Aluminium 7075: Properties, Applications, and Challenges
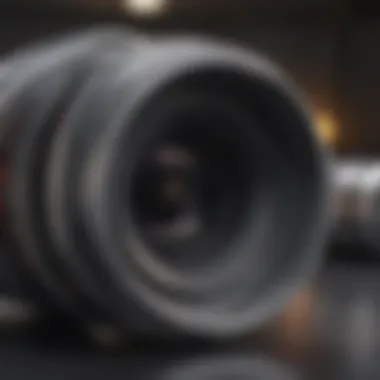
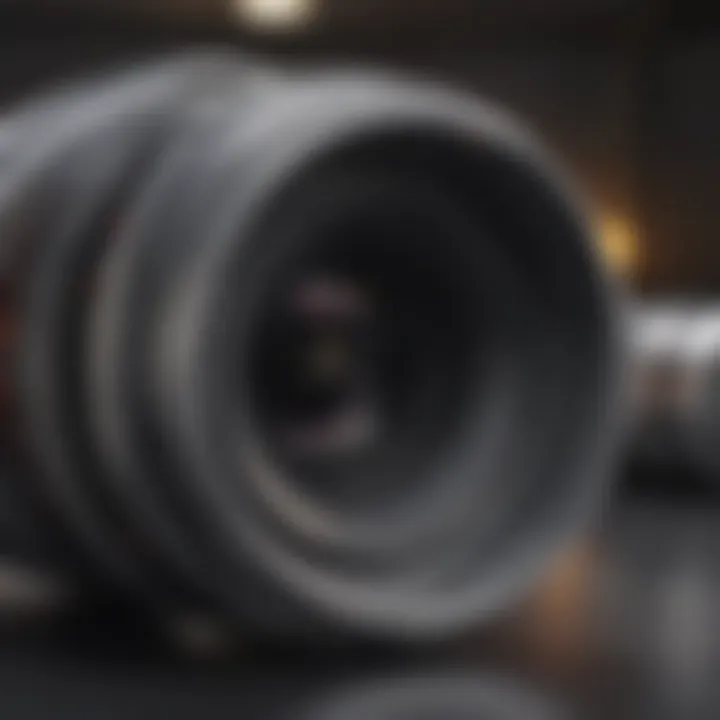
Intro
Aluminium 7075, a high-strength aluminium alloy, stands out due to its unique properties and remarkable versatility. Often termed as the backbone of high-performance applications, this alloy is extensively utilized across numerous industries, from aerospace to automotive. Its characteristics make it an essential material in engineering, where weight and strength are critical factors.
This contemporary narrative aims to elaborate on the intricate nature of Aluminium 7075, discussing its metallurgical nuances, performance determinants, and an evaluation of its significance in the engineering realm. By taking a comprehensive approach, we will explore how advancements in technology are shaping the future of this alloy, all while keeping the challenges of processing and application in mind. We expect that readers will gain an enriched understanding of Aluminium 7075, discovering not just its capabilities but also its vital role in modern design and construction practices.
Through a detailed analysis, we will navigate the complexities of working with Aluminium 7075, fostering a deeper appreciation for its applications. The conversation begins by outlining the methodology involved in our examination of this alloy.
Foreword to Aluminium
Aluminium 7075 has carved a niche in the realm of materials science due to its high strength-to-weight ratio. It is particularly treasured in industries where reliability and performance are non-negotiable. An understanding of this alloy, therefore, becomes crucial for students, researchers, and professionals navigating fields that demand robustness, such as aerospace and automotive engineering.
When discussing Aluminium 7075, one finds that the elements that contribute to its properties—primarily zinc, magnesium, and copper—combine to yield a substance that stands out even among other aluminium alloys. This section lays the foundation for a comprehensive exploration of how these elements interplay to create an alloy that exhibits exceptional toughness and fatigue resistance, making it a prime choice in competitive industries.
Overview of Aluminium Alloys
Aluminium alloys can be broadly categorized into two major groups: wrought and cast. Wrought aluminium undergoes mechanical processes such as rolling or extruding. In contrast, cast aluminium is molded into shapes through pouring into forms.
However, within these categories lie myriad specifics. There are heat-treatable alloys, such as 7075, that allow finer control over the material's properties through processes like annealing. Then there are non-heat treatable alloys, which cannot be strengthened with heat but rather rely on work-hardening techniques. This distinction is vital for applications requiring specific performance standards.
One of the more intriguing aspects of aluminium alloys is how the addition of alloying elements alters physical and mechanical characteristics. For instance, adding silicon can enhance corrosion resistance, while copper can improve strength but might reduce ductility. This balance is essential for engineers to grasp, especially when selecting materials for high-performance applications.
