for distilling useful information from the raw data. Various techniques are utilized, including filtering, amplification, and digital signal processing algorithms.
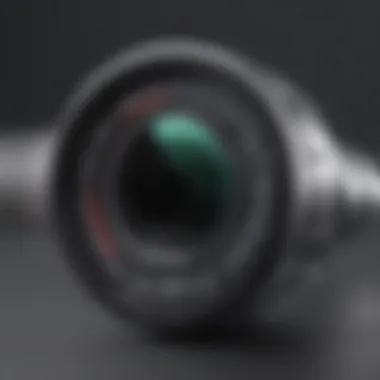
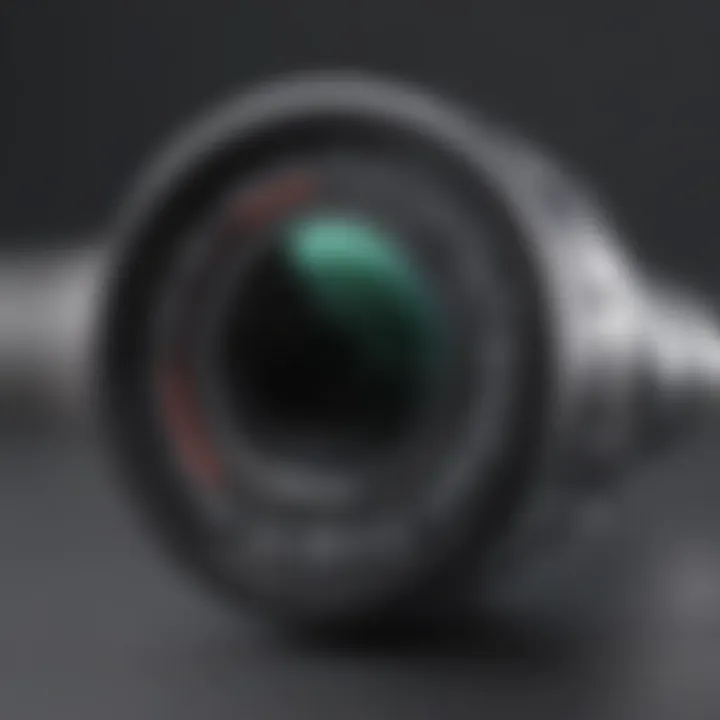
- Filtering: This reduces unwanted noise that can distort the signal.
- Amplification: Enhances the strength of the signal for better detection.
- Digital Signal Processing (DSP): This technique utilizes algorithms that can perform complex calculations in real-time, improving the accuracy and reliability of the data.
An effective signal processing strategy therefore ensures that the output is meaningful and actionable.
Data Output Formats
Data output formats vary widely, depending on the application and the design of the accelerometer. Most digital accelerometers output data in a few standard formats. These can include binary data, analog signals, or digital communication protocols such as I2C or SPI.
- Binary Data: Often used for basic applications where simple measurements are sufficient.
- Analog Signals: Useful in environments where real-time output is necessary.
- Communications Protocols: Such as UART and CAN, provide flexibility and compatibility with various systems.
Selection of data output format influences how easily the data can be integrated into broader systems. Each format serves specific needs, allowing for integration in diverse domains, from consumer electronics to industrial machinery.
Understanding the operational mechanisms behind digital accelerometers will aid engineers and researchers in optimizing their designs and applications for enhanced functionality.
Calibration and Accuracy
Calibration and accuracy are pivotal concepts in the realm of digital accelerometers. These elements serve not only to collect data but to ensure that the data remains trustworthy and applicable across various fields. Digital accelerometers, like any precision instrument, require careful calibration to provide accurate measurements of acceleration forces. Calibration establishes a relationship between the raw output of the accelerometer and the actual measurement it is intended to record. Without proper calibration, even the best accelerometer may yield outputs that are inaccurate or unreliable, leading to potential mishaps in applications where precision is crucial.
Importance of Calibration
Calibration is essential for numerous reasons. Firstly, it enhances the reliability of the measurements. An accelerometer that is routinely calibrated can mitigate drift in its readings over time, which is critical for applications that demand continuous data monitoring. Secondly, calibration assures compliance with industry standards. Many sectors such as aerospace and automotive have stringent regulations about data accuracy, making calibration a necessary step in meeting these requirements. Thirdly, it facilitates troubleshooting. By establishing a baseline through calibration, one can easily identify deviations in sensor performance that may indicate underlying issues or malfunctions.