Significance of Aluminium
The significance of Aluminium 7075 cannot be understated, as it serves as a critical material across various sectors. Its unmatched strength, comparable to that of many structural steel products, offers a clear advantage for applications where light weight can lead to substantial energy savings.
The aerospace industry, where efficiency and safety are paramount, utilizes Aluminium 7075 for components such as aircraft wings and fuselages. Its ability to withstand high stress while maintaining form makes it an industry front-runner. Similarly, in the automotive field, parts manufactured from this alloy contribute to vehicle performance, improving fuel efficiency through reduced weight.
"The use of Aluminium 7075 represents a convergence of engineering ingenuity and material science, continually pushing the boundaries of what's achievable in design and manufacturing."
Additionally, the adaptability of Aluminium 7075 lends it to military applications, where conditions can be unpredictable and reliability needs to be guaranteed. In essence, understanding Aluminium 7075 is not merely academic—it is a gateway into appreciating the intricacies of engineering design choices in high-stakes environments.
Chemical Composition of Aluminium
Understanding the chemical composition of Aluminium 7075 is crucial for various sectors that rely on this metal for its remarkable characteristics. The unique blend of elements determines the alloy’s physical properties, making it suitable for high-stress applications, such as aerospace and military projects. Unlike more common alloys, the specific ingredients in Aluminium 7075 enable it to achieve exceptional strength and resistance to corrosion, but also demand finer processing considerations. This section will carefully dissect the alloying elements, both primary and trace, to reveal how they contribute to the overall functionality and reliability of Aluminium 7075.
Primary Alloying Elements
The primary alloying elements in Aluminium 7075 largely include zinc, magnesium, and copper, each serving distinct roles that enhance the overall performance of the alloy.
- Zinc (Zn): This is the cornerstone element that boosts the strength of Aluminium 7075 significantly. Zinc, usually found in concentrations around 5.1 to 6.1%, not only improves yield and ultimate tensile strength but also enhances stress corrosion resistance, making it suitable for harsh environments.
- Magnesium (Mg): With about 2.1 to 2.9% magnesium, this element works hand-in-hand with zinc to fortify the alloy, promoting a remarkable strength-to-weight ratio. This is prized in applications needing both lightness and robustness, such as in aerospace parts.
- Copper (Cu): Copper's presence, typically around 1.2 to 2.0%, introduces higher strength levels but at the cost of corrosion resistance. Often regarded as a double-edged sword, it can result in the alloy more susceptible to room temperature stress corrosion cracking. Careful handling in processing becomes critical to mitigate this risk.
These primary elements form the backbone of Aluminium 7075’s unique characteristics. Their careful balance enables the alloy to deliver superior performance in high-demand environments.
Trace Elements and Their Effects
While primary alloying elements define the major properties of Aluminium 7075, trace elements also play a vital role, often influencing the material's behavior and properties subtly.
- Silicon (Si): Generally found in small amounts (around 0.4%), silicon can influence the fluidity of the alloy during the casting process. Its presence helps refine grain structure, which can impact properties like strength and toughness.
- Iron (Fe): Even in minute quantities (about 0.5%), iron can lead to the formation of iron-rich intermetallic compounds. While generally undesirable, careful control of its levels can minimize its negative impacts.
- Manganese (Mn): At about 0.3%, manganese aids in enhancing tensile properties and conductivity. It works to improve the resistance to corrosion and ensures that the alloy maintains integrity under pressure.
- Titanium (Ti): Present in around 0.2%, titanium helps to prevent grain growth, which is essential in maintaining mechanical properties during heat treatments.
These trace elements may seem insignificant, but they can tip the scales between superior performance and failure under load or environmental stress. Understanding their impacts is vital for engineers and designers who work with Aluminium 7075 in critical applications.
Key Takeaway: The chemical composition of Aluminium 7075, with its essential primary and trace elements, underscores its unparalleled strength and versatility across different industries. The meticulous balance of these elements is what elevates this alloy above its competitors.
Mechanical Properties
Understanding the mechanical properties of Aluminium 7075 is critical for its application across various industries. Mechanical properties denote how a material responds to applied forces, making this section essential for evaluating the alloy's performance in real-world conditions. This analysis not only highlights the notable strengths of Aluminium 7075, such as high tensile strength and excellent fatigue resistance, but it also covers its ductility and impact toughness, which are vital for safety and functionality in demanding environments.