Calibration Methods
Several methods can be employed to calibrate digital accelerometers. One common approach is static calibration, where the accelerometer is placed in a known orientation, often at rest or under a controlled acceleration. By comparing the output to expected values, adjustments can be made. Another method is the dynamic calibration, where the accelerometer is subjected to known dynamic movements, allowing for more robust testing under real-world conditions.
Other techniques include:
- Factory Calibration: Conducted before the unit leaves the manufacturing facility; however, recalibration may be necessary over time.
- Field Calibration: Performed on-site to ensure ongoing accuracy in actual operating conditions.
- Software Calibration: Utilizing algorithms to adjust the data output based on feedback mechanisms nurtured through machine learning and sensor fusion.
Factors Affecting Accuracy
Several factors can influence the accuracy of digital accelerometers. Environmental factors play a significant role. Temperature variations can affect the materials within the sensor, resulting in drift. Similarly, mechanical vibrations, which occur during usage, can introduce noise into the measurement, misleading the sensor output.
Additionally, sensor bias β a continuous offset in the measurement β can affect the accuracy. Sensor bias can arise from manufacturing imperfections or operational wear over time. Other important factors include:
- Resolution of the sensor: Higher-resolution sensors provide more accurate readings.
- Signal noise: Electrical noise can interfere with the measurement, impacting output quality.
- Aging effects: Components may degrade over time, affecting performance and reliability.
In summary, understanding calibration and accuracy is vital for ensuring that digital accelerometers deliver reliable and precise measurements. By maintaining strict calibration routines and being aware of the various factors that can affect performance, one can unlock the full potential of these sophisticated instruments.
Reducing Noise and Enhancing Performance
Noise in digital accelerometers can significantly impact their output accuracy and reliability. Addressing this topic is crucial as it influences the overall performance of these instruments in various applications. Accelerometers are used in fields like consumer electronics, automotive systems, and aerospace, where precision is paramount. Thus, understanding how to reduce noise leads to improved data quality and device functionality. This section focuses on the types of noise specifically affecting digital accelerometers and techniques to reduce it.
Types of Noise in Accelerometers
Accelerometers encounter various noise types, which can obscure the actual acceleration signals. These noises can be broadly classified into the following categories:
- Thermal Noise: This type originates from the natural vibrations of atoms in the sensor components, which can introduce random variations in the output signal.
- Shot Noise: Resulting from the quantized nature of electric charge, shot noise can be more prominent in low-signal environments.
- Vibration Noise: External vibrations create interference, leading to inaccuracies in measuring genuine acceleration.
- 1/f Noise: This noise, also known as flicker noise, increases at lower frequencies and can be a substantial factor in long-term measurements.
These noise types highlight the inherent challenges faced by digital accelerometers in capturing accurate data, which makes the understanding of methods to mitigate them even more critical.
Noise Reduction Techniques
Mitigating noise involves several techniques that can enhance the accuracy and reliability of the measurements provided by digital accelerometers. Some effective strategies include:
- Signal Filtering: Applying digital filters can help eliminate unwanted frequencies from the signal, allowing the desired acceleration signal to stand out.
- Signal Averaging: This technique reduces random noise by averaging multiple readings over time. The result improves the signal-to-noise ratio, yielding more reliable data.
- Shielding: Physical shielding of the sensor against environmental noise can also be beneficial. This includes housing designs that minimize exposure to external vibration sources.
- Temperature Control: Maintaining stable operating conditions can reduce the impact of thermal noise on sensor accuracy.
- Calibration and Compensation: Regular calibration can help account for specific noise characteristics inherent to the accelerometer. Additional compensation algorithms can adapt the system to mitigate known disturbances.
- Low-pass filters are commonly used to block high-frequency noise while preserving the signal of interest.
- High-pass filters can help in eliminating low-frequency noise effects.
Incorporating these techniques can significantly enhance the performance of digital accelerometers, making them critical tools for accurate measurements in advanced technological applications.