Tensile Strength and Ductility
Tensile strength refers to the maximum amount of tensile (pulling) stress that a material can withstand before failure. With a tensile strength often exceeding 570 MPa, Aluminium 7075 stands out as one of the strongest alloys in its category. This exceptional strength is crucial in applications like aerospace and military manufacturing, where every component must handle significant loads. The alloy achieves this strength largely through careful alloying and processing methods, including heat treatment.
Ductility, on the other hand, is the measure of how much a material can bend or stretch without breaking. While Aluminium 7075 exhibits notable strength, its ductility can vary based on its temper. For instance, T651 temper shows a balance of strength and ductility, allowing for effective forming processes. The combination of high strength and adequate ductility enables engineers to design thinner, lighter structures that don’t compromise performance, crucial in the quest for efficiency.
Fatigue Resistance
Fatigue resistance describes a material's ability to withstand repeated loading cycles without developing cracks or failing. Aluminium 7075 excels in this area, making it an ideal candidate for applications subjected to cyclical stresses, such as in aircraft frames or automotive components. The fatigue limit, or endurance limit, indicates the maximum stress level a material can tolerate for an infinite number of cycles without failing.
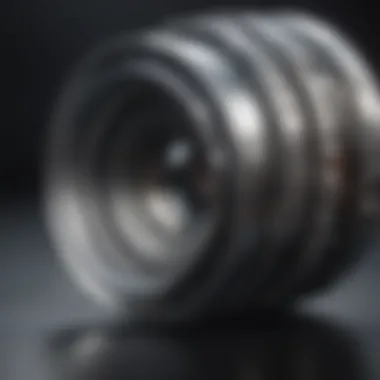
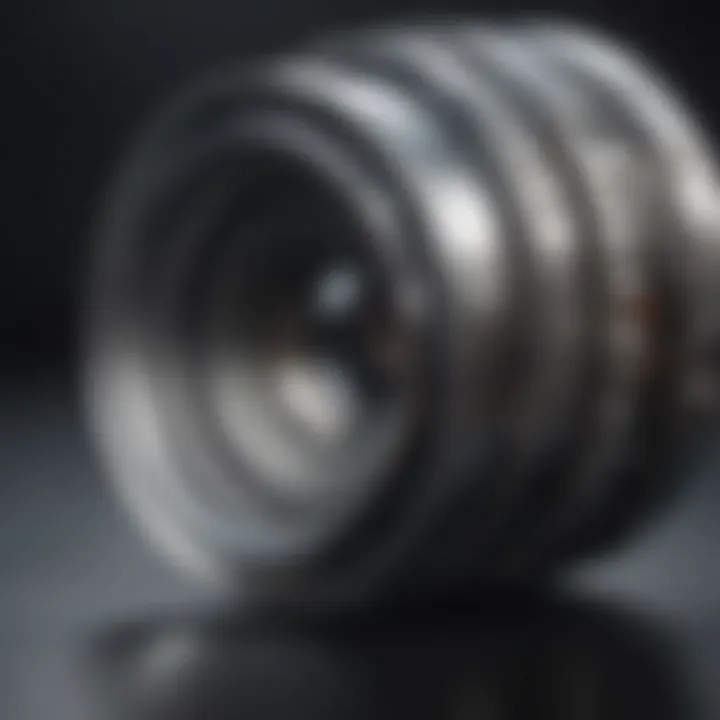
Factors influencing fatigue resistance in Aluminium 7075 include microstructural characteristics, alloying elements, and processing techniques. Proper heat treatment enhances its resistance to fatigue by refining grain structure and removing any potential defects that could initiate crack growth. Hence, producers focus on optimized processes to ensure the integrity of components is maintained even under strenuous conditions.
Impact Toughness
Impact toughness measures a material's ability to absorb energy during sudden impacts. This property is particularly important in situations where materials may experience shock loading or dynamic forces. Aluminium 7075, while primarily known for its strength, demonstrates adequate impact toughness, especially in variants designed for applications requiring high durability.
Material treatment plays a substantial role in impacting toughness. For example, 7075-T651 has been noted to display better impact toughness than some other high-strength alloys, which can become brittle under similar conditions. Engineers must carefully consider the working environment and potential impact loads when selecting Aluminium 7075, ensuring its properties align with the intended use.
In essence, understanding the mechanical properties of Aluminium 7075 is paramount in the engineering domain, influencing design choices that prioritize safety and performance.
Thermal Properties
Thermal properties play an essential role in understanding the behavior of materials like Aluminium 7075 under varying temperature conditions. The significance of examining these properties can't be overstated, particularly for industries where thermal stability and heat conductance are crucial for application performance. Factors such as thermal conductivity and heat treatment processes collectively affect the overall integrity and usability of this aluminum alloy.
Thermal Conductivity
Thermal conductivity refers to the ability of a material to conduct heat. In the case of Aluminium 7075, it exhibits decent thermal conductivity, which is important for applications where heat dissipation is necessary. This property becomes especially relevant in aerospace and automotive industries, where components are subjected to substantial heat loads.
- Aluminium 7075’s thermal conductivity typically ranges around 130 W/m·K, making it suitable for applications that require efficient thermal management.
- This level of conductivity helps in distributing heat evenly, thereby preventing local overheating, which can lead to thermal stresses and eventual material failure.
Using Thermal Conductivity in calculations can yield insights not just about performance under heat but also about how the material interacts with other structural components.
"Aluminium’s lightweight nature combined with its thermal conductivity makes it an ideal choice for precision components in environments with fluctuating temperatures.”
Heat Treatment Processes
Heat treatment is a vital step that can drastically alter the physical and mechanical properties of Aluminium 7075. The primary methods involve solution heat treatment, aging, and quenching. Each has a unique impact on the material’s performance and usability:
- Solution Heat Treatment: In this phase, the alloy is heated to a temperature where the alloying elements dissolve into a solid solution, which is then cooled rapidly. This is critical for enhancing strength.
- Aging: Following the solution heat treatment, the alloy is aged, either naturally or artificially. This process allows for the precipitation of secondary phases that strengthen the alloy through a fine-tuning of the microstructure.
- Quenching: Rapid cooling in water or oil significantly alters the structure, locking in the desired properties.
The success of these processes often relies on maintaining precise temperature controls and times, reflecting the thermal properties of Aluminium 7075. Engineers need to be particularly adept at choosing the correct treatment parameters to achieve optimal results for specific applications.
- The right heat treatment can enhance tensile strength by up to 200 MPa.
- Understanding how heat treatment impacts thermal stability can lead to better design and construction of components that are both light and capable of withstanding high thermal loads.
Applications of Aluminium
Aluminium 7075, known for its exceptional strength-to-weight ratio and unique properties, changes the game in various fields. Its importance cannot be overstated, especially when you consider its critical applications that drive innovation and efficiency. From aerospace to military uses, the applications of Aluminium 7075 represent a cornerstone of modern engineering. Let’s dive deeper into specific sectors where this aluminium alloy shines and understand the specific elements and benefits that make it a choice material.
Aerospace Industry
When it comes to the aerospace realm, every ounce matters. Aluminium 7075 is heavy in demand due to its lightweight nature coupled with remarkable strength. Aircraft manufacturers look for materials that not only enhance performance but also ensure safety and reliability. 7075 aluminium excels in providing both, often being the preferred choice for critical aircraft components such as:
- Wings and fuselages
- Landing gear
- Aircraft frames
Using 7075, manufacturers can achieve significant weight savings, thus improving fuel efficiency and payload capacity. The alloy shows excellent resistance to stress-corrosion cracking, an essential factor given the harsh environments aircraft often experience.
Automotive Engineering
In the automotive world, weight reduction is essential for improving fuel efficiency and handling. Aluminium 7075 steps up in various high-performance vehicles. The automotive industry is increasingly focused on innovative materials to enhance performance while being conscious of environmental impacts. Here are a few areas where Aluminium 7075 makes its mark:
- Structural components in race cars, including chassis and suspension systems
- Components in electric vehicles, where weight is crucial for battery efficiency
Aluminium’s ability to be formed into complex shapes allows engineers to optimize designs that can withstand high stress without adding unnecessary weight, making it an invaluable asset in modern automotive engineering.
Military Applications
In military applications, the stakes are high. The need for robust yet lightweight materials has never been more critical. Aluminium 7075 is commonly employed in the defense sector for manufacturing high-stress components that must perform reliably under extreme conditions. Some typical uses include:
- Aircraft and helicopter structures
- Weapon systems and accessories
- Armored vehicles
The industry favors 7075 for its superior strength and durability. Moreover, its resistance to corrosion is highly valued for equipment that operates in severe environments. Selecting the right materials in the military realm can mean the difference between success and failure in high-pressure situations.
The significance of Aluminium 7075 shines through in its diverse applications across critical sectors. Each application not only showcases the alloy's unique properties but also highlights the ongoing shift towards optimizing performance and efficiency in industries that shape our world.
Through these varied applications, Aluminium 7075 proves itself not just as a material but as a key player in advancing technology and innovation, making it a focal point in engineering discussions.