"Reducing noise is essential for ensuring that digital accelerometers deliver data that is both accurate and reliable across various applications."
Applications of Digital Accelerometers
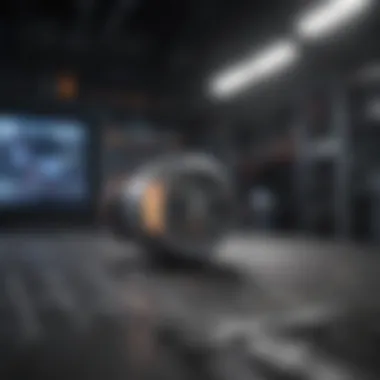
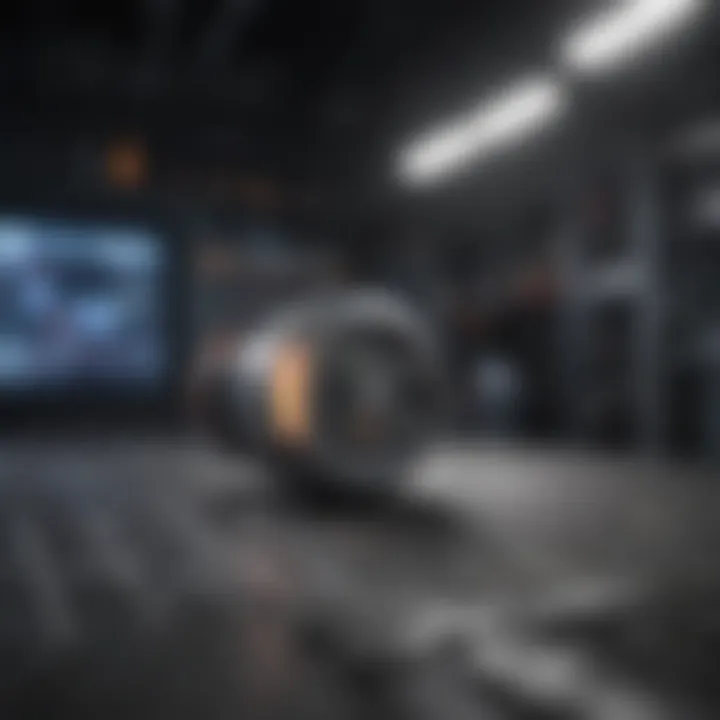
Digital accelerometers serve a crucial role in various technological applications. As instruments that measure acceleration forces, they find use in numerous fields due to their ability to deliver precise and real-time data. Understanding these applications enhances our grasp of how digital accelerometers influence modern technology and society.
Consumer Electronics
In consumer electronics, digital accelerometers are foundational. They provide an interface in devices such as smartphones and tablets. For example, as a user rotates or tilts their device, the accelerometer detects these movements, allowing the interface to adjust. This interaction improves user experience significantly. It also enables features such as screen auto-rotation, shake-to-undo, and game control enhancements.
Moreover, wearables like fitness trackers utilize accelerometers to monitor physical activity. They can measure steps taken, distance traveled, and even sleep patterns. This data is important for health-conscious individuals aiming to track their fitness journey.
Automotive Systems
In the automotive sector, digital accelerometers are vital for vehicle safety systems. They are integrated into airbag deployment mechanisms. When a collision occurs, the accelerometer detects rapid deceleration, triggering airbags to deploy instantly. This can save lives and reduce injury severity.
Additionally, accelerometers contribute to advanced driver-assistance systems (ADAS). Features like electronic stability control and traction control rely on data from these sensors. They help maintain vehicle stability by detecting changes in motion and adjusting accordingly.
Aerospace and Aviation
The aerospace industry employs digital accelerometers for navigation and stability. In aircraft, these sensors monitor acceleration and orientation. They provide critical data that assists in flight control systems. This data ensures operational safety, especially in turbulent conditions.
In satellites, accelerometers facilitate attitude control. By measuring how a satellite moves through space, engineers can correct its position, maximizing functionality. This application demonstrates the importance of accelerometers in both manned and unmanned missions.
Industrial Applications
Industrial automation also benefits from digital accelerometers. They are used in machinery monitoring systems. By measuring vibrations or irregular movements, businesses can predict equipment failures and schedule maintenance. This predictive maintenance can save companies substantial costs associated with unplanned downtime.
In robotics, accelerometers assist in navigation and stability. They help robots detect changes in their environment, allowing for precise movements. This capability is essential for various applications, from manufacturing to service robots in hospitality.
The adaptability of digital accelerometers across different industries highlights their significance in modern technology, making them essential tools for enhancing safety and efficiency.
Future Trends in Digital Accelerometers
In recent years, digital accelerometers have gained significance across various industries and sectors. Understanding the future trends in this technology is essential, as it indicates how these devices may evolve in capabilities, applications, and integration into larger systems. This section highlights the importance of staying abreast of advancements in digital accelerometers, focusing on their technological innovations, the integration with Internet of Things (IoT), and the evolving standards and regulations that govern their use.
Technological Innovations
The rapid pace of technological advancements greatly impacts digital accelerometers. Innovations continue to refine the sensitivity, accuracy, and miniaturization of these devices. New materials, such as advanced polymers and composites, are being explored to enhance performance while reducing weight.
Further, developments in microelectromechanical systems (MEMS) technology have led to more compact designs, making them ideal for modern applications. Increased computational capabilities allow accelerometers to perform complex signal processing internally, reducing the need for external processing units and enabling faster response times. These innovations result in devices that are not only more efficient but also more adaptable to various environmental conditions.
Examples of innovations include:
- Improved noise filtering techniques
- Enhanced energy efficiency for longer battery life
- Advanced calibration methods that increase accuracy
Integration with IoT
The integration of digital accelerometers with the Internet of Things (IoT) is reshaping how they are utilized. As more devices connect to the internet, accelerometers play a crucial role in providing real-time data critical for various applications. This connectivity allows for better monitoring and analysis in various settings, affecting everything from consumer electronics to industrial automation.
For instance, in smart homes, accelerometers can detect movement, enabling security systems to function efficiently. In industrial settings, they help with predictive maintenance by analyzing vibrations in machinery to anticipate failures. This trend not only enhances functionality but also provides higher levels of automation and insights from data analytics.
"The fusion of digital accelerometers with IoT is a leap towards smarter systems across multiple industries, ranging from healthcare to manufacturing."
Evolving Standards and Regulations
As digital accelerometers are integrated into more critical applications, evolving standards and regulations are of paramount importance. Regulatory bodies are continuously updating guidelines to ensure safety, accuracy, and reliability. The increasing use of these devices in health monitoring systems, aerospace, and automotive industries necessitates stringent compliance with international standards.
Maintaining awareness of these regulations is crucial for manufacturers and developers. Adhering to updated norms fosters consumer trust and encourages innovation without compromising safety. The focus is shifting toward not only meeting or surpassing current standards but also anticipating future regulations that may require even greater reliability and accuracy from digital accelerometers.
End
In summary, the role of digital accelerometers is fundamental to many technological disciplines. Their ability to accurately measure acceleration opens new opportunities across industries like automotive, aerospace, and consumer electronics. Understanding the processes involved in their calibration and signal processing enhances their effectiveness and reliability. Digital accelerometers improve not only the safety of vehicles but also the effectiveness of industrial machinery. This article has provided insights into various types, operational mechanisms, and applications of these devices, emphasizing their critical contributions to modern technology.
Summary of Key Points
- Digital accelerometers measure acceleration forces effectively.
- Different types include MEMS, capacitive, piezoelectric, and optical accelerometers.
- Proper calibration is essential for accurate data capture.
- Noise reduction techniques ensure improved performance.
- Applications span consumer electronics, automotive systems, aerospace, and various industrial uses.
Final Thoughts on Digital Accelerometers
As we look to the future, it is clear that digital accelerometers will continue to evolve. The integration with IoT devices will enhance data collection and analysis. Innovations in technology will likely lead to further miniaturization and improved accuracy. Keeping abreast of these advancements will benefit professionals and researchers alike. Understanding digital accelerometers is, therefore, not just about current applications but also about anticipating future developments.
"The significance of digital accelerometers lies not just in their function, but in their capacity to enable innovative solutions across diverse fields."
For those seeking further knowledge on this subject, resources like Wikipedia, Britannica can provide valuable information.