Comparison with Other Aluminium Alloys
Understanding Aluminium 7075 requires a nuanced look at how it stacks up against other aluminum alloys. This section is significant as it draws critical comparisons that provide insight into the advantages and limitations of Aluminium 7075 in various applications. With a spectrum of aluminum alloys available, it’s crucial to highlight what sets 7075 apart and why certain industries opt for it over others, especially when performance and durability are priority factors.
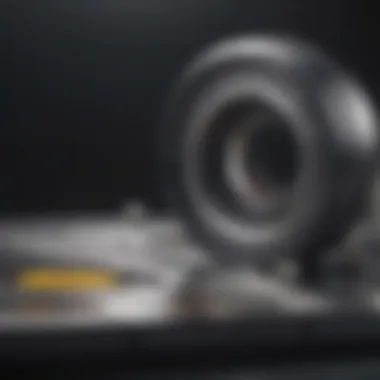
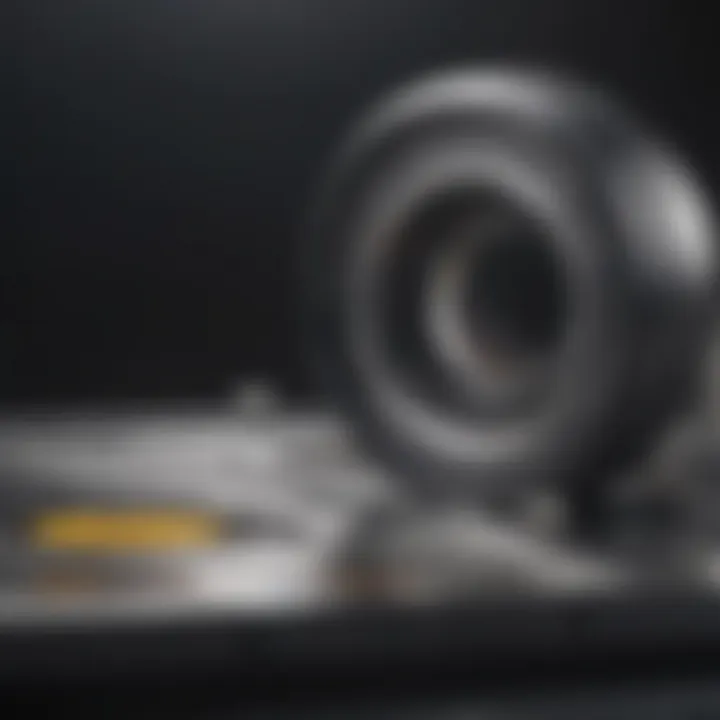
Aluminium vs. Aluminium
When discussing Aluminium 6061 and Aluminium 7075, one can’t help but notice their differing characteristics and applications. Aluminium 6061 is often praised for its excellent corrosion resistance, medium strength, and good workability. It's commonly used in structural applications, such as building frames and marine parts. On the flip side, Aluminium 7075 is recognized for its superior strength-to-weight ratio, making it a top choice in critical components, particularly in aviation and defense sectors.
Key Differences:
- Strength: 7075 provides a significantly higher tensile strength—about 150 % that of 6061.
- Workability: 6061 is more malleable, which means it's easier to weld and forge.
- Applications: 7075 is typically found in high-stress applications, whereas 6061 is versatile for moderate loads and extensive fabrications.
In situations where weight must be minimized without sacrificing integrity, Aluminium 7075 takes the lead. This aspect is crucial in industries where performance directly correlates with safety and efficiency, like aerospace. A good example can be drawn from the structural components of aircraft, which frequently utilize 7075 to achieve lighter designs without compromising strength.
"Selecting the right alloy is like choosing the right tool for the job—getting it right can make or break the outcome."
Aluminium vs. Aluminium
Comparing Aluminium 2024 with Aluminium 7075 opens another perspective on alloy properties. Both alloys are favored in aerospace applications, yet they cater to slightly different needs. While 2024 delivers great fatigue resistance and is often preferred for aircraft structures, 7075 tops the chart when discussing ultimate strength.
Considerations include:
- Fatigue Resistance: 2024 exhibits better fatigue performance under cyclic loading, making it suitable for aircraft skins.
- Corrosion Resistance: Similarly, 2024 has decent corrosion resistance with appropriate coating. In contrast, 7075, being heat-treated, may require more attention to environmental factors due to its susceptibility to corrosion.
- Formability: Again, 7075 is tougher to form compared to 2024, owing to its higher strength.
The distinction between 2024 and 7075 material choices often lies in specific engineering demands—whether it’s needing that raw strength or resilience in fatigue and longevity of application. Engineers play a vital role in this choice, ensuring the right alloy aligns with the mechanical requirements and environmental conditions expected in service life. The relationship between these alloys highlights the importance of understanding material properties and their application contexts, ensuring optimal performance in engineering processes.
Challenges in Processing
The processing of Aluminium 7075 presents a variety of challenges that industry professionals must navigate. This section shines a spotlight on these difficulties—specifically in machining and welding—due to their relevance in shaping the material's applications and its overall performance in various sectors. Understanding these challenges is crucial because they can influence the effectiveness, efficiency, and ultimately the cost of manufacturing components made from Aluminium 7075.
Machining Difficulties
Machining Aluminium 7075 can often feel like threading a needle in dim light. While the alloy is renowned for its strength and durability, these very properties can complicate machining processes. The hardness of Aluminium 7075 means that it wears down cutting tools quicker than softer alloys like 6061. This translates into more frequent tool changes, which naturally inflates production costs and timelines.
- Tool Selection:
- Cutting Speeds:
- Chip Removal and Cooling:
- Using carbide tools is frequently recommended, as they endure higher temperatures and resist wear.
- High-speed steel tools might fall short in performance when working with 7075, leading to poorer finish qualities.
- Finding the sweet spot for cutting speeds can be tricky. Too slow, and you lose productivity; too fast, and you risk tool damage or poor surface finish.
- Effective chip removal is essential to avoid re-cutting material. This might necessitate specialized equipment or setup. Additionally, using proper coolant to manage heat dissipation helps in sustaining tool life and maximizing machining efficiency.
In summary, while machining Aluminium 7075 is not impossible, it does demand a more sophisticated approach compared to other alloys. The precision required during this stage sets the tone for the end product.
Welding Characteristics
Welding Aluminium 7075 poses its own set of hurdles, making it a less favorable choice for certain applications. The alloy’s high strength and low crack susceptibility do allow it to perform well in various scenarios, but there are nuances to consider that can directly affect the integrity of welds.
- Alloy Composition:
- Pre-Weld Preparation:
- Welding Techniques:
- Post-Weld Treatments:
- The presence of zinc as a primary alloying element can lead to a tendency for burning or cracking during the welding process.
- Proper surface preparation is paramount. Grease, oil, and other contaminants must be thoroughly removed to ensure maximum weld quality.
- Both gas tungsten arc welding (GTAW) and gas metal arc welding (GMAW) can be employed, but the choice between them hinges on various factors, including thickness of the material and the desired finish.
- Stress relief treatments are often recommended after welding to relieve residual stresses that can lead to cracking over time.
Understanding the challenges associated with welding Aluminium 7075 is necessary for ensuring structural integrity and satisfying performance in applications that demand strength.
Innovations and Technological Advances
The landscape of Aluminium 7075 is continually changing, driven largely by innovations and advancements in technology. This part covers innovative practices and breakthroughs that are reshaping how Aluminium 7075 is produced, processed, and utilized across various industries. These advances offer not just improvements in material performance but also open pathways for sustainability and efficiency in manufacturing.
New Alloying Techniques
Recent developments in alloying techniques have revolutionized the production of Aluminium 7075. Traditionally, the alloy was known for its impressive strength-to-weight ratio, but new methods have enhanced its properties further.
For instance, the introduction of thermodynamic modeling throughout the alloy design phase has allowed engineers to predict the behavior of Aluminium 7075 under various conditions more accurately. Improved alloying elements, such as added lithium, have shown promise in increasing strength while maintaining low density. The significance of such advancements can be summed up in the following points:
- Enhanced Mechanical Properties: New alloying combinations are resulting in better fatigue resistance and yield strength.
- Customization Abilities: Tailoring the alloying microstructure means specific performance criteria can be met more effectively based on application needs.
- Improved Consistency: Modern methods lead to a more homogeneous distribution of elements within the alloy, which results in more reliable performance.
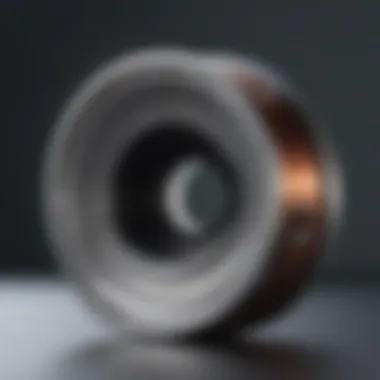
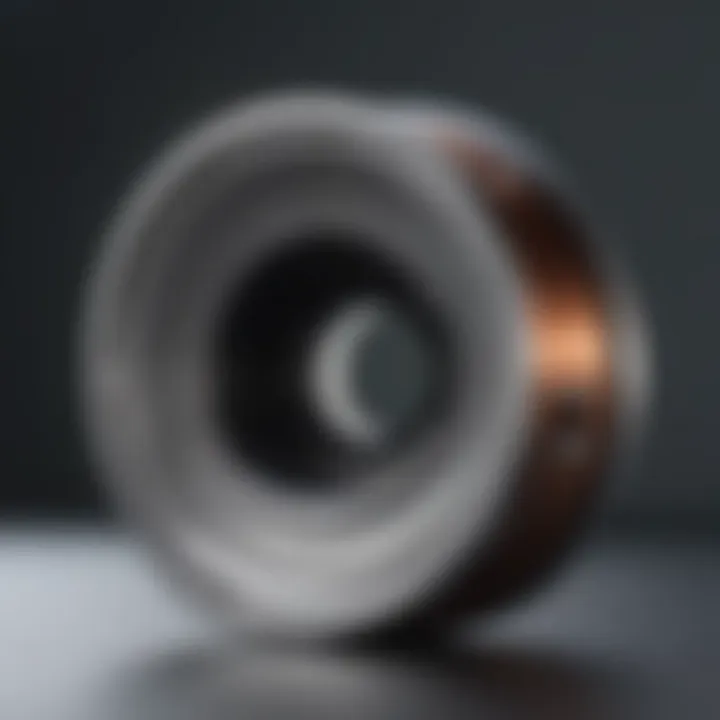
These innovations don't merely refine existing processes; they lay the groundwork for the future development of materials that meet the ever-increasing demands of industries such as aerospace and automotive—where performance and safety are paramount.
Advanced Manufacturing Processes
Technological strides in manufacturing processes have also made their mark on Aluminium 7075. Techniques like additive manufacturing are one of the standout innovations enabling manufacturers to create complex geometries with greater ease.
Moreover, advanced machining methods, such as high-speed machining (HSM), are increasingly becoming the go-to choice for working with Aluminium 7075. This has resulted in:
- Reduced Production Time: HSM significantly cuts down machining time, allowing for quicker turnaround from conception to production.
- Higher Precision: New tool designs and controls reduce the margin of error, ensuring components meet precise specifications.
- Less Waste: Improved machining leads to greater yield rates from raw material, which is financially beneficial and reduces environmental impact.
These advanced manufacturing techniques not only enhance the cost-effectiveness of production but also encourage sustainable practices. By leveraging such methods, manufacturers can reduce the carbon footprint often associated with traditional aluminium processing.
"The constant evolution in alloying techniques and manufacturing processes highlights the industry's commitment to innovation and sustainability, particularly in the context of Aluminium 7075."
Environmental Considerations
Aluminium 7075 plays a vital role in the discussions surrounding environmental sustainability in modern manufacturing practices. As industries aim to reduce their ecological footprints, understanding the environmental implications of materials is more crucial than ever. This section delves into two principal components: the recyclability of Aluminium 7075 and its contribution to sustainable manufacturing processes.
Recyclability of Aluminium
Aluminium 7075 is recognized for its excellent recyclability, which significantly contributes to reducing waste in landfills. Unlike many materials that lose properties once recycled, Aluminium alloys like 7075 can be re-melted and reformed with almost no degradation in quality. This characteristic makes it a prime candidate for recycling endeavors.
- Energy-efficient recycling: Recycling Aluminium requires only about 5% of the energy needed to produce new metal from ore, showcasing substantial energy savings. This process conserves resources and reduces greenhouse gas emissions.
- Closed-loop recycling: Industries utilizing Aluminium 7075 can benefit from closed-loop systems where scrap material from one project is reused in another, minimizing waste.
- Long life cycle: The substantial lifespan of products made from Aluminium 7075 also means that, after their use, they can be reincarnated into new applications without losing strength or durability.
In essence, the recyclability of Aluminium 7075 not only helps in conserving energy but also diminishes the extraction pressure on natural resources. This shift towards circular economics is necessary for a sustainable future.
Impact on Sustainable Manufacturing
The use of Aluminium 7075 in manufacturing processes has notable implications for sustainability. By integrating this alloy into production, companies can adopt practices that reflect environmental responsibility.
- Lightweight benefits: Due to its high strength-to-weight ratio, Aluminium 7075 enables manufacturers to design lighter components. This is especially beneficial in industries like aerospace and automotive, where weight reduction can lead to decreased fuel consumption.
- Durability leads to longevity: Aluminium 7075's resilience means that products typically have a longer lifespan, which reduces replacement frequency and thus leads to a lower overall environmental impact over time.
- Innovations in processing: Advanced manufacturing methods developed for Aluminium 7075 can result in less waste and efficient material utilization, enhancing overall sustainability.
"Sustainable practices are no longer optional; they are essential for the future of manufacturing and the health of our planet."
As the global focus shifts toward eco-friendly alternatives, the advantages of Aluminium 7075 signify its importance not just from a performance standpoint but also as a crucial component in the sustainability conversation. By adopting such materials, industries are taking meaningful steps toward reducing their environmental impact.
Future Directions
Discussing the future directions for Aluminium 7075 is pivotal as it sheds light on how this alloy will evolve in changing industries, particularly in aerospace and automotive engineering. Improvements in material science not only open up new avenues for application but also enhance performance characteristics. As industries become increasingly competitive, innovations will increasingly demand advanced materials like 7075, which is prized for its strength-to-weight ratio.
Trends in Aerospace Applications
Aerospace is a field where every gram counts. That’s where Aluminium 7075 shines, providing the perfect balance of strength and weight. Recent trends show that there’s a growing shift towards using high-strength alloys to meet stringent safety and performance standards. 7075 is no stranger here, finding its place in critical applications such as aircraft structures and frames. Manufacturers are also exploring additive manufacturing techniques, where 7075 can be 3D printed for complex geometries that were previously challenging or impossible to achieve.
- Benefits of using Aluminium 7075 in aerospace include:
- Lightweight construction: Increases fuel efficiency.
- Enhanced strength: Provides necessary durability for high-stress environments.
- Corrosion Resistance: Ensures longevity of aircraft parts exposed to harsh conditions.
Some innovative companies are diving into hybrid materials, combining Aluminum 7075 with composites. This has the potential to not only lighten aircraft but also increase stiffness and resistance to fatigue, which is essential for the safety of modern air transport.
Emerging Markets and Uses
As Aluminium 7075 continues to gain accolades in aerospace, its applications are also evolving in other industries. Emerging markets in renewable energy, such as wind turbine construction, are catching on. The lightweight yet robust nature of 7075 makes it a prime candidate for turbine blades, enabling more efficient energy production.
Exploration into the automotive sector is yielding exciting developments as well. With the push for electric vehicles, weight reductions are crucial for battery efficiency. Manufacturers are increasingly considering Aluminium 7075 not just for chassis components but also for structural parts, showcasing its versatility.
"The potential of Aluminium 7075 is yet to be fully realized across various industries; its unique properties can redefine standards."
In addition, the advancement of nanotechnology holds promise for Aluminium 7075. Incorporating nanoparticles into the alloy could significantly improve its mechanical properties, paving the way for revolutionary applications in many fields. This ongoing research signals a bright future for 7075, where it can carve out more roles across different sectors.
- Key considerations for emerging uses of Aluminium 7075 include:
- Economic viability: Sourcing and production processes must remain cost-effective.
- Environmental impact: Sustainability in usage and manufacturing is crucial.
- Technological compatibility: The need for alignment with existing technologies and materials.
Ending
The conclusion in this discussion of Aluminium 7075 is vital as it encapsulates the essential insights garnered throughout the article. In today's rapidly evolving engineering landscape, Aluminium 7075 stands out due to its unique combination of properties that make it indispensable in numerous high-performance applications. Its exceptional strength-to-weight ratio, alongside notable fatigue resistance, renders it an ideal material for sectors like aerospace and automotive engineering.
Several specific elements underscore the importance of Aluminium 7075. First off is its versatility; it can be heat-treated to achieve various mechanical properties, catering to different requirements across industries. This ability allows for a more tailored approach to material selection, which is critical in mission-critical applications. More so, understanding the nuances of Aluminium 7075's chemical composition helps engineers optimize its use effectively. The precise role of alloying elements can be tailored through meticulous control during the manufacturing and heat-treatment processes.
Another key aspect that deserves attention is the environmental consideration related to Aluminium 7075. As industries shift towards sustainability, the recyclability of Aluminium 7075 poses an added benefit. When materials can be reused and reprocessed, it significantly reduces the environmental footprint, making it an attractive choice in a world where sustainability is increasingly a priority.
Moreover, this analysis has spotlighted future directions for Aluminium 7075 in various emerging markets. As advancements continue, we could see new applications springing forth, leveraging the specific benefits of this alloy. Understanding the current trends can prepare students, researchers, and professionals alike to adapt and innovate as new challenges arise.
In summary, the conclusion aligns all the crucial takeaways, reiterating that Aluminium 7075 is not just a material; it’s a cornerstone of modern engineering. As demands evolve, its role is set to become even more significant, ensuring it remains at the forefront of material science conversations. The insights presented here are more than mere facts; they are a call to leverage Aluminium 7075’s potential responsibly and thoughtfully in future endeavors.